This article comprehensively reviews the research status of gear fatigue crack initiation and propagation behavior. It introduces the main forms and causes of gear failure, summarizes the factors affecting gear fatigue strength, and discusses the types of gear cracks and the methods of crack initiation and propagation. In addition, existing simulation methods for gear fatigue cracks are summarized, and the microstructure mechanical behavior in gear fatigue is described. Finally, suggestions for avoiding gear cracks are provided.
1. Introduction
Gear transmission is one of the most widely used forms of mechanical transmission. It has the advantages of high transmission efficiency, accurate and stable transmission ratio, and a wide power range. However, gear fatigue failure often occurs, which seriously affects the performance and reliability of gear equipment. Therefore, it is of great significance to study the initiation and propagation behavior of gear fatigue cracks.
2. Gear Fatigue Failure
2.1 Main Modes of Gear Failure
In industrial gears with rough surfaces, surface pitting is mainly affected by surface roughness. It can lead to defects such as residual stress, fatigue, and surface cracking. Typical failure types include tooth fatigue fracture, working surface wear and pitting, gear surface bonding, and plastic deformation. The main failure modes are shown in Table 1.
Failure Mode | Failure Type |
---|---|
Fatigue | Tooth bending, surface contact (pitting), rolling contact or thermal fatigue |
Influence | Tooth bending, tooth shear |
Wear | Abrasive, adhesive |
Stress Failure | Internal, external |
The most common and typical fatigue failure forms are contact fatigue and bending fatigue. Contact fatigue is defined as a damage caused by the change of material microstructure under the influence of rolling or sliding contact loads over time, resulting in crack initiation and propagation. Gear tooth surface contact fatigue is one of the most common causes of gear operation failure due to excessive local Hertz contact fatigue stress. The causes of contact fatigue mechanism include local dislocation accumulation causing gear bending fatigue and microcrack generation, high load leading to gear bending fatigue fracture, and inhomogeneous inclusions or other defects in or under the contact surface causing plastic deformation around the gear. Bending fatigue is the fatigue failure phenomenon caused by the repeated pulsating bending load acting on the tooth root. The surface hardening treatment and residual stress of the gear will affect the gear bending fatigue. The tooth root is the key position of potential failure, and gear bending fatigue mostly occurs in the tooth root area.
2.2 Fatigue Damage Behavior Research
Gear materials require various processing technologies such as heat treatment, surface hardening, and grinding during processing and forming. These processes will generate some initial residual stresses. Initial residual compressive stress is beneficial to fatigue life, while initial residual tensile stress is not. Overload and different loading sequences will affect the residual stress. At present, wear and contact fatigue have become increasingly serious problems, and researchers have done a lot of research on the contact fatigue behavior of gears. Table 2 shows the typical literature on gear contact fatigue behavior research in recent years.
Year | Journal/Unit | Author | Review Content | Literature |
---|---|---|---|---|
2018 | ASME | Liu et al. | Calculated the sub-surface stress distribution of gears considering the influence of lubrication and surface roughness | [19] |
2012 | Faraday Forum | Evans et al. | Predicted gear contact fatigue based on tooth surface roughness | [20] |
2014 | ASME | Dong et al. | Studied the influence of temperature on gears based on elastohydrodynamic lubrication theory | [21] |
2018 | ASME | Zhu et al. | Evaluated the contact fatigue life of wind turbine gear pairs considering residual stress | [22] |
2019 | International Journal of Damage Mechanics | Wang et al. | Studied the rolling contact fatigue performance of wind turbine gears considering residual stress and hardness gradient | [23] |
In order to study the fatigue performance of gears, He et al. calculated and recorded the detailed evolution of gear material degradation and damage and stress response during cyclic loading based on continuum damage mechanics. They also calculated the stress fields in the gear contact area and tooth root area and evaluated the tooth surface contact fatigue and tooth root bending fatigue. The simulation results showed that the risk of gear surface contact fatigue failure is much greater than that of gear bending fatigue failure. Wang et al. combined crystal plasticity and continuum damage to describe the fatigue damage behavior of gear microstructure. By comparing the stress-strain responses (including shear strain amplitude, maximum normal stress, and normal strain amplitude) obtained from the model, the microstructure-sensitive model was verified. The verification results of the stress-strain response showed that in the early stage of gear service, the accumulation of contact fatigue is slow, and the damage increases sharply in the later stage. The bending fatigue damage is relatively flat throughout the process, and the grain orientation has an important influence on the type of gear fatigue failure.
It is crucial to detect fatigue damage in a timely manner. At present, most fatigue damage assessment methods use the acoustic nonlinearity of ultrasonic guided waves for detection. By detecting the acoustic emission signal, the purpose is to detect and evaluate the severity of fatigue damage of materials and structures, from the initial stage of fatigue damage to the gradually growing macro cracks. By establishing a model framework, the fatigue damage can be accurately described and continuously monitored. To improve the accuracy of the damage quantification numerical results based on the second harmonic generation, Lee et al. proposed an advanced simulation method for fatigue crack trajectories based on guided wave simulation. Compared with the traditional simulation method using a straight crack as the damage model, the nonlinearity of the advanced simulation method in crack length trend and size is closer to the experimental results.
2.3 Factors Affecting Fatigue Strength
The fatigue problem of gears is the weakest link affecting the reliability of the gear transmission system. For different gear materials, the factors affecting fatigue performance damage are different. The fatigue performance of metal gears is affected by factors such as load, surface roughness, and temperature. Load is an important factor that has been widely studied. When the load exceeds the design range during gear use, especially when the sample undergoes periodic overloading of the cyclic yield stress magnitude, the fatigue performance will be significantly reduced. Liu et al. found that when the load is small, the fatigue performance is mainly affected by the stress distribution. As the load increases, the area where the gear may fail expands. For the large stress amplitude caused by load fluctuation, the Brown-Miller-Morrow fatigue criterion is often used to simulate the stress-strain state and predict the fatigue life. Yan established a linear relationship between the gear input system torque and the maximum contact stress of the gear using this fatigue criterion for the wind turbine gear transmission system, and converted the random stress into an equal amplitude cyclic stress as the load input variable. The results showed that under high load, obvious bending and torsional deformations will occur between the gear shafts, leading to gear failure.
Polymer gears have temperature-dependent physical properties. Temperature rise can significantly reduce the tooth surface contact pressure, but it will also affect the gear fatigue performance and thus the fatigue life. Considering the influence of temperature on the fatigue strength performance of gears is crucial. Even under the same load and speed, the temperature will vary greatly due to differences in test equipment, gear size and shape, surrounding environment, and cooling and heating rates. Kalin et al. studied the influence of different temperature conditions on the fatigue wear of polymer gears and found that the fatigue performance of polymer gears is significantly better at low temperatures (30 °C).
In addition to load and temperature, other factors such as roughness also have a great influence on gear contact fatigue. Li Zhi et al. studied the influence of microconvex body parameters on the contact stress of gears. The results showed that within a certain range, as the radius of curvature of the microconvex body increases, the contact stress also increases. The contact stress increases with the increase of height, and the height factor has a greater influence on the stress. Peng et al. believed that corrosion damage (such as the presence of pitting and intergranular cracks) will reduce the fatigue life, and corrosion pits often form multiple small fatigue cracks, which will merge into larger cracks when growing simultaneously.
3. Gear Fatigue Crack Initiation and Propagation
3.1 Three Types of Gear Fatigue Cracks
Gear cracks can be divided into three types under the action of external forces, as shown in Figure 1. The opening and propagating crack [Figure 1(a)] is generated under the action of tensile stress perpendicular to the crack surface. The sliding crack [Figure 1(b)] is generated by the slip under the action of shear stress perpendicular to the crack surface and perpendicular to the crack tip. The tearing crack [Figure 1(c)] is generated by tearing and propagating under the action of shear stress parallel to the crack surface and the crack front.
(a) Opening type
(b) Sliding type
(c) Tearing type
Figure 1 Three basic forms of the crack
Pei Weichi et al. found that in the steady-state crack propagation stage, when the applied load increases, the propagation rates of the opening and sliding cracks both increase. In the acceleration stage, the crack propagation rates increase basically the same with the increase of the applied load. Under a constant load, the crack propagation rate of the sliding crack is higher than that of the opening crack. The sliding fatigue crack generally occurs on the surface or under the surface of the component. The sliding fatigue crack starting from the surface propagates under the action of air or lubricant, and the sliding fatigue crack starting from the inside of the surface is generally caused by inclusions in the middle and propagates in a vacuum.
3.2 Analysis of Gear Fatigue Crack Initiation
3.2.1 Initiation Causes
The mechanism of crack initiation has been studied for a long time, but there is still no specific conclusion and it is still in the speculation stage. Since there is no specific description of the cause and process of crack initiation, specific numerical analysis cannot be carried out. In the gear production process, it is found that the extrusion process may lead to some surface defects, which may have a negative impact on the integrity of the material. Cracks are generated during the extrusion process, and the high hardness and low toughness of the alloy promote the fatigue crack propagation of existing defects. According to the microscopic analysis of the gear fatigue area, it can be clearly seen that the fatigue arcs and radial stripes are distributed in the fatigue source area and the propagation area respectively, and there are tooth surface processing marks near the initial crack. Therefore, it is judged that the cause of the crack is the initial tooth surface processing mark. Under the continuous cyclic load, the crack gradually propagates until it breaks. Huang et al. studied the initiation of gear cracks using a three-dimensional finite element method. The results showed that the maximum stress exists at the gear tooth root, and the initial crack appears at the place with the largest stress value. Mackaldener et al. established a two-dimensional plane strain finite element mesh to evaluate the stress at each point of the gear tooth in each load cycle. Combined with the finite element analysis, the risk of crack generation at different parts of the gear was calculated. The analysis results showed that the tensile stress caused by surface hardening leads to high fatigue stress in a large area inside the gear.
3.2.2 Detection Methods
For fracture mechanics research and safety research, the means and methods for measuring crack initiation, propagation rate, and direction are very important. In a large number of studies, researchers have established different models to detect cracks generated by gear fatigue motion based on the distribution of residual stress, stress-strain curves, etc. Xi mapped the residual stress and hardness distribution at different distances from the gear surface to study the gear fatigue crack initiation area. By combining the distribution of fatigue strength and working stress from the surface to different depths and changing the applied load, the most fatigue-prone area and the position of fatigue crack initiation can be easily determined. Lalonde et al. proposed a factorial design method for gear bending fatigue simulation to quickly predict the crack propagation path. A two-dimensional boundary element model assuming linear elasticity was used for the factorial design experiment, and the bending fatigue damage was modeled using a polynomial function. The established prediction model can quickly establish the crack trajectory of a thin-rimmed gear under any number of cycles. Belsak et al. processed the time vibration signal related to the rotation speed in the time-frequency analysis to improve the reliability of the damage (fault) definition. According to the prediction, when a crack appears, the measured signal will have some characteristic changes, which should increase the number of sidebands in the frequency spectrum.
At present, the analytical model for calculating the meshing stiffness of good gears has been relatively perfect. Compared with the finite element method, the calculation results of the analytical model have a high degree of agreement and the calculation time is shorter. Chen et al. proposed an analytical meshing stiffness calculation model for non-uniformly distributed tooth root cracks along the tooth width, which can well predict the tooth cracks generated in the early stage of the spur gear pair. Through case studies, it can be seen that the dynamic characteristic statistical indicators related to cracks in the gear transmission system are more sensitive to the crack propagation along the tooth depth than the crack propagation along the length. Among the three statistical indicators (peak-to-peak, kurtosis, and crest factor) used in this literature, kurtosis has the least sensitivity to crack propagation. Yang et al. found that the gear crack is closed in the non-service state, but it is open in the working state. An improved calculation model for the meshing stiffness of gears with cracks was proposed, considering the change of the effective compression section of the cracked tooth surface and the neutral layer offset caused by the crack opening. For large cracks, the influence of the bending stiffness change caused by the neutral layer offset on the meshing stiffness cannot be ignored.
3.3 Analysis of the Causes of Gear Fatigue Crack Propagation
3.3.1 Propagation Methods
Fatigue crack propagation prediction is an effective tool for estimating the remaining service life of structural components before failure. After cracks are generated in gears, material defects, pre-cracks, and cyclic loads can easily cause undetected cracks to propagate in any direction and form any shape. There are many numerical simulation methods for gear fatigue fracture, including the finite element method, boundary element method, meshless method, and extended finite element method. In recent years, the simulation of crack propagation has increasingly changed from 2D to 3D. At present, the finite element method and the extended finite element method are mostly used to simulate and predict the crack propagation of gears. Moes et al. found that the extended finite element method can predict the crack propagation rate, failure cycle number, crack shape, and final size of the crack, which are basically consistent with the experimental results, verifying the reliability of this method.
Using the extended finite element method, Nikfam et al. mainly analyzed the influence of the initial crack geometry and cyclic load factors on the tooth fatigue fracture behavior. A two-dimensional finite element model of a pair of teeth was established in Abaqus, and a crack was preset at the tooth root. The simulation model and mesh division are shown in Figure 2. According to the maximum stress criterion, the crack propagation direction was determined. Sukumar et al. found according to the extended finite element simulation model that the initial position of crack initiation has a great influence on the crack propagation direction and propagation rate, and the length of the initial crack affects the crack propagation rate to a certain extent. Verma et al. used the extended finite element method to determine the time-varying meshing stiffness and crack propagation behavior of spur gears. The results showed that the crack propagation path strongly depends on the crack starting point. Majzoobi et al. analyzed the results of cyclic loading conditions using the finite element method and then used the virtual crack growth method in the finite element method to simulate the fatigue crack propagation process from the initial crack to the formation of surface pits. In order to obtain the number of loading cycles required for the initial crack length to expand to the critical length from the crack initiation, the relationship between the stress intensity factor and the crack length was given.
Figure 2 Double tooth models for gear engagement and boundary conditions
The study of the crack propagation path and rate under the action of applied load is an important method in fracture mechanics analysis and is based on the assumption of linear elastic fracture mechanics. Ahamed et al. predicted the crack propagation path at the gear tooth root using a two-dimensional finite element method based on the main elastic fracture mechanics or linear elastic fracture mechanics. When the crack lengths were 10%, 20%, 30%, 40%, and 50%, their corresponding vibration signals were recorded. The experimental results showed that the multiple-pulse individually rescaled-time synchronous averaging (MIR-TSA) as a filtering technology method can improve the rotation speed ratio of vibration signals under different gear input rotation speeds, and the root mean square value of the time-domain signal is an effective diagnostic feature of this method.
3.3.2 Propagation Causes
During the crack propagation process, the inhomogeneity of stress and material structure will affect the crack propagation rate and the deflection of the propagation direction. The deterioration process of the crack is usually related to the change of the material microstructure. The stress intensity factor is closely related to the gear crack propagation and is based on the linear elastic theory, reflecting the strength of the stress field at the crack tip. Therefore, it is necessary to conduct numerical simulation analysis of the stress intensity factor and study its influencing factors.
Guan Lushuang et al. found that when the stress intensity factor K is within the range of the critical stress intensity factor , the crack maintains a stable propagation rate. Figure 3 shows the change curve of the stress intensity factor K with the crack length a. It can be seen from Figure 3 that before the crack propagates to 2.5 mm, the increasing trend of the stress intensity factor is stable. When the crack length exceeds 2.5 mm, the stress intensity factor K exceeds the critical value of the material and increases sharply, and the crack propagates rapidly, resulting in tooth fracture. Thirumurugan et al. believed that in the actual gear operation, the magnitude and position of the force will change with the rotation of the gear. The critical plane damage and finite element theory model were used to study the influence of the moving gear load on the gear service life, and the number of stress cycles required for fatigue crack initiation was determined. Li et al. gave the numerical solution of an infinite elastic plane containing macro cracks and arbitrarily oriented micro cracks, obtained the stress intensity factor, stress field, and strain energy density near the crack tip, and analyzed the influence of micro cracks on the macro crack strength factor. The results showed that as the length of the micro crack decreases or the distance between the micro crack and the macro crack increases, the influence of the micro crack on the macro crack strength factor gradually weakens. The micro crack will increase the strength factor of the macro crack in one direction and decrease it in the other direction.
3.4 Research on Life Estimation under Gear Fatigue Test
According to GB/T 14229 – 2021 “Gear Contact Fatigue Strength Test Method”, for gears that have been carburized and hardened, when the pitting area on a single tooth surface reaches 4% of the contact area of the tooth surface, or the pitting area of the entire gear pair reaches 0.5% of the working area, the tooth surface is judged to be failed, and the number of stress cycles at this time is the failure life [84 – 86].
In the literature [87], the problem of lack of test sample parameters was solved by the probability prediction method of gear crack propagation, and the calculation accuracy was relatively high. Zhou Zijie et al. provided a theoretical basis for the reliability and failure rate of gears based on the characteristics of the Weibull distribution theory and the least square method. During the fatigue test, whether the gear is fatigued and failed is judged by the pitting area of a single tooth of the gear or the pitting area of the gear pair. The test results showed that the tooth surface pitting phenomenon of tooth surface fatigue occurs in the early failure period, and the failure rate of tooth surface pitting is large. Podrug et al. believed that the crack initiation period accounts for most of the service life and studied the influence of dynamic tooth load on the gear fatigue life. The critical plane method can be used not only to predict the gear fatigue life but also to predict the crack initiation direction. The literature [90] proposed a method for generating crack propagation trajectories based on the three – dimensional boundary element method. The Franc 3D method was used to obtain the influence of gear parameter changes on the crack propagation path of the tooth root of spur gears, and the maximum tangential stress crack propagation criterion was used to obtain the crack propagation path, and then the remaining life of the gear fatigue crack was estimated. The results showed that the larger the pressure angle, the smaller the fatigue life; a lower starting angle is beneficial to improving the fatigue life.
4. Methods to Avoid Gear Fatigue Cracks
There are many methods to avoid gear cracks from the root. One of the focuses in some studies is to reduce the bending stress level to improve the gear strength. In addition to the cyclic fatigue load during work, a large part of the reasons for gear crack initiation are the defects in the processing technology during gear manufacturing, which cause the concentration of residual stress on the tooth surface. Therefore, during the gear processing, the surface roughness of the gear should be reduced, the hardness of the gear tooth root should be enhanced, and the influence of the residual stress during processing on the strength of the gear tooth root should be weakened as much as possible [91]. In addition, it can also start from the selection of materials and the design of gears. Innovative gear materials can be used to design new ecological gears. Traditional materials such as engineering plastics can be replaced with lower – cost materials [92], and the optimal rim thickness can be selected to increase the tooth root stress of the gear.
The standard method to extend the gear life is to harden the contact surface by carburizing or coating [93]. Chromium coating is a method to extend the service life of steel gears. These coatings are extremely hard and chemically inert. The friction coefficient is reduced, that is, the lubrication effect of the gear is better, so the service life is also increased.
When the gear is fatigued and damaged, using appropriate technology to repair the gear can effectively prevent the occurrence of faults and catastrophic accidents and extend the fatigue life of the cracked gear. The purpose of maintenance is to keep the technical system (gear unit) in the most suitable working state [94]. However, the purpose of modern maintenance is not only to eliminate faults but also to define the potential danger stage of sudden system failures. The carbon fiber – reinforced polymer [95] reinforcement system can significantly improve the fatigue life of steel components. In addition, recent studies have shown that the use of prestressed unbonded carbon fiber – reinforced polymer reinforcement systems can further reduce the fatigue crack propagation rate and promote crack arrest.
In the future technology for detecting gear fatigue failures, efforts can be made in signal detection. The variable amplitude modulation effect can be studied to find the corresponding modulation scale, making the filtering process more stable and easier to detect and analyze the problems existing in gear work. At the same time, some new methods can be better combined with the monitoring of crack initiation and propagation. For example, the DC voltage fluctuation method [96] can monitor the entire process of crack propagation and measure the crack propagation rate in real time. This method is based on the monitoring principle of voltage change caused by resistance change.
5. Conclusion
With the rapid development of the manufacturing industry in recent years, the performance requirements for gears in all aspects are getting higher and higher. Gears will be fatigued and cracks will be initiated under the continuous cyclic load of internal and external forces, eventually leading to fracture. There are three types of cracks: opening type, sliding type, and tearing type. The causes of different crack types, as well as the propagation rates and directions, vary greatly under different working conditions. Cracks are the most common faults of gears, and a lot of research and experiments have been done on crack initiation. The causes of crack initiation depend on static, dynamic or thermal loads, material selection and processing, and the type of external working conditions. Under the continuous action of internal and external forces, gear cracks propagate. There are many methods to study gear crack propagation, among which numerical simulation methods include the finite element method, boundary element method, and extended finite element method. In recent years, more and more extended finite element methods have been used. The methods of crack propagation involve many factors. The above methods are mainly used to analyze the influence of factors such as the initial shape, length, and cyclic load of cracks on the crack propagation behavior. The research on the life estimation of gears under fatigue tests provides a theoretical basis for predicting the probability of gear failures to a large extent and increases the reliability. Some of the test methods and theoretical results are effective means to predict gear crack initiation and life.
To avoid crack generation is the main measure to ensure the efficient and safe operation of gears. Fundamentally, the microstructure and mechanical properties of gear materials are particularly important. Through gear damage detection algorithms, such as the average contrast number algorithm [97], the evolution of the microstructure during the gear contact fatigue process and the relationship between fatigue damage and mesomechanical behavior can be deeply explored. When the gear is fatigued and damaged, the crack can be monitored by signal detection technology, the crack propagation rate and direction can be measured in real time, and the gear crack can be repaired by technology to extend the service life of the gear. Although there are still many problems to be overcome in the anti – fatigue manufacturing technology of gears, under the background of the country’s vigorous implementation of the innovation – driven development strategy, in order to obtain advanced and ideal comprehensive gear performance, modern heat treatment processes, surface strengthening technologies and other disciplines must be combined with specific materials, processes and equipment. The future advanced manufacturing technology will continue to progress and achieve a qualitative leap.
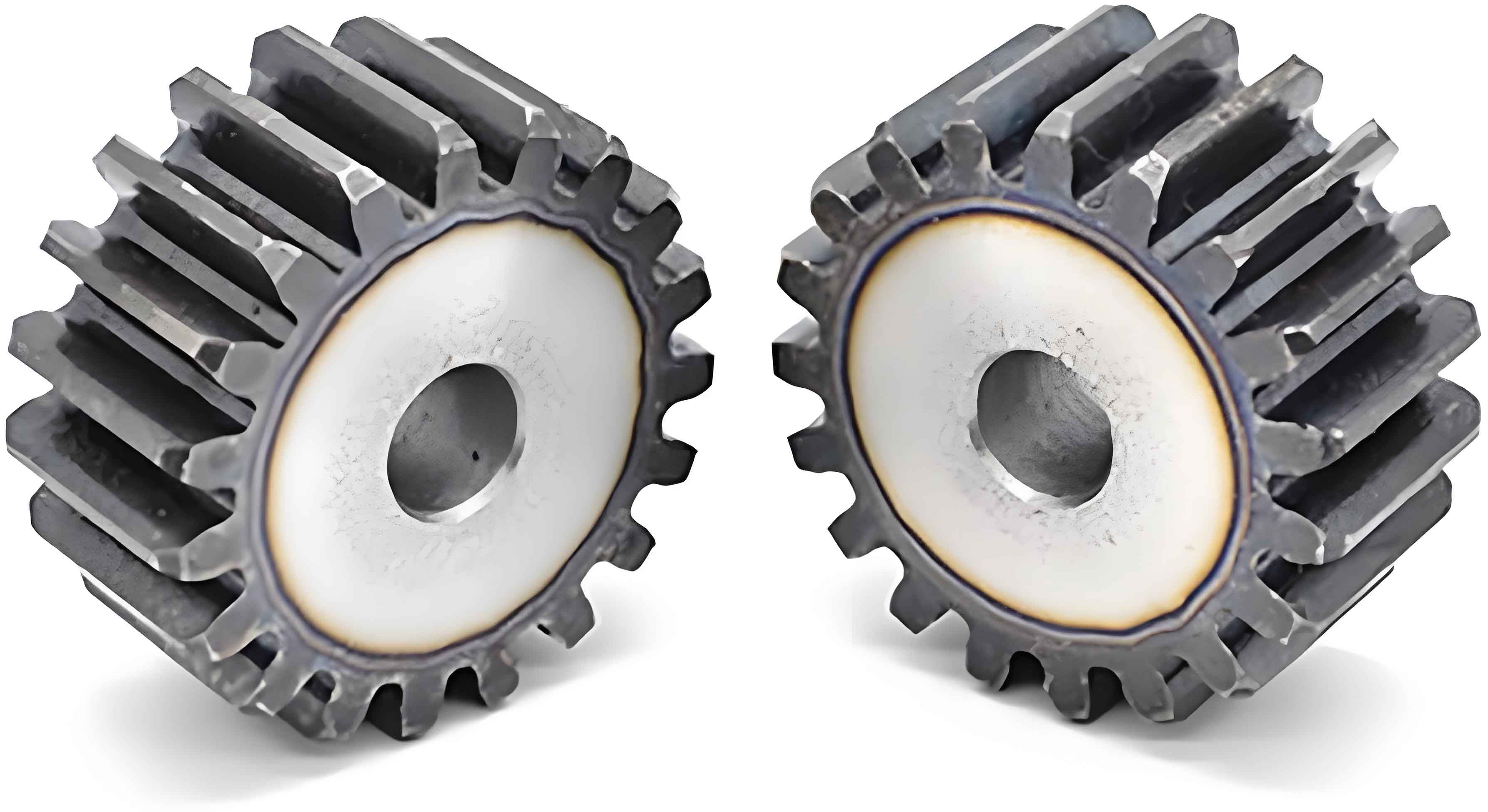