Dr. Stadtfeld of Greenson first outlined the idea of using disc wheel to machine face gear. It has the advantages of simple structure of grinding wheel, convenient design, manufacture and dressing, not limited by the design parameters of surface gear, and easy to realize the movement of machine tool. Due to the relative maturity of the surface gear machined by foreign worm tools, there are few reports on the research of the surface gear machined by disc cutters in foreign countries. However, due to its easy realization, it has been greatly developed in China.
The principle of using disc wheel to process face gear is shown in the figure, in which the profile of the tool is formed by rotating the normal section of the profile wheel around the axis of the tool. The cutter and workpiece move in a straight line along the guide rail 2 and 3 respectively to complete the feed movement in the direction of tooth width and tooth depth. The cutter rotates around its axis 6 to achieve the cutting movement. In addition, the compound movement of linear movement 1 and 3 rotation movement 5 can make the cutter rotate around the axis of the generating wheel. The rotation and workpiece rotation simulate the meshing of the generating wheel and the workpiece, so as to complete the generating processing of the face gear.
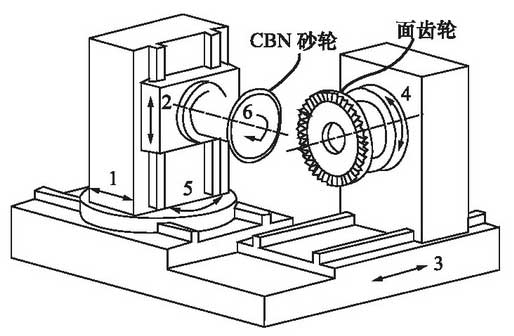
The workpiece is in point contact with the disc cutter, and it belongs to single tooth indexing machining and needs tooth feed movement, so its machining efficiency is very low. However, because of its convenience, the outstanding significance is that the cutting and grinding of face gear can be realized in a short time. If it is used for grinding teeth, it is also necessary to trim the tool. However, if the cutter is covered by hard cubic boron nitride, the trimming of the cutter can be reduced, and even the gear with dry grinding surface can be achieved at this time, which is also in line with the goal of sustainable development of gear manufacturing technology.
Based on this manufacturing technology, great progress has been made in China. For example, Li Daqing has realized the two-way shape of the face gear by using the disc wheel, and improved its meshing characteristics. Guo Hui et al. Studied the numerical control interpolation method based on the dished cutter, the experiment proved that the interpolation algorithm is effective, and put forward the prediction model of envelope residual. Wang Yanzhong et al. Studied the 5-axis numerical control method of milling face gear with dished cutter. The experiment confirmed that the maximum manufacturing error was 22.6 μ m, and developed the precise grinding method and the dressing method of dished wheel. Through error compensation, the tooth surface deviation was further reduced. Tang Jinyuan et al. Studied the grinding tooth and its shape of face gear based on disc wheel, and simulated it with simulation software. Recently, Fang Zongde and others have carried out the research on the grinding and profile of the offset gear with disc wheel.