Spiral bevel gears offer several advantages, including high efficiency and noise reduction, making them a popular choice for various applications. Let’s explore how these gears unlock the advantages of efficiency and noise reduction:
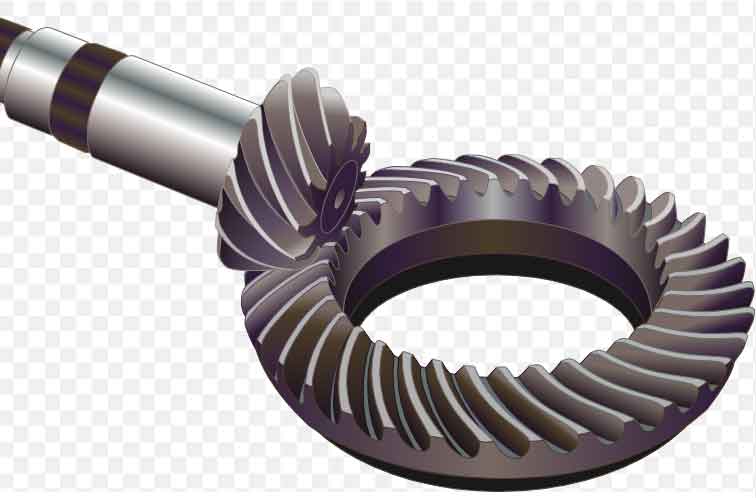
1. Efficiency:
Smooth Tooth Engagement:
- Spiral bevel gears have helical teeth that engage gradually, leading to a smooth transfer of power between shafts. This gradual meshing action reduces impact and sliding friction during gear engagement, resulting in higher gear efficiency compared to straight bevel gears.
Improved Load Distribution:
- The helical tooth design allows for multiple teeth to be in contact at any given time. This improved contact ratio distributes the load over a larger surface area, reducing tooth stresses and wear, and enhancing the gear’s load-carrying capacity.
Reduced Friction:
- The helical teeth’s continuous contact during meshing results in reduced sliding friction, minimizing energy losses due to frictional forces. This feature contributes to higher overall gear efficiency.
2. Noise Reduction:
Gradual Tooth Engagement:
- The helical teeth of spiral bevel gears engage smoothly and progressively, which reduces impact forces and gear meshing noise. This gradual engagement leads to quieter gear operation compared to straight bevel gears.
Contact Pattern Optimization:
- By carefully designing the tooth profiles and gear microgeometry, engineers can optimize the gear’s contact pattern, reducing noise and vibration during operation.
Surface Finishing and Coatings:
- Advanced surface finishing techniques and coatings can be applied to the gear teeth to reduce surface roughness and friction, further minimizing noise generation.
Damping Characteristics:
- Spiral bevel gears exhibit self-locking properties due to their helical design, providing some inherent damping capabilities. This dampening effect helps reduce gear vibration and noise.
3. Application of Spiral Bevel Gears:
Automotive Industry:
- Spiral bevel gears are commonly used in automotive differentials and drivetrains, providing smooth power transmission and improved vehicle handling with reduced noise levels.
Aerospace Applications:
- In aerospace, spiral bevel gears are employed in helicopter transmissions, flight control systems, and aircraft engines, where high efficiency and low noise are essential.
Industrial Machinery:
- Spiral bevel gears find application in various industrial machinery, such as gearboxes, machine tools, and heavy-duty equipment, delivering efficient power transmission with reduced noise.
Robotics and Automation:
- Spiral bevel gears are used in robotic systems and automation equipment, enabling precise motion control and quiet operation, making them suitable for collaborative robot applications.
Marine Propulsion:
- They are used in marine propulsion systems, providing reliable power transmission with reduced noise for boats and ships.
Spiral bevel gears offer numerous advantages, including high efficiency and noise reduction, making them a preferred choice for applications where smooth and precise power transmission, minimal energy losses, and quiet operation are essential. The advancements in design, manufacturing techniques, and materials have further improved the efficiency and noise-reducing capabilities of spiral bevel gears, solidifying their importance in a wide range of industries, including automotive, aerospace, robotics, and industrial machinery.