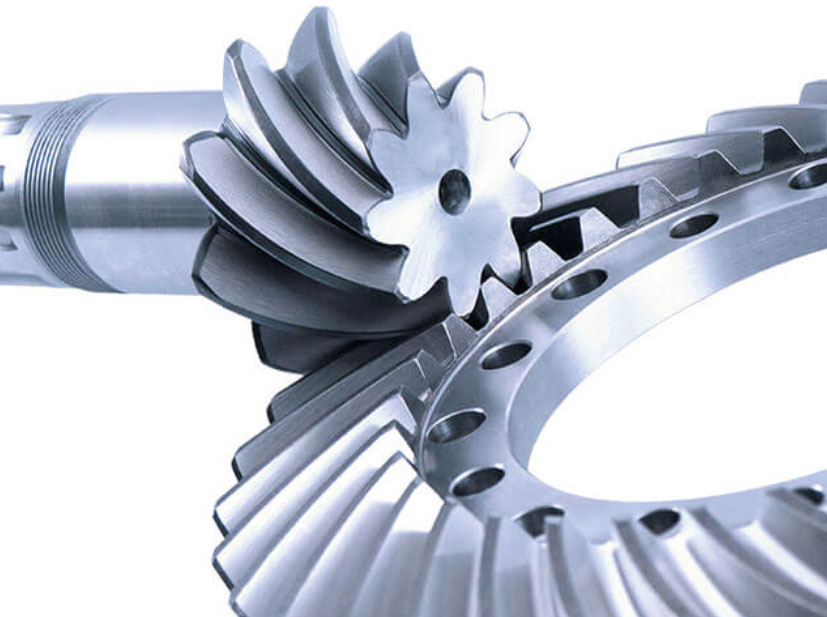
Spiral bevel gear manufacturing has seen several innovations in recent years, driven by advancements in engineering, technology, and manufacturing processes. These innovations aim to improve the precision, efficiency, and cost-effectiveness of producing high-quality spiral bevel gears. Here are some cutting-edge engineering innovations in spiral bevel gear manufacturing:
- Advanced CNC Machining: Computer Numerical Control (CNC) machining has revolutionized gear manufacturing. High-precision CNC machines equipped with multi-axis capabilities can produce complex spiral bevel gear geometries with tight tolerances. CNC machining allows for greater flexibility in gear design and ensures consistent and accurate production.
- 3D Printing/Additive Manufacturing: Additive manufacturing, also known as 3D printing, has the potential to transform the production of spiral bevel gears. While not yet widely adopted for mass production, 3D printing offers advantages in prototyping and low-volume production. It allows for the creation of intricate gear designs and customizations with reduced material waste.
- High-Performance Cutting Tools: Advancements in cutting tool technology, such as diamond-coated or carbide cutting tools, have improved the efficiency and precision of gear cutting processes. These cutting tools can withstand higher temperatures and wear, resulting in longer tool life and better gear surface finish.
- Multi-Axis Gear Grinding: Gear grinding is a critical process for achieving precise tooth profiles and surface finish. Innovations in multi-axis gear grinding machines allow for simultaneous grinding of multiple tooth surfaces, reducing production time and improving gear accuracy.
- Computer-Aided Design (CAD) and Simulation: CAD software and advanced simulation tools enable engineers to design and analyze gear geometry more efficiently. Finite Element Analysis (FEA) and computational fluid dynamics (CFD) simulations help optimize gear performance, reduce stress concentrations, and identify potential issues before physical production.
- Improved Heat Treatment Processes: Heat treatment is a crucial step in gear manufacturing to achieve desired material properties. Innovations in heat treatment processes, such as induction hardening and case carburizing, allow for better control of material hardness and distortion during heat treatment.
- Hard Finishing Methods: Innovations in hard finishing methods, such as honing and lapping, can enhance gear tooth surface quality and improve the running-in characteristics of gears, reducing friction and wear during initial operation.
- Automated Inspection and Quality Control: Automated inspection technologies, including coordinate measuring machines (CMMs) and non-destructive testing methods, enable faster and more accurate inspection of gear profiles and quality control, ensuring that gears meet stringent requirements.
- Green Manufacturing Practices: Manufacturers are increasingly adopting green manufacturing practices, such as using eco-friendly lubricants and reducing energy consumption during production, to minimize the environmental impact of gear manufacturing processes.
These engineering innovations collectively contribute to producing higher-quality spiral bevel gears with improved performance characteristics. As technology continues to advance, gear manufacturers will likely explore more cutting-edge methods to further enhance the efficiency and reliability of spiral bevel gear production.