This article focuses on the complex mechanism and easily fluctuating load problems of crack faults in gear systems. It first proposes a modified algorithm based on the potential energy method to analyze the influence of crack parameters on the time-varying meshing stiffness. Then, a gear system dynamics model considering comprehensive meshing errors is established to study the vibration response characteristics of cracked gear systems under stable and variable load conditions. Additionally, five statistical indicators are used to conduct sensitivity analysis on the vibration signals of cracked gears. The results show that as the crack depth and angle increase, the meshing stiffness decreases, with the crack depth having a greater impact. The periodic impact in the time domain and the amplitudes of sidebands around the meshing frequency and its harmonics in the frequency domain are positively correlated with the degree of crack propagation. Under variable load conditions, the vibration signal is similar to the load fluctuation trend, the low-frequency component is related to the load, and the larger the fluctuation amplitude, the less obvious the fault characteristics. The kurtosis is the most sensitive to the vibration signals of cracked gears.
1. Introduction
Gear transmission systems are widely used in various fields such as wind power generation and aerospace. Due to their complex working conditions, they are prone to failures. Among them, gear tooth breakage has the highest fault proportion, accounting for about 41% of gear faults, and the early manifestation of tooth breakage is cracks. Crack faults can affect the vibration response of the system through internal incentives in the gear system. Therefore, the analysis and research of the dynamics of gear systems with tooth root crack faults are of great significance in the field of system condition monitoring and fault diagnosis.
The time-varying meshing stiffness, as the most important internal excitation source in the gear system, and its dynamic response characteristics are important bases for gear system fault diagnosis. At present, the main calculation methods of meshing stiffness include the finite element method, the potential energy method, and the Ishikawa method. Since the finite element method requires fine meshing and a long calculation time, and the Ishikawa method has complex crack characterization after quantification, the more efficient and convenient potential energy method is widely used. Many scholars have studied the meshing stiffness of cracked gears. For example, Wan Zhiguo et al. corrected the situation where the tooth root circle and the base circle do not coincide and analyzed the influence of different depths of tooth root cracks on the time-varying meshing stiffness. Xu Kejun et al. divided the tooth profile into involute and transition curves and proposed an improved algorithm based on the potential energy method. Yu Yaoting proposed an energy method for calculating gear meshing stiffness considering the free energy of the tooth root crack surface and verified it by the finite element method.
In the analysis of the vibration response of gears with crack faults, many scholars have also carried out research. For example, Liu Jie et al. calculated the meshing stiffness of cracked gears using the potential energy method and the finite element method and analyzed their vibration response characteristics. Meng Zong et al. analyzed the vibration characteristics of gears with crack faults based on the accurate time-varying meshing stiffness algorithm. Mo Shuai et al. studied the dynamic characteristics and fault mechanism of gear systems under different crack propagation paths. Xiang et al. established a translational-torsional dynamic model of a multi-stage gear system with tooth root cracks and analyzed the dynamic characteristics of the cracked gear system from a nonlinear perspective. Wang Hongwei et al. analyzed the dynamic response characteristics of gears under different local faults based on the full finite element model of the gear transmission system. Zhang Xu et al. studied the influence of tooth surface flash temperature on the dynamic response of crack faults in wind turbine gearboxes.
However, in the actual operation of the gear system, unstable working conditions such as speed fluctuation or load fluctuation may occur, which brings great difficulties to system fault diagnosis. Therefore, the dynamic mechanism and diagnosis method of gear system crack faults under variable working conditions need to be further studied. Dai Peng et al. analyzed the vibration characteristics of cracked gear pairs under variable working conditions and found that the gear vibration amplitude increases with the increase of speed and load. However, the above research only considered the case of uniform load change and did not consider the case of load fluctuation.
Therefore, based on the previous research work, this article intends to appropriately modify the potential energy method, establish a full-depth tooth root crack model, and more accurately and comprehensively analyze the influence law of crack parameters on the time-varying meshing stiffness. It also intends to establish a 6-degree-of-freedom gear system dynamics model considering comprehensive meshing errors to analyze the influence of tooth root cracks on the vibration response characteristics of the gear system under stable and variable load conditions, providing an effective dynamic supplement for the crack fault diagnosis of the gear transmission system.
2. Time-Varying Meshing Stiffness Calculation Model
The accuracy of the calculation of the time-varying meshing stiffness, as the most important internal excitation of the gear system vibration, determines the reliability of the dynamic analysis of the gear system. At present, the potential energy method is generally used to solve the time-varying meshing stiffness in most studies, only considering the deformation energy of the contact between the teeth on the base circle. To address the above problems, this article intends to appropriately modify the potential energy method to improve the accuracy of gear modeling.
2.1 Healthy Gear Meshing Stiffness Calculation Model
The core idea of the potential energy method is to construct the gear as a non-uniform cross-section cantilever beam model on the base circle. According to the axial compression deformation energy , bending deformation energy , and shear deformation energy stored by the gear under the action of the meshing force, considering the deformation of the gear matrix and the Hertz contact on the meshing line of the two gears, the comprehensive meshing stiffness of the gear as a whole can be obtained. However, due to different gear parameters, the base circle and the tooth root circle may not coincide. Therefore, it is necessary to appropriately modify the potential energy method to improve the calculation accuracy of the meshing stiffness.
Parameter | Driving Wheel | Driven Wheel |
---|---|---|
Module/mm | 1.5 | 1.5 |
Number of Teeth | 36 | 90 |
Pressure Angle/° | 20 | 20 |
Tooth Width/mm | 12 | 12 |
Elastic Modulus/GPa | 206 | 206 |
Poisson’s Ratio | 0.289 | 0.289 |
Inner Hole Diameter/mm | 16.7 | 41.8 |
2.1.1 Modification of the Potential Energy Method
Since the part between the tooth root circle and the base circle is not an involute and the analysis is relatively complex, this part is simplified as a straight line for calculation as shown in Figure 1. Then, the modified formulas for bending energy, compression energy, and shear energy can be expressed as follows:
where is the force acting on the meshing point, which can be decomposed into a radial force and a tangential force ; and are the base circle radius and the tooth root circle radius, respectively; is the elastic modulus; is the shear modulus; is Poisson’s ratio; and are the moments of inertia of the gear section at distances and from the base circle, respectively; and are the cross-sectional areas; is the distance from the meshing point to the base circle; is the distance from the meshing point to the center line of the tooth; is the height of the section at a distance from the base circle; is the half-tooth angle on the base circle, and represents the approximate half-tooth angle on the tooth root circle.
Combined with the gear tooth profile characteristics, the following can be derived:
According to the Hertz contact theory, it is considered that the Hertz contact stiffness is independent of the load and the contact point. Therefore, the Hertz contact stiffness can be expressed as follows:
where is the elastic modulus, is the gear width, and is Poisson’s ratio.
Based on the elastic ring theory, taking the tooth root circle as the outer diameter and the shaft hole as the inner diameter, the formula for calculating the deformation stiffness of the gear matrix is obtained as follows:
where is the distance from the intersection point of the force action line and the tooth center line to the tooth root, is the arc length of the single-tooth tooth root, and , , , and can be calculated from the following polynomials. is the ratio of the tooth root circle radius to the shaft hole radius, and is the central angle corresponding to the half-tooth root arc. The matrix calculation parameters are shown in Reference [15].
The comprehensive meshing stiffness during single-tooth meshing, considering the three deformation energies, Hertz contact, and gear matrix deformation, is:
In Equation (10), the subscript 1 represents the driving wheel, and the subscript 2 represents the driven wheel.
The comprehensive meshing stiffness during double-tooth meshing is:
In Equation (11), represents the -th pair of meshing gears.
2.1.2 Comparison and Verification of the Modified Potential Energy Method
The ISO 6336-1-2006 standard specifies the calculation method of gear meshing stiffness. The maximum value of the single-tooth meshing stiffness is:
The average value of the tooth stiffness is:
where is the theoretical single-tooth meshing stiffness, the theoretical correction coefficient , the gear matrix structure parameter , the basic tooth profile coefficient , is the gear helix angle, and is the gear contact ratio.
To verify the effectiveness of the stiffness calculation method in this article, the potential energy method is denoted as ; the method in this article is denoted as ; and the results obtained by referring to the ISO standard are also considered. The comparison and analysis of the calculation results of the three methods are shown in Table 2.
Method | Maximum Single-Tooth Meshing Stiffness/×10⁶ (N/m) | Relative Error with ISO Standard/(%) | Average Time-Varying Meshing Stiffness/×10⁶ (N/m) | Relative Error with ISO Standard/(%) |
---|---|---|---|---|
ISO Standard | 1.84 | 0 | 2.89 | 0 |
A | 2.34 | 27.17 | 3.73 | 29.07 |
B | 1.98 | 7.61 | 3.1 | 7.27 |
It can be seen from Table 2 that Method A ignores the deformation energy between the base circle and the tooth root circle, resulting in a larger calculated stiffness value. The maximum error of the single-tooth meshing stiffness is 27.17%, and the average meshing stiffness error is 29.07%. Method B supplements the calculation of the deformation energy between the tooth root circle and the base circle. The maximum error of the single-tooth meshing stiffness is 7.61%, and the average meshing stiffness error with the ISO standard is 7.27%, effectively improving the accuracy of the gear model and verifying the effectiveness of the stiffness calculation and analysis in this article. |
2.2 Cracked Gear Meshing Stiffness Calculation Model
Due to the pulsating cyclic contact stress on the tooth root of the gear, cracks are prone to occur. In this article, it is assumed that the crack is a through crack, and the crack propagation line is symmetrically distributed with respect to the tooth center line. The limiting line of crack propagation is a straight line.
Figure 3 shows the geometric model of the tooth root crack. is the initial crack depth that does not reach the tooth center line, is the crack length that exceeds the tooth center line as the gear crack propagates, the total crack length , is the maximum depth when the crack propagates to the tooth center line, and is the crack propagation angle.
Since the area enclosed by the crack propagation line, the limiting line, and the tooth profile line will fail, resulting in a decrease in the effective cross-sectional area and moment of inertia at the meshing point. Therefore, according to the different crack propagation depths, the crack calculation model is divided into the following three cases. Models 1 and 2 correspond to the crack propagation depth less than 50% (measured by the percentage of in to measure the degree of tooth root crack propagation), and Models 3 and 4 correspond to the crack propagation depth greater than 50%.
Model 1: In the initial stage of the crack, the crack propagation line does not reach the upper half-tooth tip thickness, that is, , and .
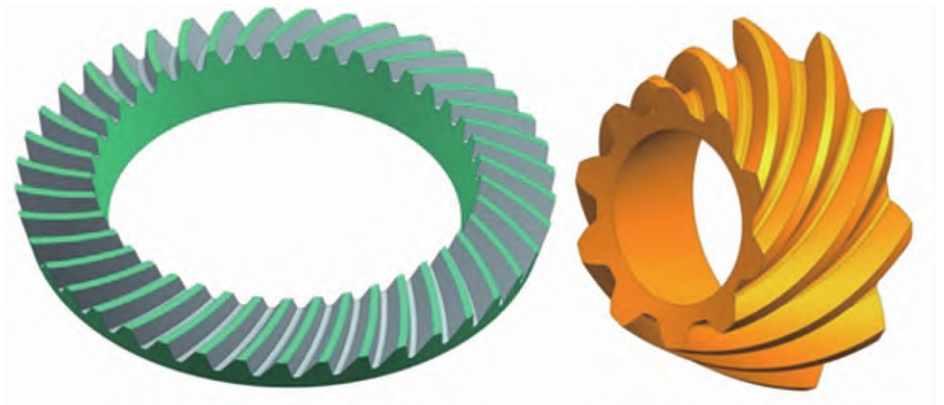