According to the theory of elastohydrodynamic lubrication, the lubricant entering into the crack will form a certain pressure inside the crack to force the crack to expand forward, which is equal to the elastohydrodynamic lubrication pressure at the crack entrance.
Under the Hertz pressure distribution, some studies have shown that the mode I and mode II stress intensity factors Ki and Kii tend to have maximum values when the crack just enters the contact zone, that is, the crack is most likely to expand under this kind of contact load. Therefore, based on the above contact pair model, the elastohydrodynamic lubrication pressure distribution is used to simulate the crack propagation in the entrance region and Hertz contact region. In order to study the influence of different load distribution on the crack, seven different working conditions as shown in Figure 1 are established for calculation.
The results show that in each crack propagation process, compared with other conditions, Ki in condition IV is the maximum, and Kii is close to the maximum σ It’s the biggest. When the crack length a = 28 μ M, the equivalent stress intensity factor k at this time σ> KIC, the crack will extend directly to the tooth surface along the last propagation angle to form micro pitting. It can be seen that crack propagation is more likely to occur under condition IV load. Therefore, the subsequent crack growth studies are carried out under the load distribution of condition IV in Fig. 1.
In addition, as shown in Fig. 2, when the Hertz pressure distribution is used, the maximum K is 0 σ K corresponding to condition IV σ Compare the results. It can be seen that the crack tip K is calculated by Hertz pressure distribution and elastohydrodynamic lubrication pressure distribution σ Especially when the crack propagates rapidly to the tooth surface (a = 26,28) μ m) The difference between them is very obvious. According to Paris formula, the difference shows that the EHL condition delays the crack growth rate of the tooth surface to a certain extent, and the pressure distribution between the contact tooth surfaces is usually in accordance with the EHL pressure distribution when the gear is running under the actual lubrication conditions. Therefore, the elastohydrodynamic lubrication pressure distribution of the contact pair model is more suitable for simulating micro pitting corrosion.
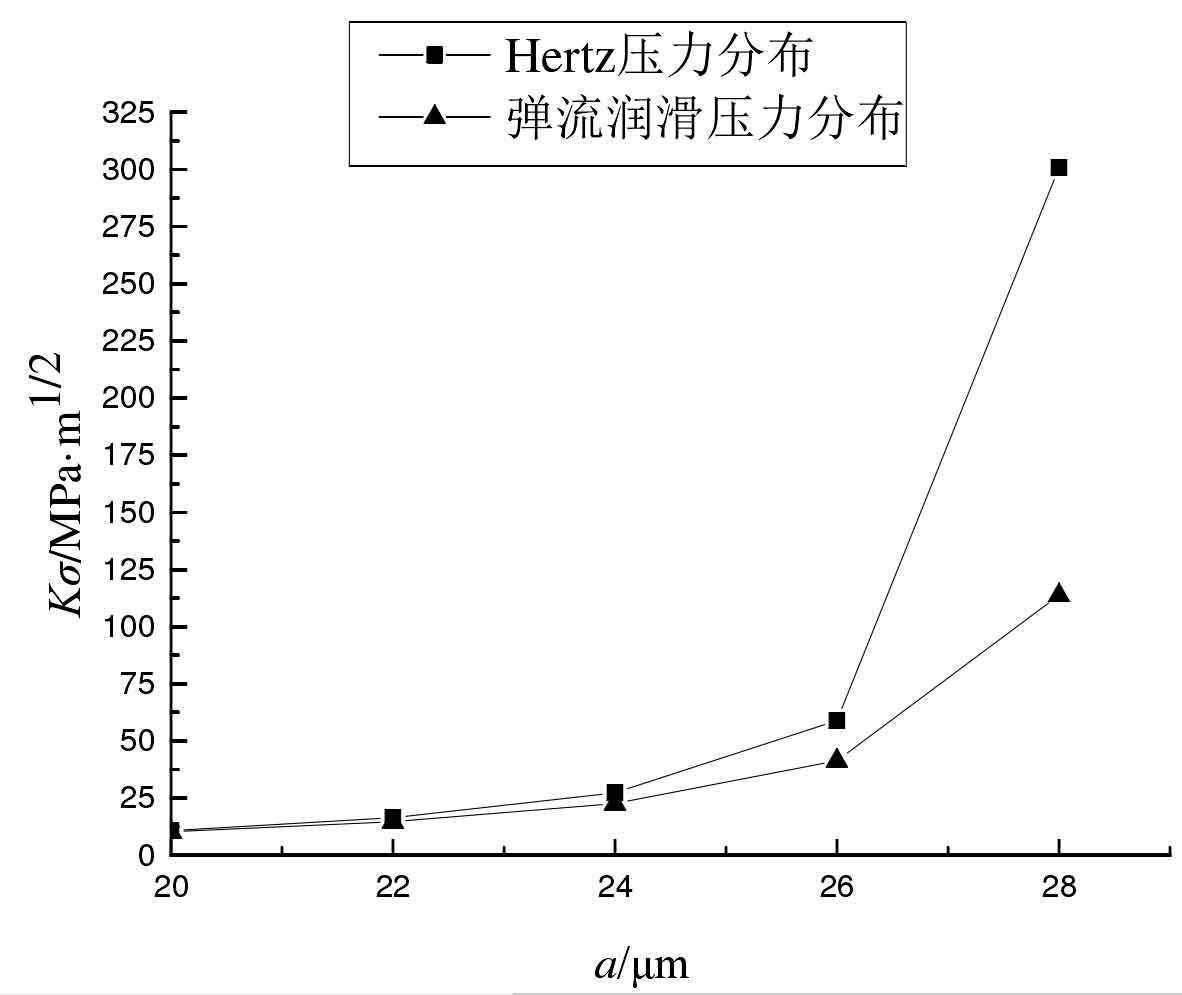