For the statistical analysis of this section, the relevant data of stress ratio r = 0.6 is also used.
The formula is obtained by multiplying both sides of Paris formula by Da and integrating
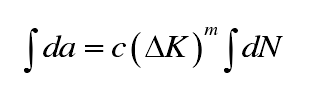
The relationship between the crack length and the number of cycles is obtained by combining the formula
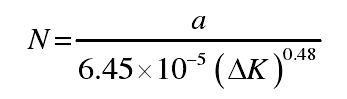
The simulation results of different crack lengths and the stress intensity factors at the crack tip under different crack lengths are substituted into the formula to obtain the corresponding number of cycles n. The number of cycles n obtained from the test and N obtained from the calculation are drawn into a histogram. The relationship between the two groups of data is shown in the figure.
It can be seen from the figure that under the same crack length, the number of cycles obtained from the test is always higher than the theoretical value obtained from the simulation calculation, but there is no significant difference between them. That is to say, when the crack in the sample is extended to the same length, the numerical simulation method is always used to get a relatively small number of cycles. When the crack in the sample is extended to the critical size and fatigue damage occurs, but in fact the crack in the sample has not reached the critical size and fatigue life. This shows that the method of numerical simulation is reliable and accurate in estimating the fatigue life of the specimen.
ABAQUS software was used to simulate the fatigue crack growth of standard compact tensile specimens. The results show that the Mises equivalent stress nephogram of the crack tip in the numerical simulation state is consistent with the theory, and it is approximately symmetrical on both sides of the crack tip with obvious gradient; Under the condition of the same crack length, the smaller stress is larger than the equivalent stress cloud area at the crack tip. With the increase of the crack length, the area increases. Because the numerical simulation is carried out under ideal conditions, the test material is uniform, continuous and isotropic, and the load is applied smoothly, compared with the test results, the stress intensity factor at the crack tip under the same stress ratio and crack length obtained by numerical simulation is always smaller, and the calculated fatigue life is shorter, but the error is smaller, which is within the acceptable range, It can prove the reliability and accuracy of the numerical simulation method and the feasibility of the test, and lay the foundation for the gear bending fatigue test in the next chapter.