Cylindrical helical gear is a common transmission component in industrial machinery, which is widely used in transportation, aviation, shipbuilding and other industries. In the process of industrialization and informatization, the parameter design and related detection technology in the processing of cylindrical helical gears are still a hot research direction. Compared with general cylindrical spur gears, the tooth surface structure of cylindrical helical gears is relatively complex, and the tooth line will produce non axial force in the processing process, resulting in certain manufacturing errors of the processed gears. Because the accuracy of machining parameters of cylindrical helical gears directly determines the performance and life of the whole mechanical equipment in the working process, the gear machining parameter detection system is very critical in the machining program of cylindrical helical gears.
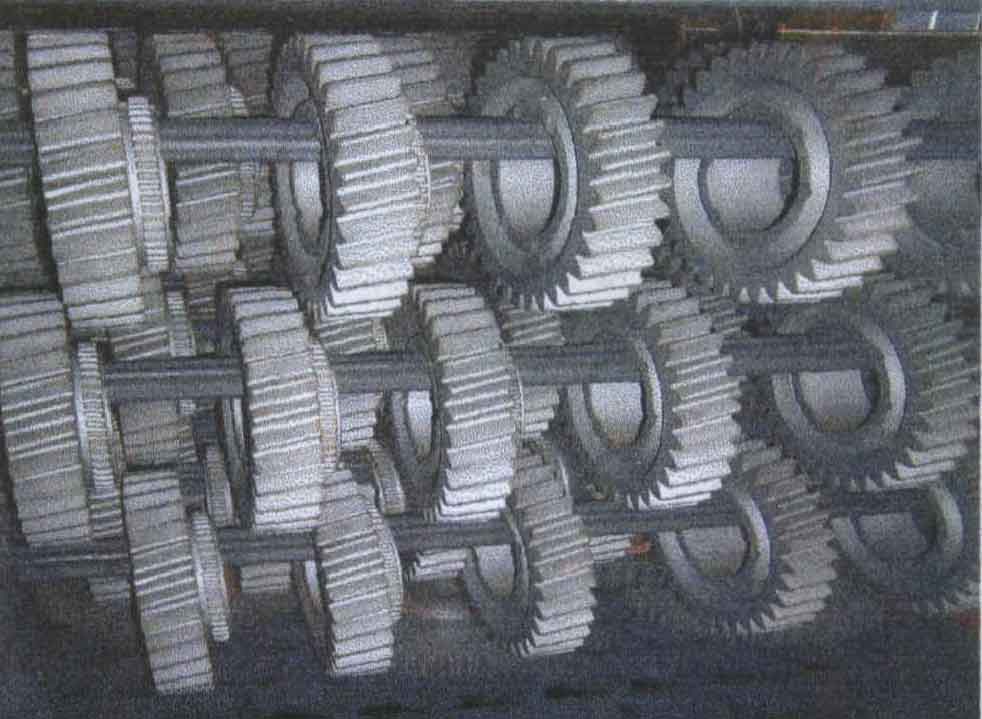
The traditional CNC cylindrical helical gear measurement system can accurately measure the processing parameters of cylindrical helical gears in the actual work process, but it does not consider the small errors in the processing and manufacturing process of cylindrical helical gears. Compared with the real parameter results, the measurement results will inevitably have large deviations. In view of this, a cylindrical helical gear processing parameter measurement system considering manufacturing error is designed.
In view of the defects in the application of the traditional CNC cylindrical helical gear measurement system, the machine vision technology is introduced into the design of the cylindrical helical gear processing parameter measurement system, and the manufacturing error is considered in the actual measurement, so as to reduce the deviation between the parameter measurement results and the real results. The system has made some achievements in the experiment, but there are also many shortcomings (for example, the selection of parameters is too few). In the future research, we need to add a variety of processing parameters to design and measure, so as to make the function and performance of the system more stable.