Customizing spiral bevel gear for specialized industrial applications involves several critical considerations to ensure that spiral bevel gear meet specific performance requirements, environmental conditions, and operational demands. Spiral bevel gears are vital components in transmitting power efficiently across intersecting shafts, and their customization can significantly enhance the functionality and durability of machinery in various industries, including aerospace, automotive, heavy machinery, and energy. Below are key aspects involved in customizing spiral bevel gears:
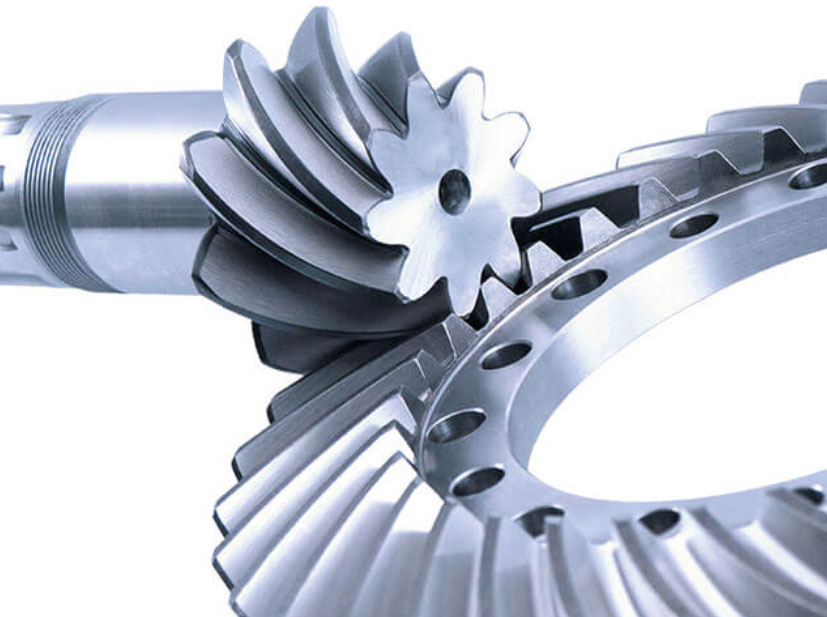
1. Material Selection
- High-Strength Alloys: Materials such as high-strength steel alloys are commonly used for their durability and resistance to wear. The specific alloy chosen can depend on the application’s requirements for strength, temperature resistance, and corrosion resistance.
- Advanced Materials: For applications requiring lightweight or non-metallic options, materials like carbon fiber-reinforced composites or advanced polymers can be used. In extremely demanding environments, ceramics or special alloys designed for high temperature or corrosive conditions may be selected.
2. Gear Geometry and Design
- Custom Tooth Profiles: The shape and size of spiral bevel gear teeth can be tailored to optimize load distribution, minimize stress concentrations, and reduce noise. This customization can significantly affect spiral bevel gear’s efficiency and lifespan.
- Mounting Features: Customized spiral bevel gear may require specific mounting features to fit unique assembly requirements or to interface with other components in the system.
- Size and Ratio: Depending on the power transmission needs, spiral bevel gear size and the ratio of spiral bevel gear pair can be designed to achieve the desired torque and speed output.
3. Manufacturing Techniques
- Precision Machining: Advanced CNC machining techniques allow for high-precision manufacturing of spiral bevel gear, ensuring that they meet the exact specifications for specialized applications.
- Additive Manufacturing: 3D printing technologies enable the production of spiral bevel gear with complex geometries or internal features that would be difficult or impossible to achieve with traditional machining methods. This is particularly useful for lightweight or highly customized spiral bevel gear designs.
4. Surface Treatments and Coatings
- Heat Treatment: Processes like carburizing, nitriding, or induction hardening can increase surface hardness and fatigue resistance, enhancing spiral bevel gear’s durability.
- Coatings: Surface coatings such as diamond-like carbon (DLC) or titanium nitride (TiN) can provide additional wear resistance and reduce friction, further improving performance in harsh environments.
5. Lubrication and Sealing
- Lubrication Systems: Custom spiral bevel gear may require specific lubrication strategies to ensure smooth operation and to protect against wear, especially in high-speed or high-load applications.
- Sealing Solutions: For spiral bevel gear operating in environments exposed to dust, moisture, or corrosive substances, custom sealing solutions can protect spiral bevel gear mechanism and ensure longevity.
6. Testing and Validation
- Performance Testing: Rigorous testing under simulated operational conditions is crucial to validate the design and manufacturing quality of custom spiral bevel gear. This includes load testing, thermal analysis, and vibration analysis.
- Life Cycle Analysis: Estimating the operational lifespan under expected conditions helps in making informed decisions about materials and design features.
Conclusion
Customizing spiral bevel gear for specialized industrial applications requires a holistic approach, considering material properties, design specifics, manufacturing precision, surface treatments, and operational conditions. Through collaboration between design engineers, material scientists, and manufacturing specialists, it is possible to develop spiral bevel gear that meet the unique demands of specialized applications, thereby enhancing the performance and reliability of industrial machinery and systems.