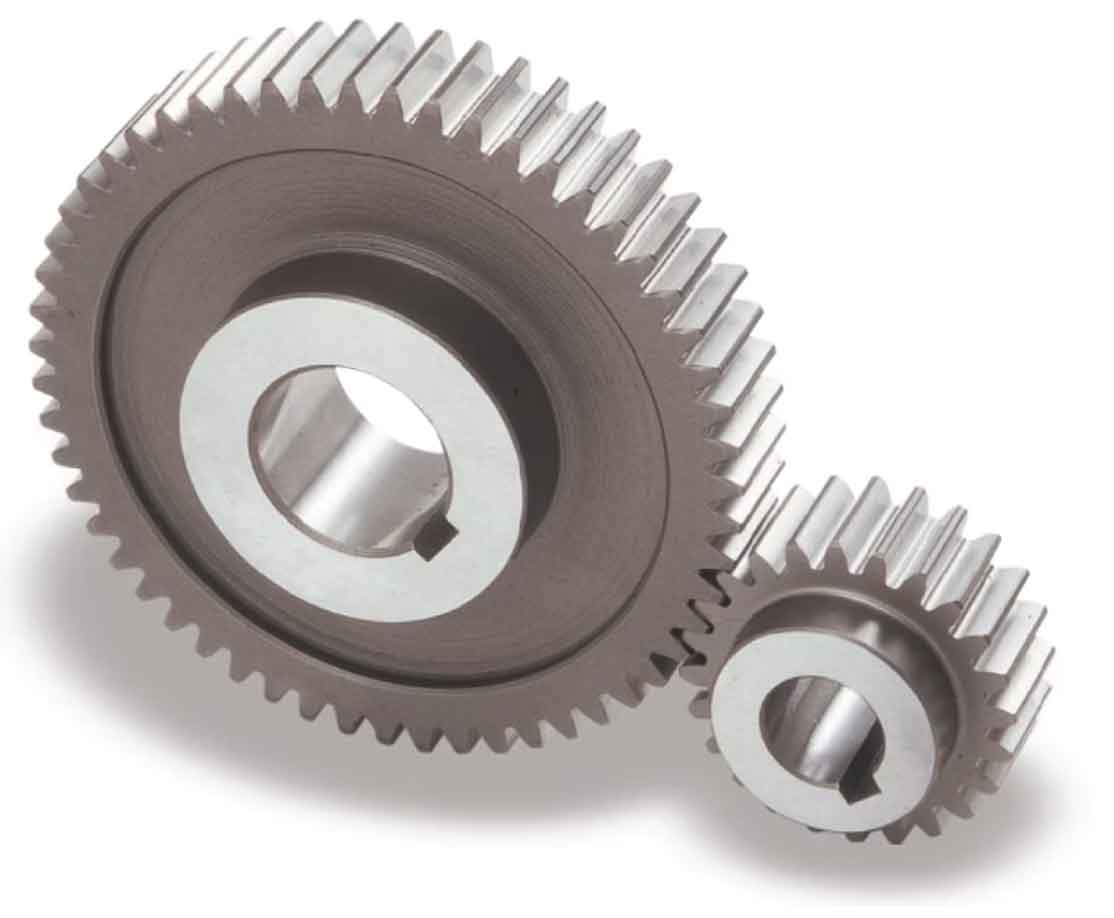
Designing efficient spur gear systems requires careful consideration of various factors to optimize performance, reduce energy losses, and ensure reliable operation. Here are some tips and best practices to help you design efficient spur gear systems:
1. Proper Gear Selection:
Choose the appropriate gear materials and sizes based on the application’s torque, speed, and load requirements. Selecting high-quality materials and precise gear dimensions will improve efficiency and gear life.
2. Gear Ratio Optimization:
Optimize the gear ratio to achieve the desired speed and torque output. Avoid unnecessary gear stages to minimize power losses and increase overall system efficiency.
3. Gear Teeth Profile:
Ensure the gear teeth profile is accurate and designed for smooth and efficient engagement. Tooth profiles can affect noise, vibration, and efficiency, so optimizing them is essential for efficient gear systems.
4. Gear Geometry and Alignment:
Maintain proper gear geometry and ensure precise alignment between mating gears. Misalignment can lead to increased friction, wear, and energy losses.
5. Lubrication and Maintenance:
Proper lubrication is crucial to minimize friction and wear in spur gears. Use the right lubricant and establish a regular maintenance schedule to ensure efficient operation and extend gear life.
6. Backlash Control:
Control backlash to maintain the required clearance between mating gears without excessive play. Proper backlash control ensures efficient power transmission and reduces gear noise.
7. Noise and Vibration Reduction:
Employ noise and vibration reduction techniques to reduce energy losses due to gear meshing impact. These techniques can include gear tooth modifications, surface finishing, and the use of noise-damping materials.
8. Heat Dissipation:
Design the gear system to facilitate heat dissipation. Proper ventilation and cooling mechanisms prevent excessive temperature buildup and improve gear efficiency.
9. Material Selection:
Choose gear materials with the right hardness and wear resistance to withstand the specific operating conditions. High-quality materials reduce friction losses and enhance gear durability.
10. Efficiency Testing and Analysis:
Perform efficiency testing and analysis of the gear system to identify potential areas of improvement. Finite element analysis (FEA) and other simulation tools can help predict gear system performance and guide design optimizations.
11. Consider Gear System Integration:
Integrate the spur gear system seamlessly with other components in the machinery or equipment. Proper integration ensures that the entire system operates efficiently as a whole.
12. Optimize Bearing Selection:
Select suitable bearings for supporting the gears and minimizing power losses due to friction. High-quality bearings contribute to overall system efficiency.
13. Design for Load Distribution:
Design the gear system to distribute loads evenly across the gear teeth. This prevents excessive wear on specific areas and enhances gear performance and longevity.
By following these tips and best practices, you can create efficient spur gear systems that deliver reliable performance, reduced energy consumption, and extended gear life in various industrial applications. Regular monitoring and maintenance of the gear system will also help sustain its efficiency and ensure smooth operation over time.