Worm gears, spur gears, and helical gears are all types of gears used in mechanical systems for power transmission and motion control. Each gear type has its own unique characteristics, advantages, and applications. Here are the key differences between these three types of gears:
Worm Gears
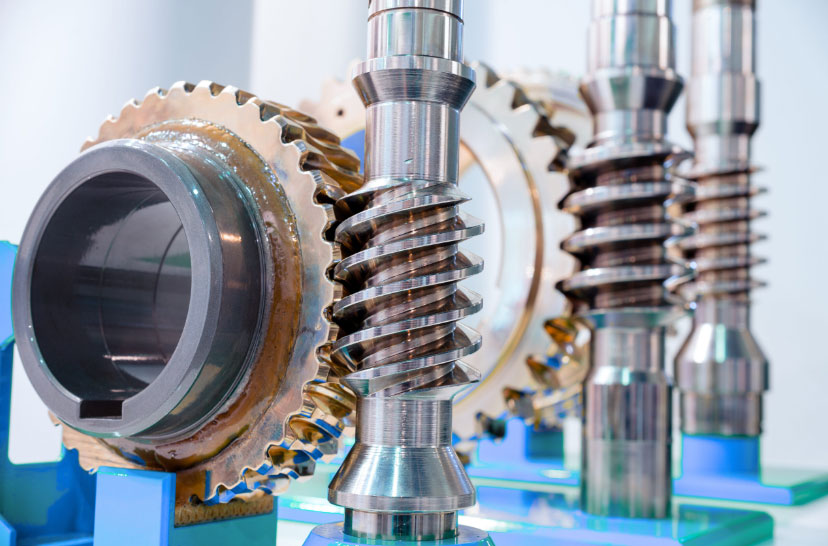
Worm gears are used in large gear reductions. Gear ratio ranges of 5:1 to 300:1 are typical. The setup is designed so that the worm can turn the gear, but the gear cannot turn the worm. The angle of the worm is shallow and as a result the gear is held in place due to the friction between the two. The gear is found in applications such as conveyor systems in which the locking feature can act as a brake or an emergency stop.
- Spur gears are cylindrical gears with straight teeth that are parallel to the gear axis.
- They are the most straightforward and most commonly used type of gears.
- Spur gears are ideal for transmitting power between parallel shafts.
- They offer high efficiency and are relatively easy to manufacture.
- However, they can generate more noise and vibration due to the sudden engagement of teeth during meshing.
Spur Gears
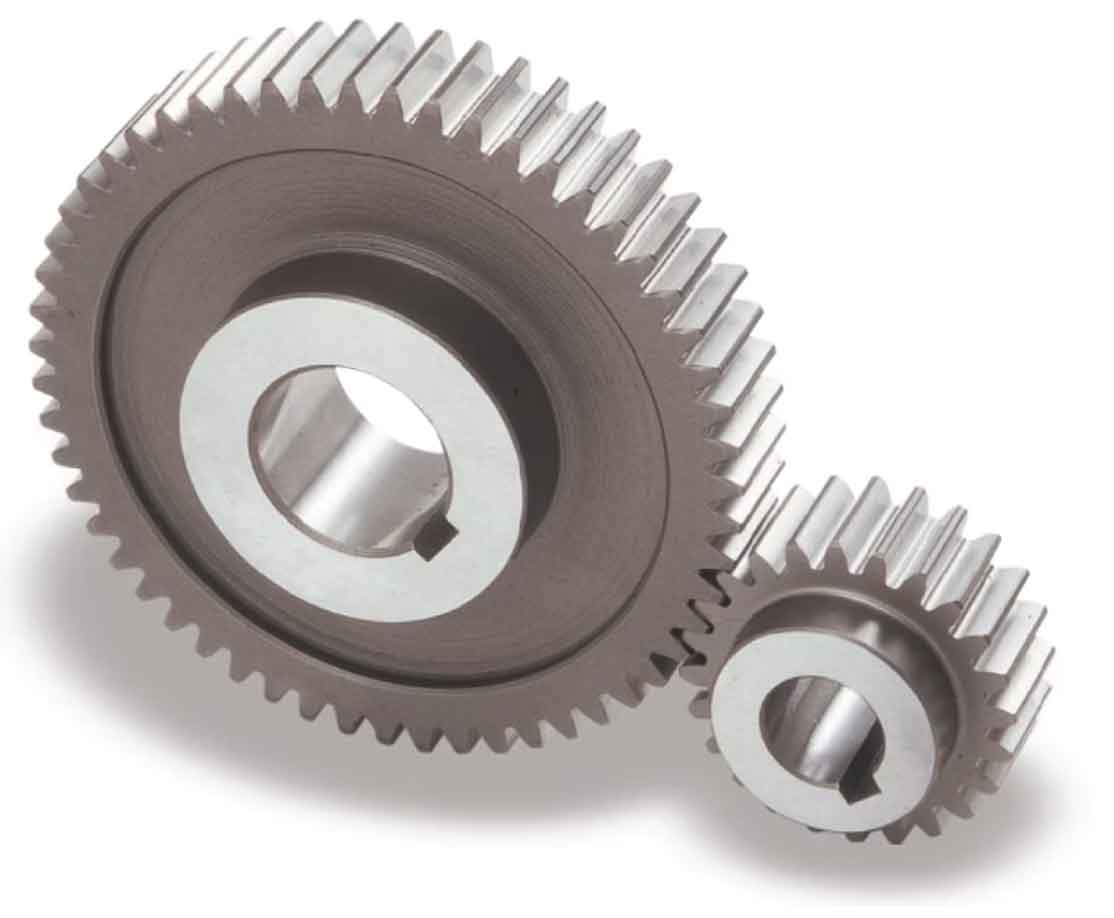
The most common gears are spur gears and are used in series for large gear reductions. The teeth on spur gears are straight and are mounted in parallel on different shafts. Spur gears are used in washing machines, screwdrivers, windup alarm clocks, and other devices. These are particularly loud, due to the gear tooth engaging and colliding. Each impact makes loud noises and causes vibration, which is why spur gears are not used in machinery like cars. A normal gear ratio range is 1:1 to 6:1.
- Helical gears have helical teeth that are cut at an angle to the gear axis in a helix pattern.
- The helical tooth design allows for gradual tooth engagement, resulting in smoother and quieter operation compared to spur gears.
- Helical gears have higher load-carrying capacity and efficiency, making them suitable for higher-speed and heavy-duty applications.
- They are commonly used in parallel shaft configurations, but they can also transmit power between non-parallel and non-intersecting shafts.
Helical Gears
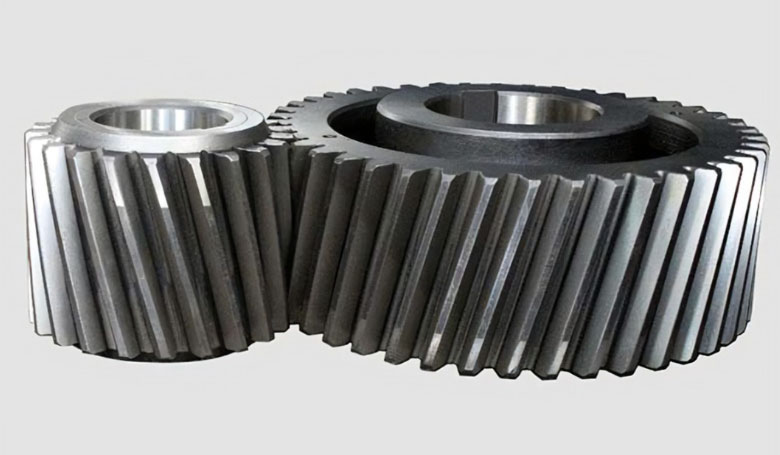
Helical gears operate more smoothly and quietly compared to spur gears due to the way the teeth interact. The teeth on a helical gear cut at an angle to the face of the gear. When two of the teeth start to engage, the contact is gradual–starting at one end of the tooth and maintaining contact as the gear rotates into full engagement. The typical range of the helix angle is about 15 to 30 deg. The thrust load varies directly with the magnitude of tangent of helix angle. Helical is the most commonly used gear in transmissions. They also generate large amounts of thrust and use bearings to help support the thrust load. Helical gears can be used to adjust the rotation angle by 90 deg. when mounted on perpendicular shafts. Its normal gear ratio range is 3:2 to 10:1.
- Worm gears consist of a helical gear (called the worm) and a meshing gear with screw-like teeth (called the worm wheel).
- The worm gear typically has only one or a few teeth, while the worm wheel has multiple teeth.
- Worm gears are used to transmit motion between shafts at a right angle and are especially useful for large speed reduction ratios.
- They offer significant mechanical advantage but are less efficient due to sliding action between the worm and worm wheel.
- Worm gears are commonly used in applications where self-locking is required, preventing back-driving of the system.
Summary:
- Spur gears are simple, commonly used, and efficient gears ideal for parallel shafts.
- Helical gears offer smoother operation, higher load-carrying capacity, and are suitable for both parallel and non-parallel shafts.
- Worm gears provide large speed reduction ratios and are useful for right-angle shaft configurations, but they have lower efficiency.
The choice of gear type depends on the specific requirements of the application, such as speed, load, space limitations, noise considerations, and efficiency. Engineers carefully select the appropriate gear type based on these factors to ensure optimal performance and reliability in mechanical systems.