Spur gears, fundamental components in countless mechanical systems, rely heavily on the properties of the materials from which they are made. The choice of material affects spur gears strength, durability, resistance to wear, and cost-effectiveness. This comprehensive guide explores various materials used in the manufacture of spur gears and their applications, highlighting how different materials cater to the specific demands of various industries.
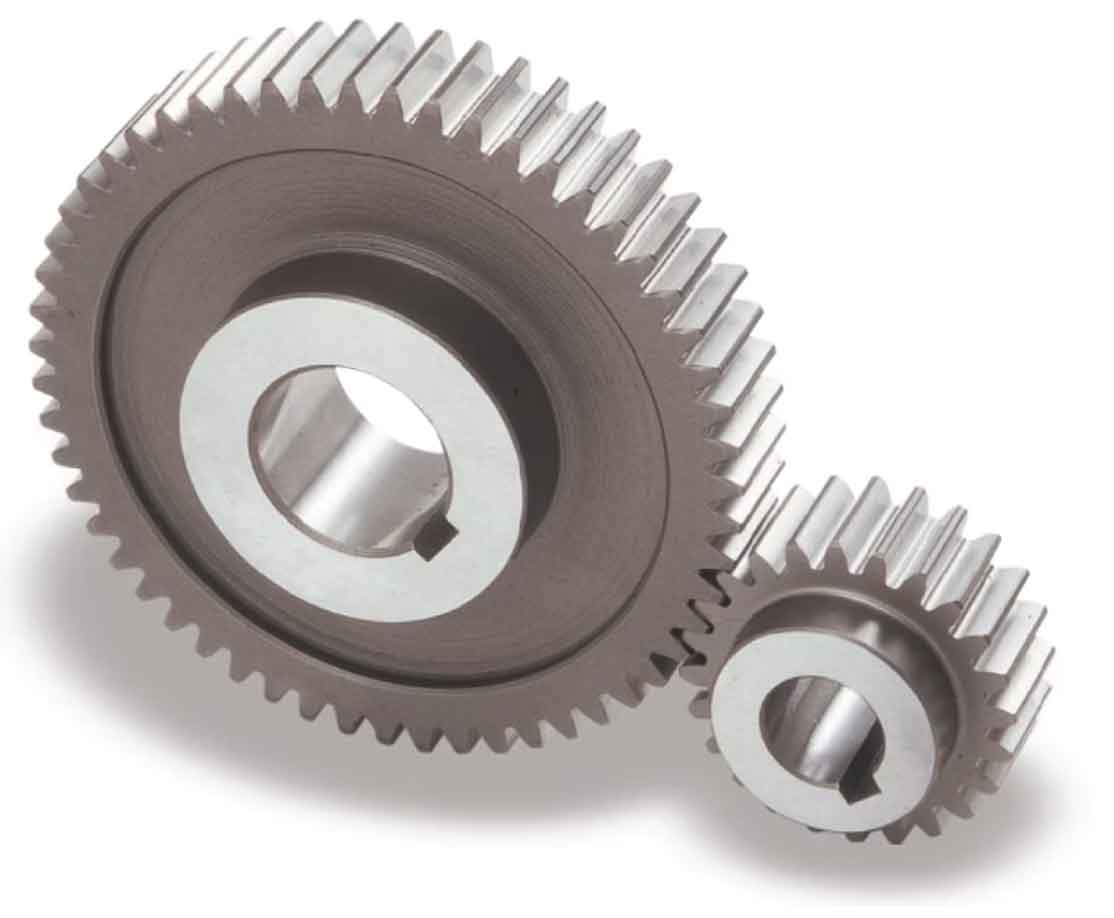
1. Steel and Steel Alloys
Characteristics: High strength, excellent toughness, and good wear resistance. Steel spur gears can handle high loads and are suitable for applications requiring durability and resistance to impact. Alloy steels, with elements like chromium, molybdenum, and nickel, offer enhanced properties like increased hardness and corrosion resistance.
Applications: Widely used in automotive transmissions, heavy machinery, and industrial equipment where high strength and durability are essential.
2. Cast Iron
Characteristics: Good wear resistance, high compressive strength, and the ability to absorb vibrations make cast iron suitable for spur gears. Gray cast iron and ductile cast iron are common, with ductile iron providing additional toughness and resistance to shock loads.
Applications: Suitable for machinery where noise dampening is beneficial, such as in gearboxes for industrial machinery and automotive components.
3. Brass and Bronze
Characteristics: Excellent machinability, good corrosion resistance, and inherent lubricity. Brass spur gears are more malleable and less strong compared to steel and iron spur gears, while bronze spur gears offer superior wear resistance and strength, especially in marine environments.
Applications: Commonly used in clocks, electronic devices, and marine applications where corrosion resistance is crucial. Bronze spur gears are preferred for their durability in harsh conditions.
4. Aluminum and Aluminum Alloys
Characteristics: Lightweight, corrosion-resistant, and with good machinability. Aluminum spur gears are not as strong as steel spur gears but offer a high strength-to-weight ratio, making them suitable for applications where weight reduction is critical.
Applications: Ideal for aerospace, automotive, and robotics applications where reducing the weight of spur gear assembly enhances performance and efficiency.
5. Plastics and Composite Materials
Characteristics: Include a wide range of properties depending on the type of plastic or composite. They can offer excellent corrosion resistance, low noise operation, and reduced weight. Common plastics used include acetal, nylon, and polycarbonate. Composite spur gears can be reinforced with fibers to enhance strength and thermal stability.
Applications: Used in consumer electronics, light machinery, and medical devices where low weight, low noise, and low to moderate load capacity are required. Composite spur gears find applications in specialized environments, such as in high-temperature or chemically aggressive conditions.
6. Ceramics
Characteristics: Extremely hard and wear-resistant, ceramics can withstand high temperatures and aggressive environments. They are brittle, however, and can fracture under impact or shock loading.
Applications: Suitable for high-precision machinery, aerospace components, and applications requiring resistance to high temperatures and corrosive substances. Ceramic spur gears are often used in specialized equipment where their unique properties offer significant advantages over metals or plastics.
Conclusion
The selection of material for spur gears is crucial and depends on a variety of factors including the operational environment, required load capacity, speed, noise considerations, and cost. Advances in material science continue to expand the possibilities for spur gear design, allowing engineers to tailor spur gear materials to meet the specific needs of increasingly complex and demanding applications. Whether for high-strength industrial machinery, lightweight aerospace components, or precision medical devices, there is a material and design that fits the need. Understanding the properties and applications of these materials is key to optimizing spur gear performance and longevity in any mechanical system.