Fretting refers to the micro relative motion of the closely matched contact surface in the mechanical parts under the action of mechanical vibration and other alternating loads, which produces the amplitude of micrometer magnitude [6-8]. [6-8]. Fretting damage includes fretting wear, fretting fatigue and fretting corrosion. Fretting wear refers to the wear on the contact surface caused by the small relative movement of the contact pair under the local contact load or fixed force caused by the external vibration. Fretting fatigue refers to the fatigue damage caused by the small deformation of the contact pair caused by the external alternating load. Fretting corrosion refers to the tiny relative vibration of the contact pairs in the electrolyte or corrosive environment.
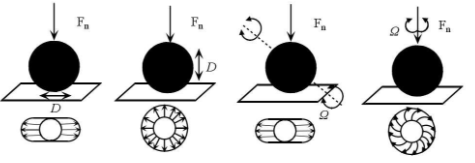
In engineering practice, the fretting phenomenon on the contact surface of two objects has a very complex form of fretting operation. In order to facilitate scientific research, the fretting operation mode of objects is usually simplified as ball / plane contact mode. According to the different relative operation directions between the contact surfaces of two objects, it can be divided into four basic fretting wear modes: tangential fretting wear, radial fretting wear, rotational fretting wear and torsional fretting wear, as shown in the figure:
In the figure, FN represents the normal pressure on the contact object, D represents the displacement amplitude of the object under the action of tangential and radial fretting wear, and Ω represents the torsional angular amplitude of the object under the action of rotational and torsional fretting wear. Fretting wear is a complex process which is affected by the fatigue deformation, friction temperature, contact stress and chemical medium on the contact surface of the object. Due to the fretting wear, the contact surface layer of the object will produce mechanical properties, metallographic structure and other changes, which makes the fretting wear mechanism very complex under the interaction of various factors. Because of the limitation of the theory and scientific research conditions at that time, people formed different fretting wear theories according to different fretting phenomena.
Since the 1920s, people began to find the phenomenon of fretting and began to study it preliminarily. Tomlinson et al think that intermolecular attraction is the main cause of fretting wear, that is, the material on the contact surface of the object reaches the critical value of intermolecular force under the action of normal force and reciprocating relative motion and falls off. Godfrey et al. Found that the wear particles between the contact surfaces of the object are caused by the adhesion and oxidation of the micro convex body, that is, the mechanical action is the main factor in the fretting wear process of the material, and the oxidation is the secondary factor in the damage of the material. Uhlig applied mechanical and chemical principles to fretting wear research, and thought that the combination of mechanical and chemical effects was the main cause of fretting wear. In the process of the relative movement of the micro convex body on the contact surface of the object, the mechanical action is to scrape off the oxide film on the surface so as to present a new contact surface, while the chemical action is that the new contact surface will quickly absorb oxygen in the air and generate chemical reaction to form oxide. The alternation of mechanical and chemical factors in fretting wear results in the loss of metal materials, so the thicker the oxide film is, the greater the wear is. Under other conditions, the thickness of oxide film is proportional to the exposure time of fresh metal. This method is the first to use the quantitative expression of fretting wear theory, but it analyzes the mechanical and chemical effects separately, and considers that the oxidation reaction is a completely harmful effect, which can not be completely consistent with the actual situation.
On the basis of the traditional friction and wear theory, Feng and rightmire divide the fretting wear process into four stages:
(1) The adhesion of the micro convex makes the material transfer between the contact surfaces;
(2) After oxidation reaction and crushing, the exfoliated abrasive particles form oxide debris layer between the contact surfaces;
(3) The work hardening effect of the object contact surface will lead to the decrease of wear rate;
(4) In the stable wear stage, the rate of debris generation is basically the same, and the relationship between debris generation and spillage keeps a dynamic balance.
Wright et al. Once thought that the particles in fretting wear process have abrasive wear characteristics after falling off and oxidation, and the surface damage is caused by fatigue. Halliday and hurricks think that the particle shedding is caused by the rupture of oxide film, and the contact plastic deformation causes the fatigue fracture of the local adhesion point on the metal surface; and they think that the existence of wear debris prevents the direct contact of the metal, plays a role similar to the ball or roller, thus reducing the wear rate of the metal. Based on the theory of delamination under the condition of large displacement sliding wear, some scholars applied it to fretting wear, and thought that the delamination of particles is closely related to the initiation and propagation of subsurface cracks. The delamination theory explained the formation of debris particles under the condition of fretting.
In the 1970s, hurricks, aldham and Waterhouse proposed the following theory: when fretting wear occurs between two planes or two curved cylinders, the fretting wear process can be divided into three parts with the increase of time (or number of cycles) There are three stages: (1) in the initial stage, the contact surface of the object forms a local cold welding point, which makes the contact surface become more rough, and then causes more serious wear effect; fretting fatigue caused by alternating stress will cause fatigue cracks on the contact surface in this stage. (2) In the oxidation reaction stage, the abrasive particles generated in the initial stage undergo oxidation reaction to form a dense oxide layer, which causes the friction coefficient of the contact surface to decrease and makes the fretting show unstable characteristics; (3) in the steady-state action stage, the friction coefficient of the contact surface tends to a state of high and low, which makes the fretting basically show stable characteristics.
To sum up, many theories about fretting wear mechanism, especially the early ones, are obviously inadequate. These viewpoints can not explain the relationship between fatigue crack and fretting wear, and some even come to contradictory viewpoints, which is related to the cognitive level and the limitations of experimental conditions at that time.