Abstract:
With the rapid development of the coal industry, the stability of scraper reducer bevel gear pairs, as the core components of coal mine conveying systems, directly affects the safety and efficiency of the entire production line. This article analyzes common types of damage, preventive measures, and new ideas for bevel gear pairs in scraper reducers to ensure the smooth progress of coal production.
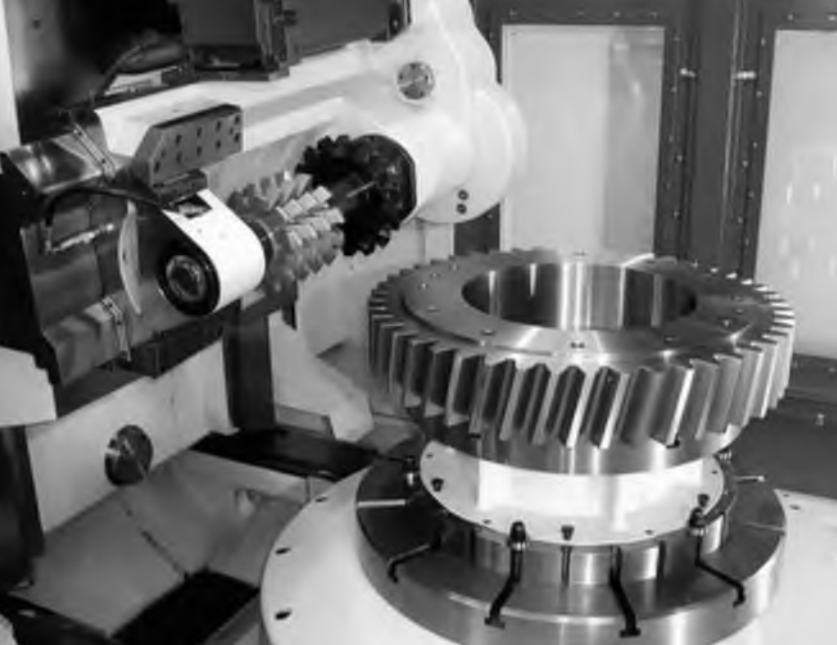
Keywords: coal mine, scraper reducer, bevel gear pair, damage, prevention
1. Introduction
Coal mines play a vital role in the energy industry, and their safe and efficient operation is directly related to the stability and development of the national economy. In the coal mine’s material conveying system, the scraper reducer serves as a critical transmission device ensuring continuous and stable material conveying. As a key component of the scraper reducer, the reliability of the bevel gear pair is fundamental to the normal operation of the entire coal mine transportation system.
2. Common Types of Damage to Bevel Gear Pairs in Scraper Reducers
Below is a summary of common damage types to bevel gear pairs in scraper reducers, presented in a table:
Damage Type | Description | Impact |
---|---|---|
Tooth Surface Wear | Caused by long-term use or foreign objects entering between gear pairs, leading to increased friction on the tooth surface. | Reduces gear meshing accuracy, affects transmission smoothness and precision, increases noise and vibration. |
Tooth Surface Spalling | Resulting from material defects, improper heat treatment, low processing accuracy, or poor assembly during manufacturing or use. | Affects gear carrying capacity and service life, requiring timely repair or replacement. |
Gear Fracture | Often caused by excessive loads or impacts on the gear, poor material quality, or inadequate manufacturing processes. | May cause equipment accidents if not addressed immediately. |
Bearing Wear | Mainly occurs at the installation position due to small interference fit between the bearing and the gear, causing the inner ring of the bearing to rotate during use. | Affects the support and fixation of the gear. |
3. Causes of Bevel Gear Pair Damage
The causes of bevel gear pair damage in scraper reducers can be summarized in the following table:
Cause | Description |
---|---|
Manufacturing Quality Issues | Inappropriate material selection, insufficient material hardness, material defects, and improper heat treatment can lead to accelerated tooth surface wear or fractures. |
Improper Assembly and Adjustment | Misalignment of gear axes, improper meshing clearance, and excessive or insufficient bearing preload can all affect gear operation performance. |
Operating Conditions | Extreme temperatures, corrosive environments, dust, vibration, and shock loads can all impact the service life of bevel gears. |
Inadequate Maintenance | Lack of regular inspections, loose fasteners, and failure to repair minor wear or damage in a timely manner can accelerate gear damage. |
4. Prevention Strategies for Bevel Gear Pair Damage
To prevent bevel gear pair damage in scraper reducers, the following strategies can be implemented:
4.1 Improving Manufacturing and Assembly Quality
Strategy | Description |
---|---|
Material Selection | Use high-quality alloy steel with high strength, wear resistance, and fatigue resistance. |
Manufacturing Process Control | Ensure precise shapes and stable dimensions through precision casting or forging. Implement appropriate heat treatment to achieve the required hardness and internal structure. |
Precision Control | Strictly control gear precision during cutting and grinding processes to reduce errors and improve meshing quality. |
4.2 Strengthening Management During Use
Strategy | Description |
---|---|
Operating Procedures | Provide detailed operating procedures for operators to ensure they understand correct operation methods, precautions, and safety requirements. |
Regular Inspections | Establish a regular inspection and maintenance system to check key areas such as tooth surface wear, backlash changes, and bearing condition. |
Monitoring Systems | Install sensors and monitoring systems to monitor the bevel gear pair’s working conditions, such as temperature, vibration, and noise, and analyze and provide early warnings for abnormal data. |
4.3 Regular Maintenance and Servicing
Strategy | Description |
---|---|
Regular Checks | Check the appearance of the bevel gear pair, tooth surface wear, cracks, or deformation. Ensure the axial and lateral clearance is within the appropriate range and tighten all bolts fixing the bevel gear. |
Lubrication | Select appropriate lubricants based on manufacturer recommendations, establish lubrication cycles, and use appropriate lubrication tools to ensure all contact surfaces are adequately lubricated. |
Cleaning | Regularly clean the inside of the reducer and the bevel gear surface to remove any residual impurities or dirt. |
5. Conclusion
Ensuring the stability of bevel gear pairs in coal mine scraper reducers is crucial for production safety and efficiency. The harsh environment, operational complexity, and inadequate maintenance can all lead to damage to this core transmission component. By implementing the above strategies, we can minimize bevel gear pair damage, ensuring the smooth progress of coal production while protecting our valuable labor resources and the environment.