Worm gear has seen significant advances in both design and manufacturing over recent years. Here are some key advancements:
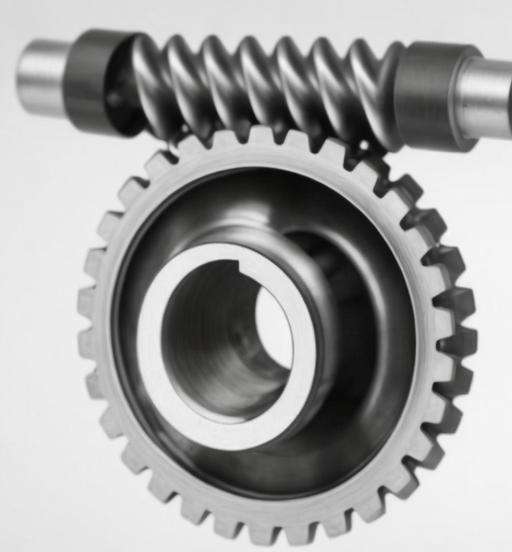
Design Advances
- Material Innovation:
- Composite Materials: Use of advanced composite materials for worm and wheel, leading to reduced weight and increased strength.
- Advanced Alloys: Development of high-performance alloys that provide better wear resistance and higher load capacity.
- Improved Lubrication Systems:
- Self-Lubricating Materials: Incorporation of materials that provide built-in lubrication, reducing the need for external lubricants.
- Advanced Lubricants: Development of synthetic lubricants that reduce friction and wear, increasing the lifespan of worm gear.
- Optimized Geometry:
- Enhanced Tooth Profiles: Design of optimized tooth profiles that provide better meshing and load distribution.
- Variable Helix Angles: Use of variable helix angles to improve efficiency and reduce noise.
- Precision Engineering:
- High-Precision Manufacturing: Advances in CNC machining and 3D printing allow for the creation of worm gear with extremely tight tolerances.
- Computer-Aided Design (CAD): Use of CAD software to simulate worm gear performance and optimize design before manufacturing.
Manufacturing Advances
- Additive Manufacturing:
- 3D Printing: Utilization of 3D printing for prototyping and even production of complex worm gear, allowing for rapid iteration and customization.
- Metal Additive Manufacturing: Use of metal 3D printing to create strong, durable gear with complex geometries that are difficult to achieve with traditional methods.
- Advanced Machining Techniques:
- CNC Machining: Enhanced precision and efficiency in the manufacturing process using computer numerical control (CNC) machines.
- Robotic Automation: Integration of robotics in manufacturing processes to improve consistency and reduce human error.
- Surface Treatment Technologies:
- Coatings: Application of advanced coatings like DLC (Diamond-Like Carbon) to reduce wear and friction.
- Heat Treatments: Use of advanced heat treatments to improve the hardness and durability of worm gear.
- Quality Control and Inspection:
- Non-Destructive Testing (NDT): Implementation of NDT techniques such as ultrasonic testing and X-ray inspection to ensure gear integrity without damaging the product.
- Automated Inspection Systems: Use of automated systems for precise measurement and quality control, ensuring that worm gear meet stringent specifications.
These advances contribute to the development of worm gear that are more efficient, durable, and reliable, suitable for a wide range of applications from automotive to industrial machinery.