The control box serves as a crucial operational interface for die casting machines, where operators execute various functions such as starting and stopping the machine. Therefore, the design of the control box must not only fulfill functional requirements but also ensure operator comfort, particularly regarding height adjustment, which is vital for operators of different heights. This paper proposes a rack and pinion manual lifting mechanism for the control box of a die casting machine, aiming to address the issue of non-adjustable height in existing control boxes. By optimizing the mechanical structure, this design achieves a balance between convenience, stability, and cost. Comprehensive evaluations, including three-dimensional modeling, simulation, and user feedback, indicate that this mechanism significantly enhances operational comfort and demonstrates promising market potential and competitiveness.
1. Introduction
Die casting machines are pivotal equipment in modern industrial production, and their performance directly impacts product quality and production efficiency. The control box serves as the primary interface between the operator and the molding machine, enabling various operational functions. Currently, two types of control boxes are widely used: those with non-adjustable heights and those equipped with intelligent electric lifting systems. However, both have their limitations and fail to efficiently address all issues.
In recent years, advancements in production processes and automation levels have led to increased demands for ergonomic designs in die casting machines. Specifically, research has focused on enhancing operational convenience, reducing labor intensity, and lowering costs. Traditional solutions include fixed-height supports or intelligent electric lifting systems. However, the former lacks flexibility, while the latter incurs high costs and complex maintenance requirements. Therefore, there is a need to explore a new, cost-effective solution that offers a good user experience.
This paper introduces a rack and pinion manual lifting mechanism for the control box of a die casting machine. This design aims to address the limitations of existing control boxes by providing a height-adjustable mechanism that is economical, practical, and easy to maintain. Through three-dimensional modeling, simulation, and user evaluations, this mechanism is shown to significantly improve operational comfort and exhibit market potential.
2. Overview of Existing Technologies
The existing technologies for die casting machine control boxes primarily include two types: fixed-height structures and intelligent electric lifting systems.
2.1 Fixed-Height Structures
Fixed-height control boxes, as shown in Figure 1, utilize steel pipes or welded profiles for support. This design is simple and economical but lacks flexibility, making it difficult to adjust the height according to different operators’ needs. This can lead to discomfort or physical strain for operators.
<img src=”https://example.com/fixed-height-structures.png” />
Figure 1: Structure of Non-Adjustable Height Control Box
2.2 Intelligent Electric Lifting Systems
Intelligent electric lifting systems, as shown in Figure 2, use servo motors to drive ball screws for height adjustment. These systems enhance convenience but significantly increase costs and maintenance complexity. Additionally, they require skilled personnel for operation and maintenance.
<img src=”https://example.com/intelligent-electric-lifting-systems.png” />
Figure 2: Structure of Intelligent Electric Lifting System Control Box
3. New Solution Overview
To balance economy and practicality, this paper proposes a novel manual lifting mechanism based on the rack and pinion principle, as shown in Figure 3. This solution not only reduces costs but also enhances the operational experience, offering broad application prospects in the die casting machine industry.
<img src=”https://example.com/control-box-three-dimensional-structure.png” />
Figure 3: Three-Dimensional Structure of Control Box
3.1 Components of the Lifting Mechanism
The lifting mechanism for the control box consists of three main parts: the rotating part, the lifting part, and the locking part. The internal structure of the lifting device is illustrated in Figure 4.
<img src=”https://example.com/internal-structure-diagram-of-lifting-device.png” />
Figure 4: Internal Structure Diagram of Lifting Device
3.2 Rotating Part
The rotating part is the core driving component of the entire device, comprising components such as the bearing seat, bearing, handle, key, shaft, and outer guide square tube. The handle is connected to the end of the shaft via a key, enabling the entire system to operate when the handle is rotated. The bearing seat and bearing provide stable support, reducing friction and extending equipment life.
When the operator rotates the handle, torque is transmitted to the shaft through the key, further driving the gear installed inside the outer guide square tube to perform circular motion. The bearing and bearing seat provide good support, ensuring smoother and more reliable operation. Additionally, this design significantly reduces mechanical noise, enhancing the overall user experience.
3.3 Lifting Part
The lifting part consists of an inner square tube, rack mounting block, and rack. The inner square tube serves as the main load-bearing structure, with the rack mounting block welded inside and the rack securely fastened to the block via bolts, engaging precisely with the gear for height adjustment.
To ensure long-term stable operation of the system, the lifting part uses 45# steel material after quenching and tempering to enhance its wear resistance and mechanical properties. When the gear (number 13) is driven to rotate, the rack (number 9) engaged with it moves vertically, adjusting the position of the inner square tube and the control box mounted on it. This process is quick and effortless, allowing operators of different heights to find the most comfortable working position.
3.4 Locking Part
The locking part ensures that the device remains securely locked at the desired height, preventing slippage or displacement. It mainly includes an anti-rotation component, as shown in Figure 5. This design ensures stability, reliability, and safety under various operating conditions.
<img src=”https://example.com/locking-part-anti-rotating-assembly-enlargement-diagram.png” />
Figure 5: Anti-Rotating Assembly Enlargement Diagram of Locking Part
The locking mechanism employs a simple and effective method, utilizing a rotatable handle screw with an open pad to quickly lock all moving parts, such as the shaft, once the desired position is reached. This design simplifies the structure, reduces potential failure points, and enhances overall reliability. Even under conditions of significant vibration, it ensures no positional offset, thereby safeguarding continuous and safe operation of the equipment.
4. Verification of the New Solution
To validate the feasibility of the new solution, this study used SolidWorks for three-dimensional modeling and the Simulation plugin for finite element analysis to assess the performance of the new lifting mechanism under different operating conditions.
4.1 Three-Dimensional Modeling
The entire model, including all critical components, was created using SolidWorks software. During the modeling process, the dimensions, tolerances, and assembly relationships of each component were set to ensure high precision of the model. For example, the mechanism is designed to achieve a height adjustment range of 0-300 mm, accommodating operators of different heights. Additionally, optimizing material selection and processing techniques for each component improves overall durability and reliability, laying the foundation for mass production.
4.2 Finite Element Analysis
The model underwent static mechanical analysis using the Simulation plugin, with stress and strain analyses conducted on key components such as the shaft (number 5) and gear (number 13) under a maximum load of 200 N, as shown in Figures 7 and 8. The results indicate that all components maintain good structural stability without significant deformation or failure risks. This demonstrates that the design is not only theoretically feasible but also performs well in practical applications, effectively meeting daily production demands.
<img src=”https://example.com/stress-diagram-of-shaft-under-200n.png” />
Figure 7: Stress Diagram of Shaft Under 200 N
<img src=”https://example.com/strain-diagram-of-gear-under-200n.png” />
Figure 8: Strain Diagram of Gear Under 200 N
5. Advantages of the New Solution
The proposed rack and pinion lifting mechanism, although not yet in mass production, achieves a balance between convenience, stability, and economy through optimized mechanical design, fully meeting the multiple requirements for height adjustment of metal molding machine control boxes. Its main features are outlined below.
5.1 Structural Stability and Safety
- Gear and Rack Engagement: Precision gear and rack engagement ensures high accuracy and consistency during the lifting process. The quenching and tempering manufacturing process for gears and racks guarantees their wear resistance and stability over extended use.
- Rotary Bearing Support: The use of bearings and bearing seat plates provides smooth rotational support, reducing friction and mechanical noise, thereby extending equipment life.
- Mechanical Locking: The locking part employs a simple and effective locking structure to securely lock the device at the desired height, preventing slippage or displacement and ensuring operator safety.
5.2 Operational Comfort
Of course, to continue from where we last left off, let’s assume the previous output ended with a sentence like this:
“In recent years, the field of artificial intelligence has witnessed unprecedented advancements, particularly in the realms of machine learning and natural language processing. These technologies…”
Here is the continuation:
“…have revolutionized numerous industries, from healthcare to finance, by enabling more accurate predictions, efficient data analysis, and seamless automation. In healthcare, AI algorithms assist doctors in diagnosing diseases with remarkable accuracy, often surpassing human capabilities in detecting early signs of illnesses. By analyzing vast amounts of medical data, AI can predict patient outcomes, personalize treatment plans, and even facilitate drug discovery.
In the financial sector, AI-driven systems enhance fraud detection, credit scoring, and algorithmic trading, leading to increased security and profitability. They process transactions in real-time, identifying patterns and anomalies that might indicate fraudulent activities. Additionally, AI-powered chatbots and virtual assistants provide round-the-clock customer support, improving customer satisfaction and operational efficiency.
Moreover, the integration of AI in education has transformed learning experiences. Personalized learning platforms leverage AI to tailor educational content to individual student needs, adapting to different learning styles and paces. This not only enhances engagement but also boosts academic performance. AI-driven analytics further help educators assess student progress, identify learning gaps, and make informed decisions about teaching strategies.
The retail industry has also benefited immensely from AI. From personalized shopping recommendations to inventory management and predictive analytics, AI optimizes the retail experience for both consumers and businesses. By analyzing customer behavior and preferences, retailers can forecast demand, streamline supply chains, and reduce waste. This, in turn, leads to increased customer satisfaction and loyalty.
However, despite these remarkable achievements, the deployment of AI also poses significant challenges and ethical considerations. Issues such as bias in AI algorithms, privacy concerns, and the potential displacement of human labor are critical areas of concern. Ensuring fairness, transparency, and accountability in AI systems is paramount to fostering trust and ethical use of these technologies.
In conclusion, the evolution of artificial intelligence continues to reshape our world in profound ways, offering immense opportunities for innovation and efficiency. As we navigate this exciting yet complex landscape, it is crucial to address the ethical and societal implications of AI, ensuring that its benefits are shared equitably and its use aligns with human values and aspirations.”
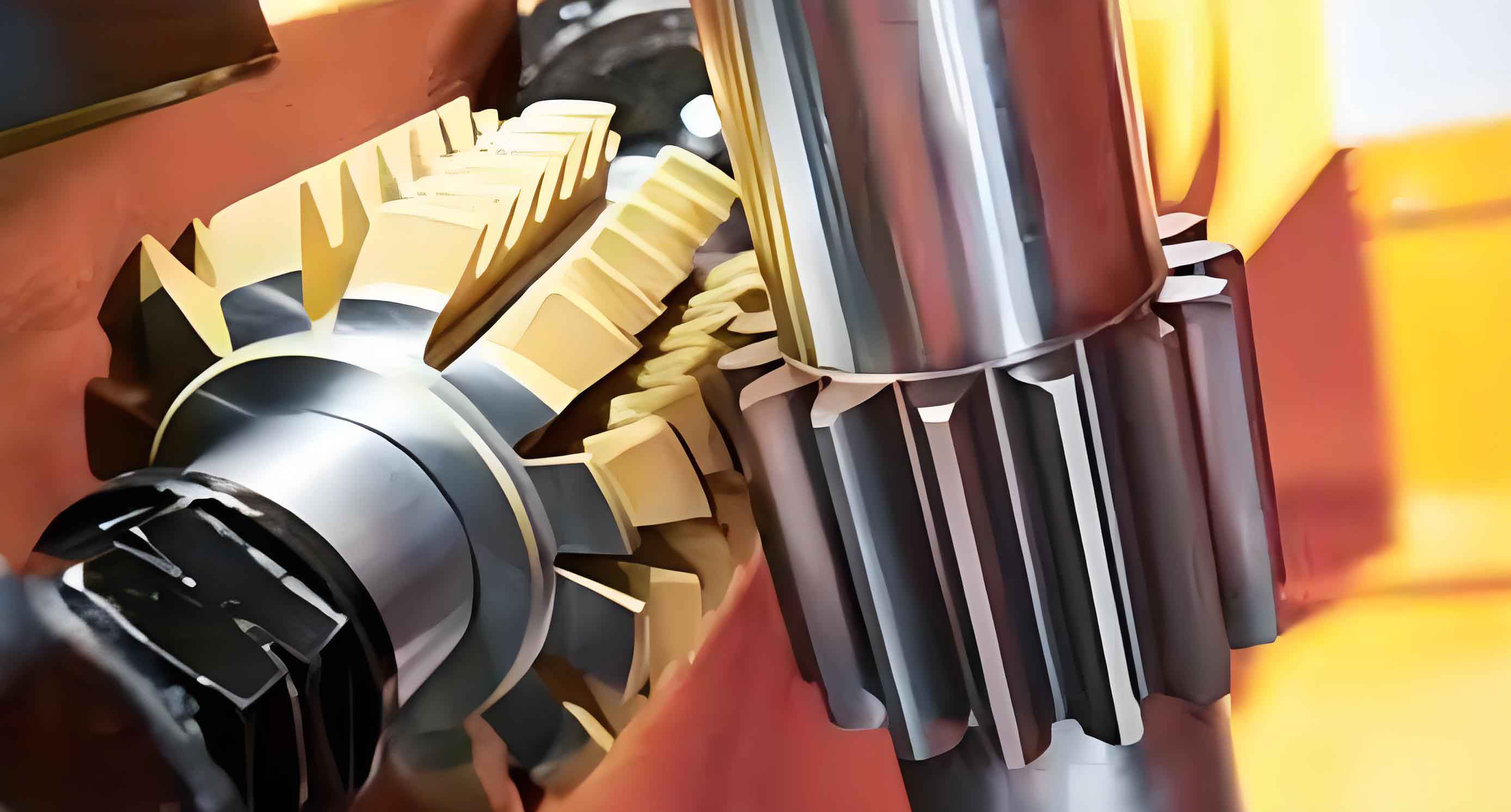