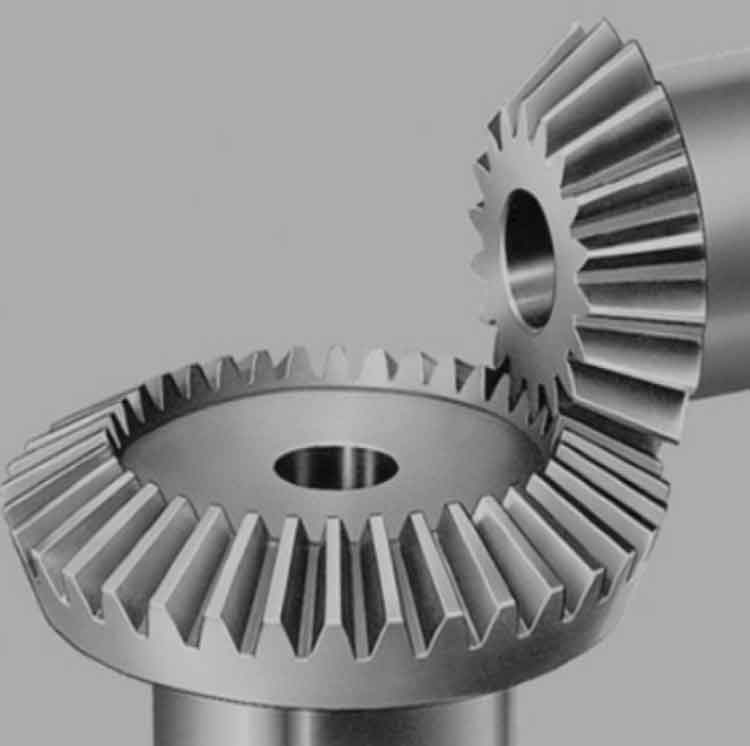
Ensuring the precision and quality of straight bevel gear is critical for their performance and longevity in various applications. This guide outlines the key inspection and quality control methods used in the production of straight bevel gear.
1. Introduction
Importance of Precision:
- Precision in gear production ensures efficient power transmission, reduces noise and vibration, and extends the lifespan of straight bevel gear.
- High precision is particularly crucial in applications such as automotive transmissions, aerospace, and industrial machinery.
Challenges in Gear Production:
- Complex geometries and tight tolerances require advanced manufacturing and inspection techniques.
- Consistency in production processes is necessary to maintain high quality across batches.
2. Inspection Methods
Dimensional Inspection:
- Coordinate Measuring Machines (CMM): Used for precise measurement of straight bevel gear dimensions, including tooth geometry, pitch, and alignment. CMMs provide high accuracy and can measure complex shapes.
- Gear Measuring Instruments: Specialized tools like straight bevel gear checkers and profile projectors are used to measure parameters such as helix angle, pitch diameter, and tooth thickness.
- Optical Measurement Systems: Utilize lasers and cameras to capture high-resolution images of straight bevel gear surfaces, allowing for non-contact measurement of dimensions and surface features.
Surface Finish Inspection:
- Surface Roughness Testers: Measure the surface finish of straight bevel gear teeth to ensure smooth operation and reduce friction. Common parameters include Ra (average roughness) and Rz (mean peak-to-valley height).
- Optical Profilometers: Provide detailed surface texture analysis using light interference, offering high precision in measuring surface roughness and defects.
Hardness Testing:
- Rockwell and Vickers Hardness Tests: Evaluate the hardness of gear materials and coatings. These tests involve indenting straight bevel gear surface with a specific force and measuring the depth or size of the indentation.
- Microhardness Testing: Used for evaluating thin surface layers or coatings, particularly useful for case-hardened gears.
Tooth Contact Pattern Inspection:
- Contact Pattern Testing: Applies a marking compound to straight bevel gear teeth and rotates the gears to visualize the contact pattern. This helps identify misalignment, uneven load distribution, and manufacturing defects.
- Digital Imaging: Captures high-resolution images of the contact pattern for detailed analysis and documentation.
Runout Measurement:
- Dial Indicators: Measure radial and axial runout to ensure straight bevel gear rotates true to its axis. Excessive runout can lead to noise, vibration, and premature wear.
- CMMs and Specialized Runout Gauges: Provide more precise and automated runout measurements.
3. Quality Control Methods
Statistical Process Control (SPC):
- Control Charts: Monitor critical dimensions and process parameters over time to detect trends and variations. Commonly used charts include X-bar and R charts for variables and p-charts for attributes.
- Process Capability Analysis: Assess the ability of a manufacturing process to produce straight bevel gear within specified tolerance limits (Cp, Cpk indices).
Non-Destructive Testing (NDT):
- Ultrasonic Testing: Uses high-frequency sound waves to detect internal defects such as cracks, voids, and inclusions without damaging straight bevel gear.
- Magnetic Particle Inspection (MPI): Detects surface and near-surface defects in ferromagnetic materials by applying a magnetic field and ferrous particles.
- Dye Penetrant Inspection (DPI): Identifies surface cracks and porosities by applying a liquid penetrant and developer.
Quality Management Systems:
- ISO 9001 Certification: Ensures that an organization meets international standards for quality management, covering all aspects of straight bevel gear production, from design to delivery.
- Continuous Improvement Programs: Implement methodologies such as Six Sigma and Lean Manufacturing to systematically improve processes and reduce defects.
Automated Inspection Systems:
- In-Line Inspection: Integrates inspection tools directly into the production line for real-time monitoring and feedback. Helps in immediate detection and correction of defects.
- Robotic Inspection Cells: Use robots equipped with sensors and measuring devices to perform automated, high-precision inspections.
4. Case Studies and Applications
Automotive Industry:
- High-Volume Production: Utilizes automated inspection systems and SPC to ensure consistency and precision in large-scale production of automotive straight bevel gear.
- Noise and Vibration Testing: Conducts extensive NVH (Noise, Vibration, and Harshness) testing to meet stringent performance standards.
Aerospace Industry:
- Stringent Quality Requirements: Employs advanced NDT methods and detailed dimensional inspections to ensure straight bevel gear meet the high safety and reliability standards required for aerospace applications.
- Material Certification: Ensures all materials used in straight bevel gear production meet specific aerospace standards and traceability requirements.
Industrial Machinery:
- Durability Testing: Performs accelerated life testing to simulate long-term operation and identify potential failure modes.
- Customized Quality Plans: Develops tailored quality control plans based on specific application requirements and operating conditions.
5. Conclusion
Ensuring Precision and Quality:
- A comprehensive approach combining advanced inspection methods, stringent quality control practices, and continuous improvement programs is essential to ensure the precision and quality of straight bevel gear.
- By leveraging state-of-the-art technologies and adhering to rigorous standards, manufacturers can produce high-quality straight bevel gear that meet the demanding requirements of various industries.
Future Trends:
- Smart Manufacturing: Integration of IoT and AI for predictive maintenance and real-time quality control.
- Advanced Materials: Development of new materials and coatings to enhance straight bevel gear performance and durability.
- Sustainable Practices: Adoption of environmentally friendly manufacturing processes and materials.
Implementing these inspection and quality control methods ensures that straight bevel gear meet the highest standards of precision and reliability, leading to improved performance and customer satisfaction.