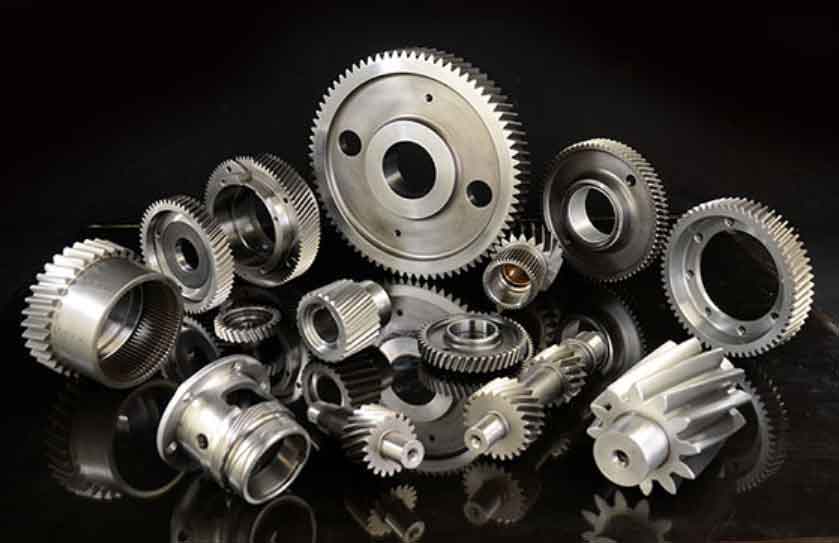
Precision engineering with helical gears involves careful consideration in design, manufacturing, and their applications to achieve high accuracy, performance, and reliability. Let’s explore each aspect in detail:
1. Design:
- Helix Angle Selection: The helix angle plays a crucial role in the design of helical gears. It affects the gear’s load-carrying capacity, efficiency, and noise level. The helix angle is chosen based on the specific requirements of the application.
- Tooth Profile: The tooth profile design must be precise to ensure smooth and efficient tooth engagement. Common tooth profiles used in helical gears include involute, cycloidal, and trochoidal.
- Gear Ratio: The gear ratio determines the speed and torque relationship between the meshing gears. Precise gear ratio selection is crucial to meet the desired speed and torque requirements.
- Material Selection: High-quality materials with the necessary hardness, strength, and wear resistance are chosen to ensure the gears can withstand the operating conditions.
2. Manufacturing:
- Gear Cutting Methods: Helical gears are typically manufactured using gear cutting methods such as hobbing, shaping, or milling. Each method has its advantages and is chosen based on factors like gear size, complexity, and production volume.
- Gear Grinding: In some cases, gear grinding is used to achieve even higher precision and surface finish, especially for high-performance applications.
- Heat Treatment: Proper heat treatment is crucial to achieve the desired material properties, such as hardness and toughness, for optimal gear performance.
- Quality Control: Strict quality control measures are employed throughout the manufacturing process to ensure the gears meet the required specifications.
3. Applications:
- Automotive Transmissions: Helical gears are commonly used in automotive transmissions for their quiet operation, efficiency, and smooth gear shifting.
- Industrial Machinery: Helical gears find applications in various industrial machinery, such as gearboxes, pumps, compressors, and conveyors, where precise power transmission is essential.
- Robotics: Helical gears play a vital role in robotic systems, offering precision motion control and reducing backlash for accurate movements.
- Aerospace: In the aerospace industry, helical gears are used in various applications, including aircraft landing gear systems and actuation mechanisms.
Precision engineering with helical gears involves a careful balance between design considerations, manufacturing techniques, and application-specific requirements to deliver reliable, efficient, and high-performance gear systems. These precision-engineered helical gears contribute significantly to various industries, enhancing the overall efficiency and reliability of mechanical systems.