Helical gears offer several advantages, especially concerning efficiency and noise reduction, making them a popular choice in various applications. Let’s explore these advantages in detail:
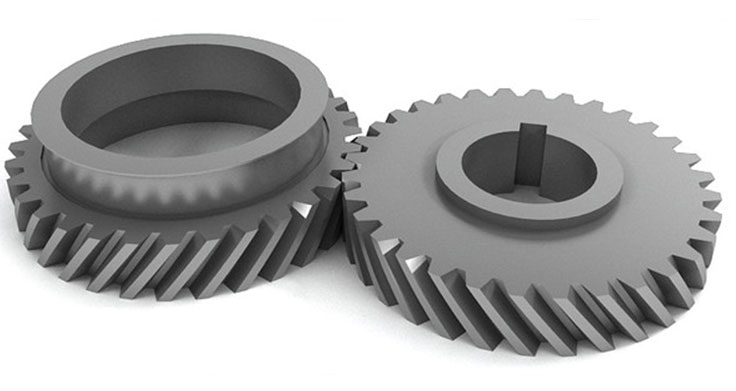
1. Efficiency:
- Gradual Tooth Engagement: The helical tooth design allows for a gradual and continuous tooth engagement, reducing impact and friction during meshing. This results in higher gear efficiency compared to other gear types, such as straight-cut gears. The smoother meshing action minimizes power losses and improves overall transmission efficiency.
2. Load Distribution:
- Multiple Teeth in Contact: Due to the helix angle, helical gears have multiple teeth in contact at any given time. This distributed load-sharing characteristic allows for better load distribution across the tooth surface. The increased contact area reduces stress concentrations and enables helical gears to handle higher torque and loads efficiently.
3. Noise Reduction:
- Smooth Tooth Engagement: The gradual meshing of helical gears reduces gear noise significantly. Compared to gears with abrupt meshing, like straight-cut gears, helical gears produce lower noise levels due to the smoother engagement of the helical teeth. The reduced noise makes helical gears ideal for applications where quiet operation is critical.
4. Vibration Damping:
- Helix Angle Effect: The helix angle in helical gears provides a beneficial effect in damping vibrations during operation. This damping effect helps reduce gear and system vibrations, leading to a more stable and comfortable operation in various applications.
5. Parallel Shaft Configuration:
- Suitable for Parallel Shaft Layout: Helical gears are designed to work efficiently in parallel shaft configurations. They are widely used in applications where power transmission is required between two parallel shafts. This versatility makes them common in gearboxes and industrial machinery.
6. High Gear Ratios:
- Helical gears can achieve higher gear ratios compared to some other gear types. This flexibility allows for finer adjustments in gear ratios, enabling more precise control over speed and torque transmission.
7. Strength and Durability:
- The helical tooth design contributes to the strength and durability of helical gears. The gradual tooth engagement, load distribution, and high-quality materials used in their construction make them robust components capable of withstanding heavy loads and demanding operating conditions.
8. Versatility:
- Helical gears find applications in various industries, including automotive, aerospace, marine, industrial machinery, and robotics. Their ability to offer high efficiency, noise reduction, and reliability makes them suitable for a wide range of applications.
In summary, helical gears provide significant advantages in terms of efficiency and noise reduction compared to other gear types. Their smooth tooth engagement, load distribution capabilities, and damping effect on vibrations result in quieter operation, increased energy efficiency, and improved gear life. These advantages make helical gears a preferred choice in critical applications where precision, reliability, and quiet operation are essential.