The physical model and simplified torsional vibration model of the rigidly supported double-input-single-output helical gear system are shown in the figure without considering the influence of the rotating shaft and bearing in motion. The system consists of two power input helical gears (p, q), one power output helical gear (g) and one inertia flywheel, wherein the shaft 1 is a high load input shaft and the shaft 3 is a low load input shaft. Each helical gear is described by its base circle radius (rbp, rbg and rbq).
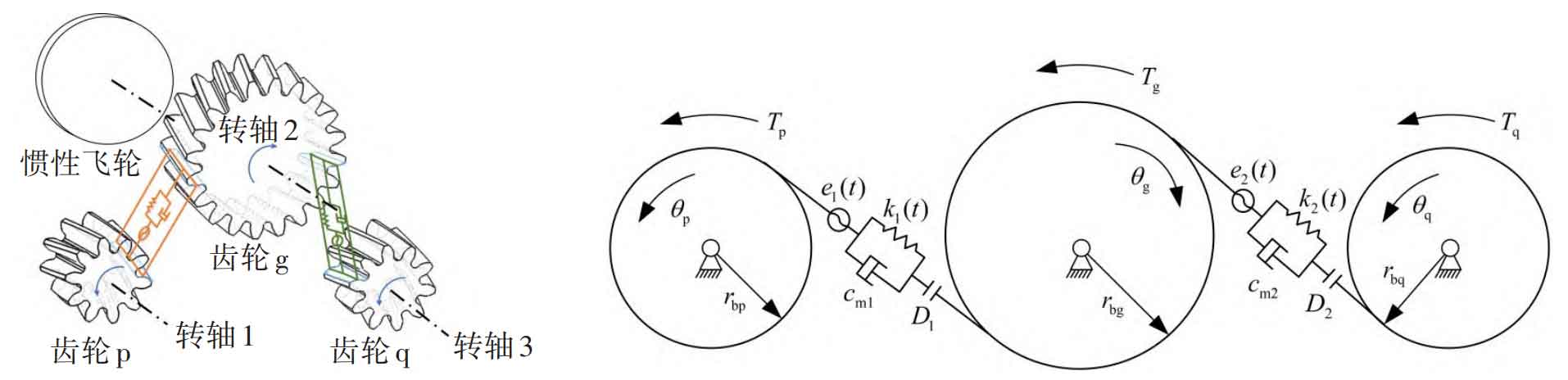
In the system, Tp, Tg and Tq are the moments acting on each helical gear, θ p、 θ G and θ Q is the dynamic angular displacement of each helical gear, Jp and Jq are the rotational inertia of the two driving helical gears, Jf is the equivalent rotational inertia of the big gear and the flywheel on the output shaft, er (t() r=1,2) is the time-varying comprehensive transmission error of the two pairs of helical gears along the meshing line, cm (r r=1,2) is the average meshing damping of the two pairs of helical gears, kr (t() r=1,2) is the time-varying meshing stiffness of the two pairs of helical gears, D (r r=1,2) is half of the tooth side clearance of two pairs of helical gear pairs, β B is the base circle helix angle.
According to Newton’s second law of motion, the pure torsional dynamic equation of the double-input-single-output helical gear system is established:
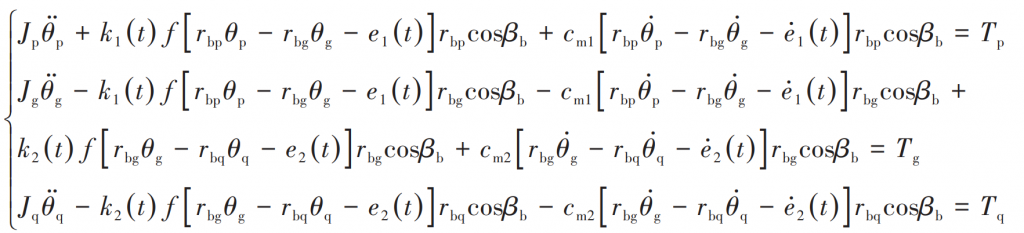