Under steady-state conditions, the engine speed range of heavy-duty vehicles studied ranges from 1000 r/min to 4200 r/min.Under full throttle condition, the variation of engine torque is close to constant with the change of engine speed, and the change trend of dynamic load coefficient with engine speed is shown as shown in the figure, in which the interval between values of engine speed is 50r/min.It can be seen from the diagram that there are three distinct peaks in the dynamic load coefficient, corresponding to the rotational speeds of 1050r/min, 2100r/min and 2600r/min, respectively, with the dynamic load coefficient of 2.95, 2.84 and 2.68.Combining the natural frequency of derived linear system (ignoring all non-linear factors), it can be seen that at 1050 r/min speed, the double engagement frequency of gear 1260Hz is close to the first natural frequency of the system 1200Hz, and the system resonates; at 2100 r/min speed, the engagement frequency of gear 1260Hz is close to the first natural frequency 1200Hz of the system, and the system resonates; at 2600 r/min speed,The engagement frequency of gears is 1560Hz, which is close to the second natural frequency of the system, 1490Hz, and the system resonates.The above analysis shows that with the change of engine speed, the system resonates when the meshing frequency and its frequency multiplication approach any natural frequency, resulting in a significant increase in dynamic load.
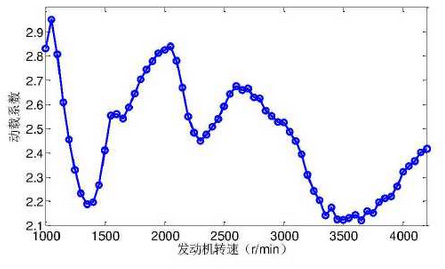
The time-varying characteristics of meshing parameters during gear transmission at rated speed are further analyzed.The time-domain curves of center distance, engagement angle, backlash and overlap are given.Due to the coupling effect between gear engagement parameters and vibration response, the center distance, engagement angle, overlap degree and engagement angle all change with time during actual gear transmission, in which, the center distance of gear fluctuates upward and downward, which is greater than the theoretical center distance; the engagement angle fluctuates upward and downward in degrees, which is greater than the theoretical engagement angle; the clearance fluctuates upward and downward, which is greater than the theoretical clearance; the overlap degree of gear is greater than the theoretical clearanceFluctuate up and down less than gear design coincidence.It can be seen from the variation trend of each meshing parameter with time that as the center distance increases, the meshing angle and tooth side clearance also increase and the coincidence degree gradually decreases.
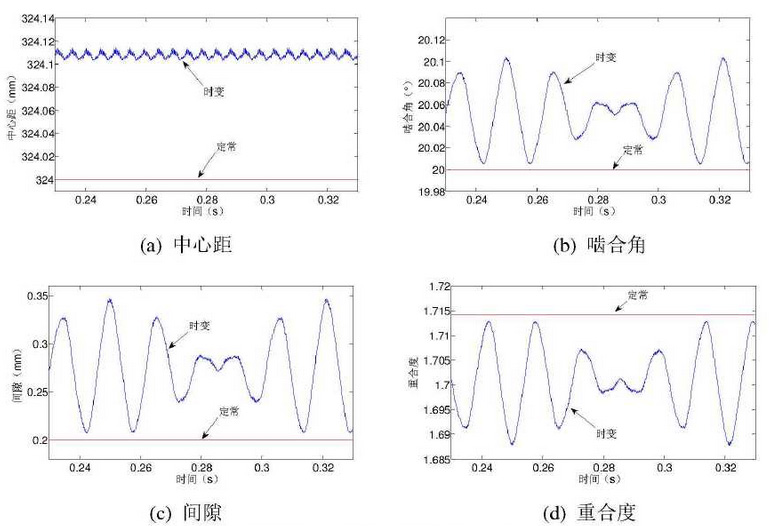
The diagram shows the time-domain and frequency-domain curves of engagement stiffness at rated speed, and gives the time-domain and frequency-domain curves of engagement stiffness under quasi-static conditions (constant speed and theoretical center distance).It can be seen from the diagram that, compared with the quasi-static engagement stiffness, the dynamic engagement stiffness decreases in the single and double teeth engagement area due to the increase of center distance, and at the same time, there is phase difference between the two on the time axis due to the change of gear speed.It can be seen from the spectrum that the dynamic engagement stiffness and the quasi-static engagement stiffness have obvious differences in the corresponding amplitudes on the engagement frequency and its second frequency.Further magnify the spectrum as shown in the figure. The frequency components of the dynamic engagement stiffness also include the frequency sum of each axis.
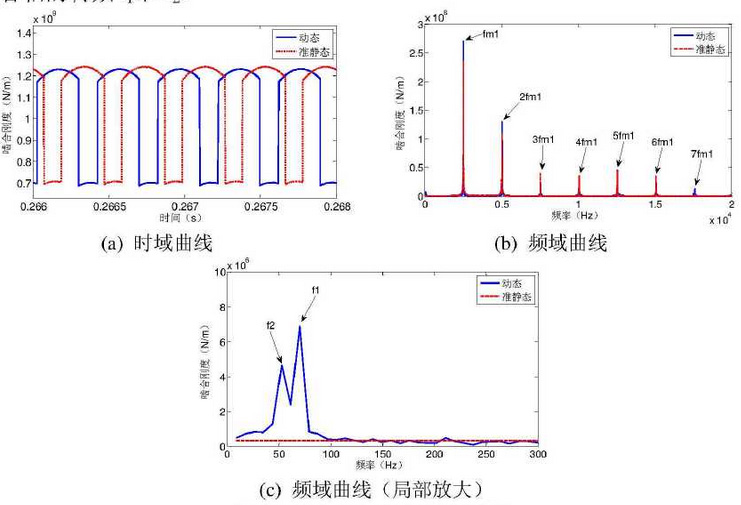