When forming spur bevel gears by “one fire and two forging”, the surface of the die cavity is in direct contact with the high-temperature gear blank. After the forgings bear high thermal load are out of the die, they need to use water-soluble graphite to cool and lubricate the cavity. The die repeatedly bears cold and thermal alternating loads, and the working conditions are very poor. In order to improve the die life, the die structure of “one fire two forging” process for planetary gear and half shaft gear was designed based on the process design and numerical simulation of precision forging for spur bevel gear.
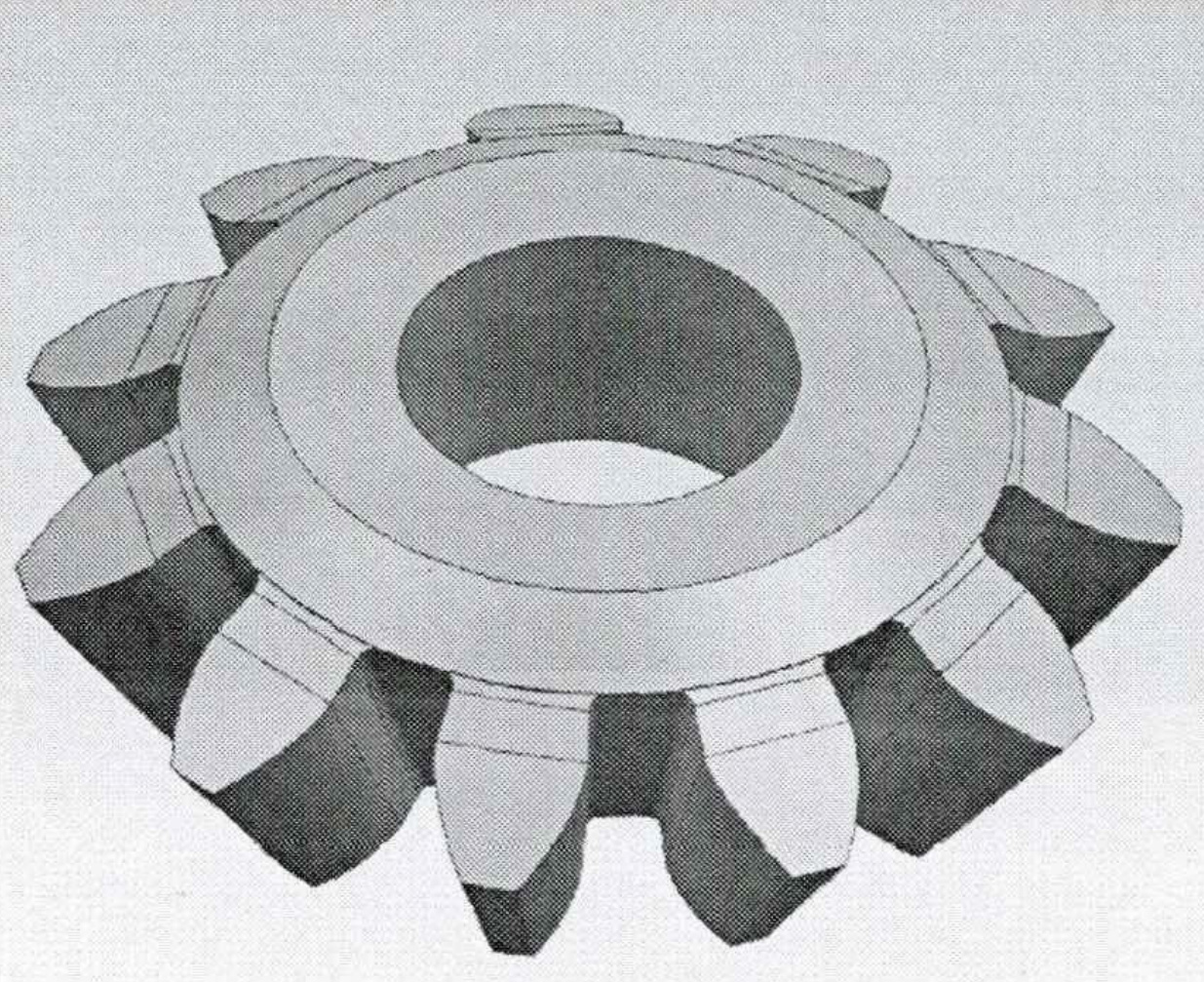
On the basis of precision forging process design and numerical simulation of spur bevel gear, two sets of die structures for forming spur bevel gear by “one fire two forging” are designed. The characteristics and working process of pre forging die and final forging die are discussed. The size design method of tooth die combination barrel and the machining method of tooth die cavity are given. The selection of die materials and the ways to improve the comprehensive properties of die materials are briefly introduced.