Worm gear is critical components in many industrial machines, known for their ability to provide high torque at low speeds. However, optimizing these gear for longevity and performance while keeping costs manageable is a significant challenge. Here, we explore several cost-effective solutions for optimizing worm gear in industrial settings.
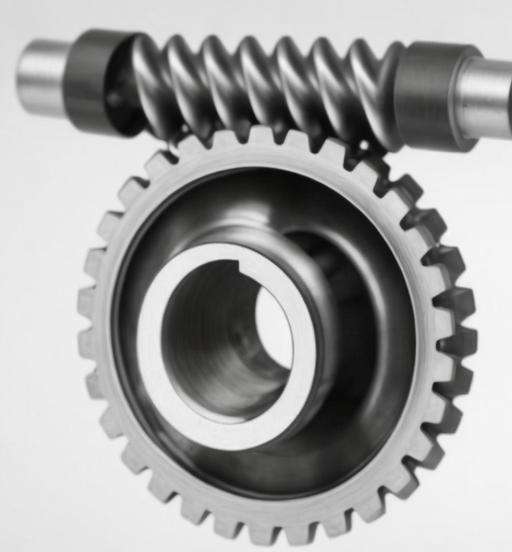
1. Regular Maintenance and Lubrication
Regular maintenance and proper lubrication are fundamental to extending the life of worm gear. Using high-quality lubricants that are specifically designed for worm gear can reduce friction and wear, leading to smoother operation and reduced maintenance costs.
2. Upgrading to Wear-Resistant Materials
Investing in wear-resistant materials can significantly enhance the durability of worm gear. Materials such as hardened steel or advanced composites offer better resistance to wear and tear. Although the initial cost may be higher, the extended lifespan and reduced downtime can justify the investment.
3. Implementing Condition Monitoring Systems
Condition monitoring systems help in early detection of wear and potential failures. These systems can include vibration analysis, acoustic emission sensors, and oil analysis. By identifying issues early, maintenance can be scheduled before a costly breakdown occurs, thus reducing unexpected downtime.
4. Applying Advanced Coatings
Advanced coatings such as tungsten carbide or diamond-like carbon (DLC) can provide additional wear resistance. These coatings reduce friction and increase the hardness of worm gear surfaces, resulting in longer service life and less frequent replacements.
5. Optimizing Gear Design
Optimizing the design of worm gear, including tooth profile and surface finish, can enhance performance and reduce wear. Using computer-aided design (CAD) and simulation tools, engineers can design worm gear that operate more efficiently and last longer.
6. Training and Skill Development
Investing in the training and skill development of maintenance personnel ensures that they are knowledgeable about the best practices for worm gear maintenance and optimization. Skilled technicians can identify potential issues more accurately and perform maintenance tasks more effectively.
Table: Cost-Effective Solutions for Worm Gear Optimization
Solution | Description | Benefits | Cost Consideration |
---|---|---|---|
Regular Maintenance and Lubrication | Scheduled maintenance and use of high-quality lubricants | Reduces friction and wear, extends life | Low to moderate |
Upgrading to Wear-Resistant Materials | Using materials like hardened steel or composites | Increases durability, reduces downtime | Higher initial cost, long-term savings |
Condition Monitoring Systems | Implementing sensors for vibration, acoustic, and oil analysis | Early detection of issues, prevents failures | Moderate to high, depending on system |
Advanced Coatings | Applying coatings like tungsten carbide or DLC | Reduces friction, increases surface hardness | Moderate initial cost, long-term benefits |
Optimizing Gear Design | Using CAD and simulation for better design | Enhances efficiency, reduces wear | Initial design cost, long-term savings |
Training and Skill Development | Educating maintenance personnel on best practices | Improves maintenance effectiveness | Moderate investment |
Conclusion
Optimizing worm gear in industrial settings doesn’t always require significant capital investments. By focusing on regular maintenance, using advanced materials and coatings, implementing condition monitoring systems, optimizing gear design, and investing in the training of maintenance personnel, industries can achieve substantial improvements in worm gear performance and longevity. These cost-effective solutions not only enhance the reliability of machinery but also lead to significant savings over time by reducing downtime and maintenance costs.