In view of the distortion caused by various factors, such as the release of processing stress, the different time and heterogeneity of structure transformation, and the temperature difference in various parts of the gear, some corresponding macro technological measures can be adopted to reduce the distortion or control the fluctuation range of distortion.
Gear blank isothermal normalizing
The dispersion of structure and hardness of gear blank after normal normalizing is large. Isothermal normalizing can first improve the uniformity of structure and hardness, and at the same time reduce the distortion caused by the uneven processing stress.
In recent years, the application of isothermal normalizing of gear blanks has played a good role in controlling the distortion of gear heat treatment in China. The test data of table shows that the hardness and structure uniformity of gear blank after isothermal normalizing are greatly improved. The table shows the effect of Isothermal Normalizing on reducing distortion. Obviously, the effect of isothermal normalizing of gear blank is heating process, not cooling process after carburizing. Therefore, some foreign large-scale automobile companies put forward strict technical requirements for preliminary heat treatment of carburized gear blanks.
Preheating, step heating
On the one hand, the purpose of preheating and step heating is to make the temperature of the surface, inside and all parts of the workpiece more uniform, while reducing the temperature difference with the target temperature. Figure 7 shows the temperature difference distribution in the workpiece surface when the step temperature rises. Compared with the direct high temperature charging, the temperature difference between the surface and the parts of the workpiece is greatly reduced. In fact, in order to reduce the distortion, preheating and step heating reduce the temperature difference of each part of the workpiece.
Based on the effect of preheating, the American military standard mil-h-6657g-1983 “heat treatment process of steel” stipulates that the final machined parts shall be preheated at 1000 ° f (540 ° C) or 1200 ° f (650 ° C) before being heated to 1300 ° f (740 ° C).
Stress relief annealing
In production, stress relief annealing is generally used to reduce the internal stress of the workpiece, which is well known. However, from the previous recrystallization annealing test, it is shown that although stress relief annealing can reduce the residual stress, the distortion caused by processing stress recovery does not mean that it can also be removed. Then, what is the significance of stress relief annealing in reducing distortion? The following two cases are analyzed.
1) Low temperature heat treatment, such as nitriding, after stress relief annealing
A kind of easy distortion boring bar with the size of φ 75 mm × 1930 mm, in which one group of boring bars is subject to stress relief annealing and then nitriding after machining; the other group of boring bars is subject to finish machining after the first stress relief annealing and then nitriding after the second stress relief annealing. The nitriding process of two groups of boring bars is the same. Finally, the teratological variables within 500 mm were measured.
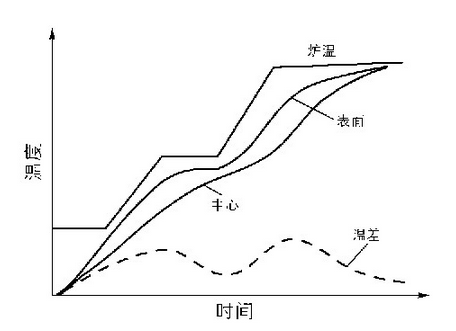
It can be seen from the test data that the distortion is not reduced by stress relief annealing, but exposed by rough machining. After that, the distortion variable is removed by finishing, and then the second stress relief annealing is carried out. Because the cutting amount of finishing is small, the machining stress is correspondingly reduced, and finally the distortion variable of nitriding is smaller. This is essentially a method of decreasing distortion step by step.
2) High temperature heat treatment, such as carburizing, after stress relief annealing
The essence of stress relief annealing is to divide the workpiece heated directly at high temperature into two sections. The first section is heated far below the carburizing temperature. Due to the low heating temperature, the thermal stress is small. At the same time, the heating speed is low and the temperature gradient is small, which is not only conducive to reducing the thermal stress, but also conducive to the slow process of stress release and distorted lattice recovery. Therefore, based on the essence of stress relief annealing, it is better to put the workpiece into the high temperature carburizing furnace immediately after stress relief annealing to get the best effect. In view of this, the existing tempering furnace can be used in the production.