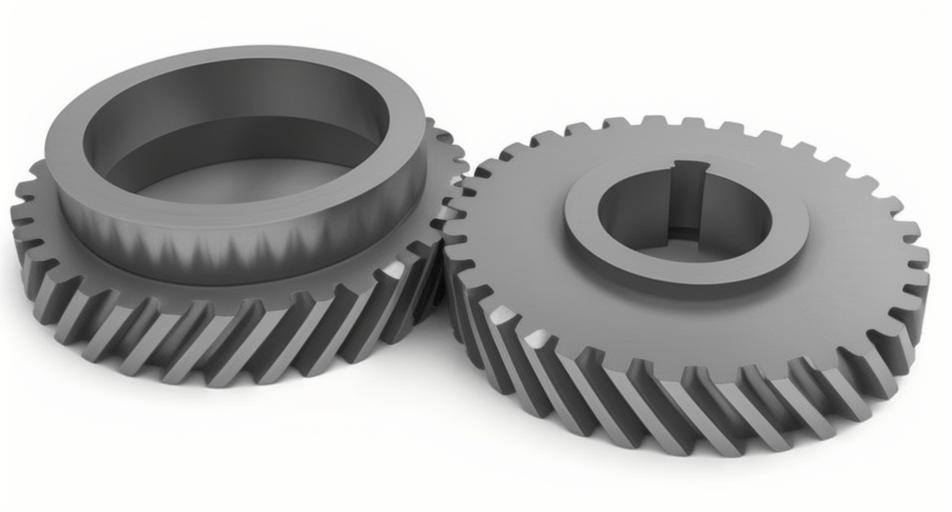
Common Causes of Helical Gear Failure
- Wear and Tear:
- Abrasive Wear: Caused by hard particles in the lubricant or surface roughness.
- Adhesive Wear (Scuffing): Results from metal-to-metal contact under heavy loads and insufficient lubrication.
- Fatigue Wear: Due to repeated stress cycles leading to material degradation.
- Pitting and Spalling:
- Pitting: Small pits form on the surface due to cyclic contact stress.
- Spalling: Severe form of pitting where larger chunks of material break away.
- Tooth Bending Fatigue:
- Repeated bending of helical gear teeth under load can lead to fatigue cracks, especially at the tooth root.
- Excessive Loads:
- Loads beyond helical gear’s design capacity can cause permanent deformation or breakage.
- Misalignment:
- Improper alignment of helical gear leads to uneven load distribution and increased stress on helical gear teeth.
- Lubrication Failures:
- Insufficient or improper lubrication increases friction and wear, leading to helical gear failure.
- Corrosion:
- Exposure to corrosive environments or moisture can degrade helical gear material, leading to failure.
- Manufacturing Defects:
- Inaccuracies in helical gear cutting, heat treatment, or material quality can lead to premature failure.
Prevention Techniques
- Proper Material Selection:
- Use high-quality materials suitable for the operating conditions, such as alloy steels with appropriate heat treatment.
- Accurate Gear Design:
- Ensure proper helical gear geometry, helix angle, and load capacity to match application requirements.
- Adequate Lubrication:
- Use the correct type and amount of lubricant and ensure proper maintenance of lubrication systems.
- Consider advanced lubricants like synthetics or nano-lubricants for enhanced performance.
- Alignment and Installation:
- Ensure precise alignment during installation to prevent uneven load distribution.
- Regularly check and adjust alignment as part of maintenance.
- Load Management:
- Avoid overloading helical gear by adhering to design specifications and using overload protection devices.
- Condition Monitoring:
- Implement vibration analysis, oil analysis, and other condition monitoring techniques to detect early signs of wear or failure.
- Regular Maintenance:
- Follow a consistent maintenance schedule to inspect helical gear, replenish lubricants, and address any issues promptly.
Repair Techniques
- Surface Grinding and Polishing:
- Minor surface damage such as pitting or scuffing can sometimes be repaired by grinding and polishing helical gear teeth.
- Tooth Replacement or Restoration:
- Severely damaged teeth can be restored by welding and reshaping, although this requires precise control to avoid introducing new stresses.
- In some cases, individual teeth can be replaced using insert techniques.
- Gear Reprofiling:
- Reprofiling involves reshaping helical gear teeth to correct wear patterns and restore proper tooth contact.
- Re-hardening:
- Surface hardening processes such as carburizing, nitriding, or induction hardening can restore hardness to worn gear teeth.
- Using Epoxy Resins:
- For temporary or emergency repairs, epoxy resins can be used to fill small cracks or pitted areas.
- Replacing Gears:
- In cases of extensive damage, it may be more cost-effective to replace the entire helical gear rather than repair it.
Case Study: Failure Analysis and Repair
Scenario:
- A helical gear in an industrial gearbox shows signs of pitting and scuffing after a few years of operation.
Steps for Analysis and Repair:
- Inspection:
- Conduct a visual and microscopic inspection of helical gear to identify the extent and type of wear.
- Perform oil analysis to check for contamination and wear particles.
- Root Cause Analysis:
- Investigate potential causes such as improper lubrication, excessive loads, or misalignment.
- Use vibration analysis to check for misalignment or imbalance in helical gear system.
- Preventive Measures:
- Improve lubrication practices by switching to a higher-quality synthetic lubricant and ensuring proper lubricant filtration.
- Check and correct alignment issues.
- Repair Process:
- Grind and polish minor pitting to restore a smooth surface.
- For areas with severe scuffing, reprofile helical gear teeth.
- Apply a surface hardening treatment to enhance wear resistance.
- Validation:
- Reassemble and test the gearbox under controlled conditions to ensure the repairs are effective.
- Implement regular condition monitoring to track gear performance.
Conclusion
Helical gear failure can result from various factors, including wear, misalignment, excessive loads, and lubrication issues. Understanding these causes and implementing effective prevention and repair techniques is crucial for maintaining the reliability and longevity of gear systems. Regular maintenance, proper lubrication, accurate alignment, and timely repairs can significantly reduce the risk of gear failure and ensure optimal performance in various industrial applications.