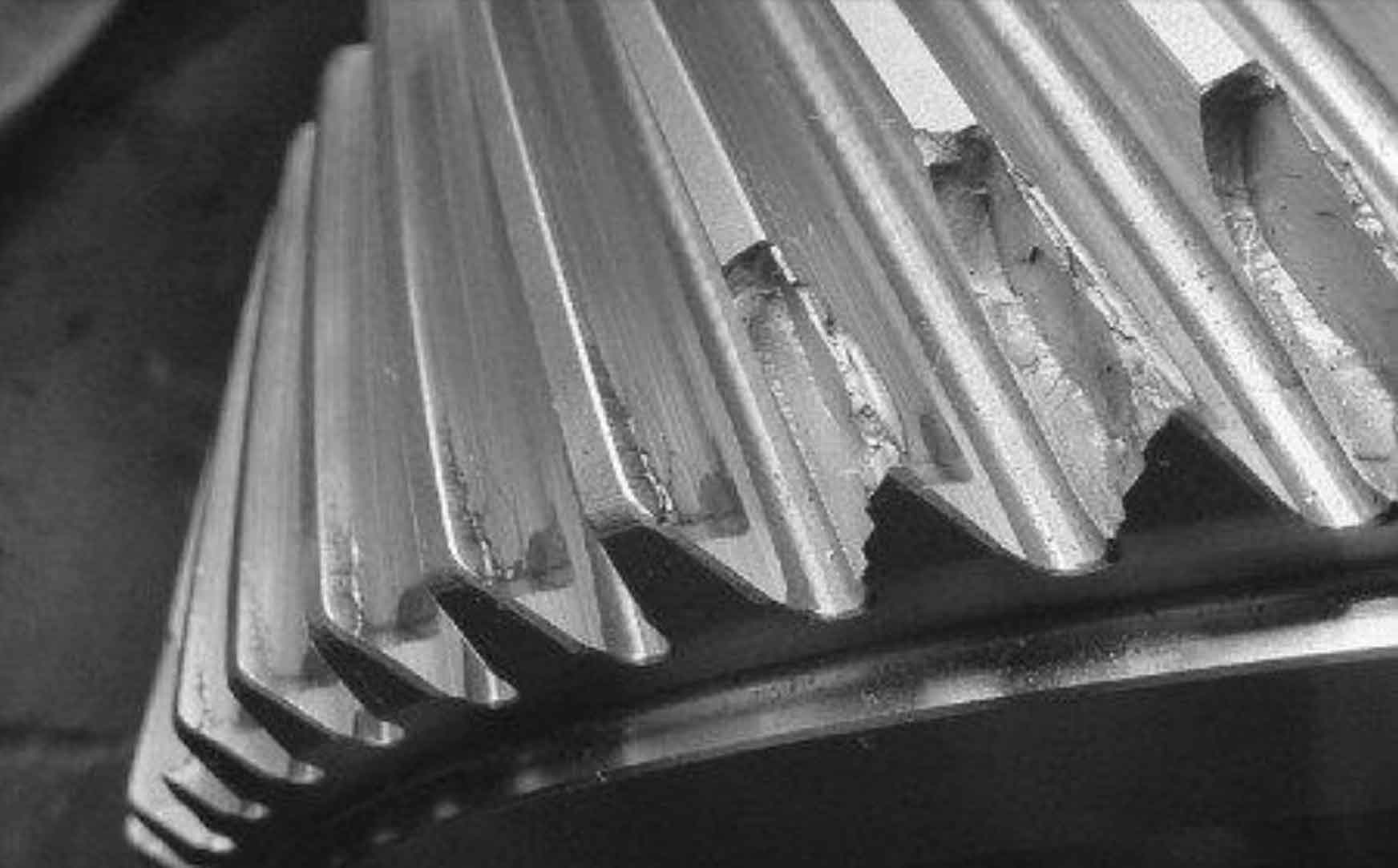
Wang Shuo and other scholars established a three-dimensional model of a helical gears, and conducted static analysis of the helical gears under working conditions using ANSYS finite element analysis software. They simulated and calculated the static bending stress distribution of the helical gears, verifying whether it meets the gear strength requirements. The static analysis results were imported into the fatigue life analysis software FE-SAFE for fatigue life analysis, and then the calculation results were imported back to ANSYS to obtain the fatigue life cloud map, Verify that the service life of the helical gears meets the design requirements.
Scholars such as Lin Xiaoyan have established a residual strength prediction model with parameters determined by S-N curves, based on the characteristics of residual strength attenuation and nonlinear fatigue damage accumulation theory, which can avoid conducting a large number of experiments. The comparison between the predicted results of the model and the material experiment results proves the accuracy of the prediction model. Combined with the dynamic reliability function, the Rackwitz Fiessler method and perturbation method are applied to calculate the bending and contact fatigue reliability of helical gears transmission.
Scholars such as Li Ming focused on high-precision long-life helical gears with high manufacturing costs and long manufacturing cycles. In order to obtain the life information of helical gears simply and accurately, they obtained the probability life relationship between helical gears with different tooth numbers based on the concept of minimum order statistics. The proposed probability prediction life model can take the life data of specific helical gears as input to obtain the probability prediction life of other helical gears. The probability prediction life model was validated through the bending fatigue test of helical gears at a constant stress level, and the test results proved that the model has good predictive ability.
Peng Chong et al. [10] studied the effect of Laser Shock Peening (LSP) on the bending fatigue performance of AISI9310 steel spur gears. The residual stress distribution caused by LSP was simulated using finite element method, and the results were verified through X-ray diffraction analysis. Research has found that LSP can generate an ideal depth of compressive stress layer on the root fillet of helical gears, and the magnitude and depth of compressive stress increase with the increase of laser energy. Conduct bending fatigue tests to compare the fatigue performance of laser peened teeth and non peened teeth. The results showed that compared with the unpeened teeth, the bending fatigue life and bending fatigue limit of LSP teeth were significantly improved.
Li Xiuhong and other scholars used UG three-dimensional software to establish a model of the helical gear pair in the high-speed train gearbox, and calculated the bending stress distribution of the helical gear pair during meshing using ABAQUS software to analyze the root crack initiation position of the helical gear pair. By combining fatigue damage accumulation theory, nominal stress method, and local stress-strain method, the crack initiation life can be simulated and calculated. High frequency fatigue testing was conducted on the experimental spur gear to obtain the crack initiation life. By comparing the calculated results with the experimental results, it was determined that the model based on the local stress-strain method is more accurate. The static results of the helical gear pair were imported into FE-SAFE, and the crack initiation life of the helical gear tooth root was calculated.
Lin Yulong and other scholars studied the input spur gear pair of the 4LZ-2 combine harvester and established a three-dimensional finite element model of the input spur gear pair to predict the fatigue life of the small gear when crack initiation and propagation are caused by bending stress. Considering the coupling effect of different stress amplitudes and excitation frequencies on fatigue life, a fatigue life prediction method based on the concept of power density and Miner formula is proposed using numerical data obtained from three-dimensional finite element analysis. The feasibility of quantifying the fatigue performance of helical gears pairs based on the concept of power density has been demonstrated through experimental verification.
Zhang Boyu and other scholars studied the rolling fatigue relief of wind turbine gears, and proposed an elastic-plastic finite element contact fatigue model using the root mean square of surface roughness directly measured by an optical profilometer as the main parameter. Extract the contact pressure, residual displacement, stress and strain fields during cyclic contact loading, and apply the Brown Miller multiaxial fatigue criterion to consider the combined effects of stress and strain to predict the contact fatigue life of rough surfaces.
Xing Zhiguo and other scholars have designed a new method for prefabricating different stress concentrations near any inclusions on the surface of gear steel by combining microhardness testers and laser etching equipment, using 20Cr2Ni4 steel as the research object. A new type of bending fatigue test was conducted on 20Cr2Ni4 steel to study the stress distribution near inclusions. A quantitative analysis mathematical model is provided based on the parameters of prefabricated notches and the state of inclusions, which can accurately predict the fatigue limit of the heavy-duty helical gears steel. The research results demonstrate that the model can be used for practical analysis of heavy-duty helical gears and life prediction based on the stress state of helical gears, providing a life prediction model for the production and processing of 20Cr2Ni4 steel gears.
He Haifeng and other scholars established a damage coupled elastic-plastic numerical model considering the influence of initial residual stress on the gear pair of a 2MW wind turbine gearbox, in order to study the fatigue performance of helical gears. Based on continuous damage mechanics, the surface contact fatigue life and root bending fatigue life are predicted by calculating the stress field, contact area, and damage rate of the tooth root area. The results indicate that the risk of contact fatigue failure on the surface of helical gears is much higher than that of tooth root bending fatigue failure. Subsequently, based on the theory of continuous damage, a novel gear bending fatigue model combining hardness gradient characteristics and residual stress was proposed to evaluate the bending fatigue behavior of hard shell wind turbine helical gears. The damage equation and damage coupled constitutive equation including residual stress and hardness gradient were derived. The model was experimentally validated for bending stress, bending fatigue failure location, mechanical performance degradation, and bending fatigue life. The predicted bending fatigue life of different hard shell helical gears is within the range of 1.5 times the predicted life.
Zhou Jie and other scholars proposed a nonlinear cumulative damage model based on material memory degradation, taking into account loading history. Four materials were used for fatigue testing and their fatigue life was predicted, and the results were compared with the Miner criterion, Lv model, and Kwofee model to verify the accuracy and effectiveness of the proposed model in estimating remaining life.
Lin Chao and other scholars have established a new theoretical model for calculating the bending fatigue life of a novel curved gear pair with time-varying characteristics. A single tooth model of a curved gear pair was established to simulate the actual operating load state, analyze the effective load of the gear pair, and obtain the load spectrum of a single tooth within a single cycle. By constructing an equivalent cantilever beam model for gear teeth, a single tooth bending stress calculation formula is derived, and bending stress spectrum analysis is performed on different sections of the tooth to obtain the stress spectrum of the dangerous section for single cycle tooth bending fatigue. A theoretical calculation method for the bending fatigue life of curved gears is proposed by combining the Miner criterion and the stress spectrum of the dangerous section of single cycle tooth bending fatigue. By comparing theoretical calculations, simulations, and experimental results, the error between the experiment and theory is within 10%, which verifies the accuracy of the theoretical calculation method for the bending fatigue life of curved gears.
Wang Zhiyuan and other scholars used ultrasonic surface rolling technology to strengthen 20Cr2Ni4A carburized helical gears steel and studied its effect on the bending fatigue performance of heavy-duty helical gears steel. A predicted failure probability stress cycle number (PS-N) curve was drawn and fatigue fracture was analyzed. Through experiments, it has been verified that USRP treatment significantly improves surface roughness, increases surface hardness, introduces a large amount of residual compressive stress, and further enhances the fatigue performance of carburized helical gears steel. In order to accurately characterize the impact of inclusions on fatigue performance, a new life prediction model based on Nisha S model was proposed by adding the effects of inclusion quantity, area, and type as corrections. The model has been validated through experiments, and the results have high accuracy.
Wang Wei and other scholars have comprehensively considered the failure mechanisms of contact fatigue and bending fatigue, and proposed a unified microstructure model. Using a damage coupled crystal plasticity model to capture the stress-strain history of slip system activity. Implement multiaxial fatigue standards at the grain level to consider stress-strain history. The mechanical properties of material points at tooth pitch and tooth root were evaluated using the continuous damage theory.
Ding Han and other scholars developed an improved design of tooth surface dry grinding tools for bending fatigue life by combining high life cycle assessment and low life cycle cost. A multi axis fatigue damage model was used for root bending fatigue assessment based on finite element method. A dry grinding tool correction model considering geometric accuracy for bending fatigue life was established with the goal of minimizing the fatigue limit of hazardous points. A relationship was established between the initial tool parameters and the actual transmission fatigue life in the design stage, and the effectiveness of the proposed method was verified through numerical examples. Afterwards, a data-driven method for predicting and optimizing the root bending fatigue life of spiral bevel gears based on Top Rem tool parameters was proposed. Using finite element method based simulation loading gear contact analysis to determine root bending stress, and combining with a model based on multi axis fatigue damage assessment, data-driven fatigue life prediction is carried out. Verified that in the early stages of the development of spiral bevel gear full life products, modifying the key parameters of the Top Rem tool can significantly improve its bending fatigue life. A new gear root side bending fatigue life prediction model was established by considering the carburization effect on the root side of spiral bevel gears and combining it with multi axis fatigue criteria. Taking aerospace spiral bevel gears as an example, the influence of key machine tool settings on tooth root bending fatigue life was verified.
Zhu Xiaolu studied the influence of the internal quality of carburized and quenched gears on the strength and service life of helical gears. Based on the experimental data of carburized and quenched gears made of 5 different materials, the bending fatigue limit and reliable stress life curves of the tested helical gears were plotted, and the relationship between surface decarburization of the helical gears and their bending fatigue strength was obtained.
Tang Xin and other scholars studied the bending fatigue performance of third-generation aviation gear steel cylindrical gears, designed the parameters of cylindrical gears for bending fatigue testing, and conducted bending fatigue tests on the gears of this material. The experimental data was processed using two parameter Weibull distribution and logarithmic normal distribution data processing methods, and the bending fatigue limit and reliable stress life curve of the test gear for this material were obtained, proving that this material has significant advantages in the bending fatigue characteristics of aviation gear transmission gears.
Chen Xingbin and other scholars used Ansys Workbench to establish a CAE model for 40CR material gear pairs, and conducted contact dynamics and fatigue life prediction analysis for helical gears. Perform static and transient analysis on helical gears pairs using the main factors affecting fatigue performance as parameters. Given different load spectra, based on Miner’s linear damage accumulation theory and material S-N curve, the fatigue analysis software Code Design Life is used to analyze the fatigue life of the helical gears pair, and the fatigue life of the contact area of the helical gears is obtained.
Scholars such as Gao Xiang proposed the concept of damage scaling factor. Based on the results of bending fatigue tests under two-stage loading, the damage scaling factor was fitted using the relationship between the ratio of two-stage stress amplitudes and bending fatigue damage. Use it to improve the original damage prediction model based on cumulative damage theory with toughness as a variable under multi-level loads. The accuracy of the model was verified by comparing the results of bending fatigue tests with multiple loading sequences.
Scholars such as Lan Shuangling have proposed a new ultrasonic rolling strengthening method with the goal of improving the bending fatigue life of cylindrical gears. A single tooth bending fatigue test was conducted to investigate the variation patterns of residual stress, surface hardness, and root hardening depth. The relationship between residual surface stress, surface hardness, depth of hardened layer, and bending fatigue life was ultimately determined. The anti fatigue mechanism of ultrasonic rolling strengthened gears is to convert the residual tensile stress at the tooth root into residual compressive stress.
Zhang Xiaolu and other scholars studied 18CrNiMo7-6 gear steel, and based on the traditional vacuum degassing smelting method, a comparative experimental steel was obtained by combining electroslag remelting and Nb microalloying. The fatigue performance of two test steels was characterized through rotational bending fatigue testing. And by means of microstructure analysis, fatigue fracture characterization, inclusion analysis, and hardness distribution, the influencing factors on the fatigue performance of two types of experimental helical gears steels were explored.
Scholars such as Fu Zhiyuan have comprehensively considered the influence of modification coefficient, number of teeth, and modulus on the strength of helical gears. They have established a mathematical model with the geometric parameters of helical gears as design variables, and the requirements of strength, overlap, and tooth top thickness of helical gears pairs as constraint conditions. The optimization objective is to minimize the difference in maximum bending stress at the root of helical gear pairs. The corresponding MATLAB program is written using multi-objective particle swarm optimization (MOPSO) algorithm, Optimize and solve the established mathematical model. Through finite element verification using MASTA software, the difference in bending strength between large and small helical gears before and after optimization was reduced, and the tooth surface bearing capacity was improved.