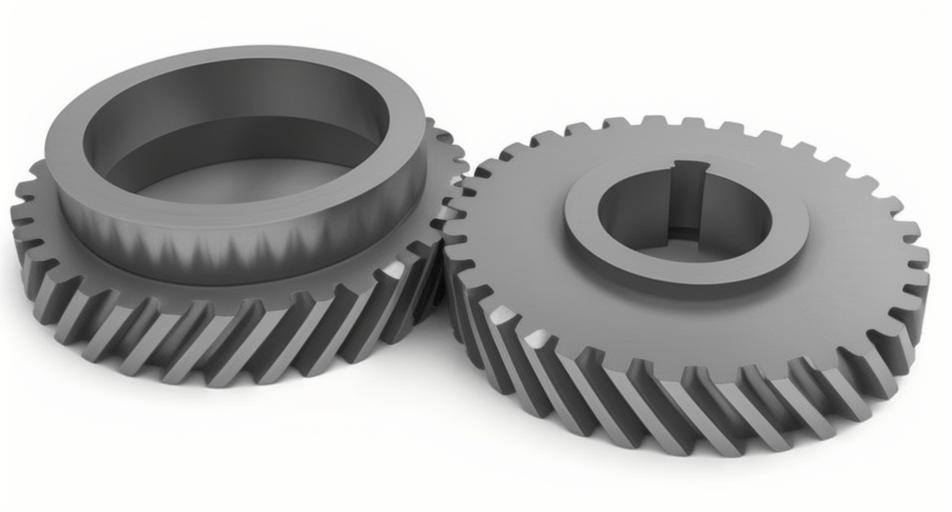
Helical gear is widely used in industrial applications due to their ability to handle high loads and provide smooth and quiet operation. However, with the increasing emphasis on energy efficiency and sustainability, there is a growing need to optimize the performance of these gear mechanisms. This article explores various strategies and innovations aimed at enhancing the energy efficiency of helical gear in industrial settings.
Understanding Helical Gear
Helical gear has teeth that are cut at an angle to the gear axis. This helical angle allows for gradual engagement of helical gear teeth, resulting in smoother and quieter operation compared to spur gear. The helical design also enables the transmission of higher loads, making these helical gear ideal for heavy-duty applications.
Factors Affecting Energy Efficiency
Several factors influence the energy efficiency of helical gear mechanisms, including:
- Material Selection: The choice of materials plays a critical role in determining the efficiency of helical gear. Advanced materials with superior strength and wear resistance can reduce friction and energy losses.
- Lubrication: Proper lubrication minimizes friction between helical gear teeth, thereby reducing energy consumption and wear.
- Surface Coatings: Innovative surface coatings can enhance the durability and performance of helical gear, leading to improved energy efficiency.
- Gear Design: Optimizing the design of helical gear, such as the helix angle, tooth profile, and helical gear geometry, can significantly impact their efficiency.
- Manufacturing Precision: High-precision manufacturing processes ensure better helical gear alignment and meshing, reducing energy losses due to misalignment and surface roughness.
Innovations in Helical Gear Mechanisms
- Advanced Materials: The development of new materials, such as high-strength alloys and composites, has led to significant improvements in the performance and efficiency of helical gear. These materials offer better wear resistance and lower friction, resulting in reduced energy consumption.
- Nano-Coatings: The application of nano-coatings on helical gear surfaces can dramatically reduce friction and wear, leading to enhanced energy efficiency. These coatings also provide superior resistance to corrosion and other environmental factors.
- Lubrication Technology: Advanced lubrication technologies, including synthetic lubricants and solid lubricants, have been developed to improve the efficiency and lifespan of helical gear. These lubricants offer better thermal stability and lower friction coefficients.
- Additive Manufacturing: The use of additive manufacturing techniques allows for the production of complex gear geometries with high precision. This technology enables the creation of optimized gear designs that enhance energy efficiency.
- Smart Monitoring Systems: The integration of smart monitoring systems with helical gear mechanisms provides real-time data on gear performance and wear. This information can be used to optimize maintenance schedules and improve overall efficiency.
Table: Comparison of Energy Efficiency Improvement Strategies
Strategy | Description | Benefits |
---|---|---|
Advanced Materials | Use of high-strength alloys and composites | Reduced friction, improved wear resistance |
Nano-Coatings | Application of nano-scale coatings on gear surfaces | Lower friction, enhanced durability, corrosion resistance |
Lubrication Technology | Use of synthetic and solid lubricants | Better thermal stability, reduced energy consumption |
Additive Manufacturing | Production of complex gear geometries with high precision | Optimized designs, improved efficiency |
Smart Monitoring Systems | Real-time performance and wear data | Optimized maintenance, improved operational efficiency |
Conclusion
Improving the energy efficiency of helical gear mechanisms is crucial for enhancing the performance and sustainability of industrial applications. By leveraging advanced materials, innovative coatings, and cutting-edge manufacturing technologies, significant improvements in energy efficiency can be achieved. Additionally, the integration of smart monitoring systems ensures optimal performance and maintenance, further contributing to the overall efficiency of helical gear mechanisms. These advancements not only reduce energy consumption but also extend the lifespan of helical gear systems, providing economic and environmental benefits for industrial operations.