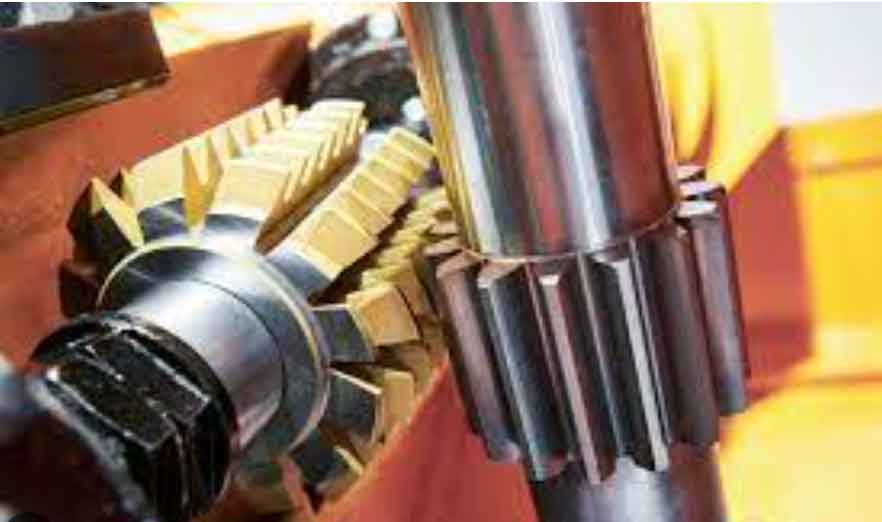
Gear hobbing, a machining process for producing gears, has been a fundamental technique in the manufacturing industry for many years. While the basic principles of gear hobbing remain the same, there have been significant innovations that are shaping the future of gear manufacturing. These advancements primarily focus on improving efficiency, accuracy, versatility, and automation in gear hobbing processes. Here are some notable innovations:
- Multi-Axis CNC Gear Hobbing Machines: Traditional gear hobbing machines were limited to single-axis movement, requiring multiple setups and tool changes to produce complex gear profiles. Modern gear hobbing machines utilize computer numerical control (CNC) technology with multiple axes, enabling simultaneous movement of the cutting tool and workpiece. This advancement allows for the production of highly complex gear profiles in a single setup, significantly reducing production time and increasing accuracy.
- High-Speed Gear Hobbing: High-speed gear hobbing has emerged as a game-changer in gear manufacturing. By increasing the rotational speed of the hobbing tool, manufacturers can achieve higher cutting speeds, resulting in reduced cycle times and improved productivity. Additionally, high-speed gear hobbing allows for the use of smaller hob cutters, reducing material waste and tooling costs.
- Dry Hobbing: Traditionally, gear hobbing involved the use of cutting fluids or lubricants to cool the cutting tool and remove chips. However, dry hobbing has gained popularity due to environmental concerns, cost savings, and improved part cleanliness. Dry hobbing utilizes advanced tool coatings, such as diamond-like carbon (DLC), to minimize friction and heat generation during the cutting process. This innovation eliminates the need for cutting fluids while maintaining tool life and improving gear surface quality.
- Adaptive Gear Hobbing: Adaptive gear hobbing employs advanced sensing and control systems to dynamically adjust the cutting parameters during the hobbing process. By monitoring factors like cutting forces, temperature, and gear quality, the system can make real-time adjustments to optimize the machining process. Adaptive gear hobbing ensures consistent gear quality, reduces tool wear, and enhances overall process efficiency.
- Gear Hobbing with Robotics and Automation: The integration of robotics and automation has revolutionized gear hobbing by enhancing productivity and reducing human intervention. Automated systems can handle the loading and unloading of workpieces, tool changes, and inspection processes. Additionally, robotic systems equipped with advanced vision systems can perform in-process measurements and make adjustments, ensuring accurate and reliable gear production.
- Simulation and Virtual Gear Hobbing: Computer-aided simulation and virtual gear hobbing tools have become invaluable in the design and optimization of gear manufacturing processes. These tools allow manufacturers to visualize and analyze the entire hobbing process before physical implementation. By simulating various cutting parameters, tool designs, and material properties, manufacturers can identify potential issues, optimize process parameters, and reduce costly trial-and-error iterations.
These gear hobbing innovations collectively contribute to increased productivity, improved gear quality, reduced lead times, and enhanced flexibility in gear manufacturing. As technology continues to advance, gear hobbing processes will likely become more efficient, precise, and automated, enabling the production of high-quality gears for a wide range of applications.