The unsung heroes of engineering, worm gears are instrumental in the operation of numerous machinery that we interact with in our daily lives, and in countless industrial applications. As an essential element of power transmission systems, their unique design and remarkable attributes contribute significantly to the functionality of modern machinery. This article aims to shed light on this marvel of engineering and its pivotal role in modern machinery.
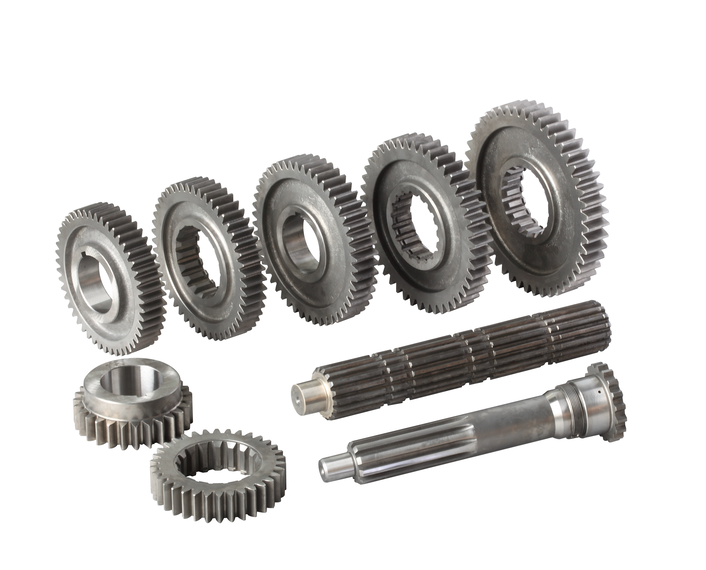
The Design and Operation of Worm Gears
Worm gears comprise two primary components – the worm (which resembles a screw) and the worm gear (a large diameter gear with grooves that accommodate the worm). This configuration ensures that the worm can easily turn the gear but not the other way around, due to the angle of interaction between the worm’s helical threads and the teeth of the worm gear. This self-locking feature plays a critical role in many applications where a system must not be driven backwards.
The gear ratio is calculated by the number of starts on the worm and the number of teeth on the worm gear. Given this characteristic, worm gears are efficient in reducing speed and increasing torque, making them ideal for applications requiring compact, high-torque mechanisms.
Role of Worm Gears in Modern Machinery
The unique design features of worm gears, such as their compact size, high torque output, quiet operation, and self-locking capability, make them ideal for a wide range of applications in modern machinery.
Automotive Industry
In the automotive sector, worm gears are used in steering systems. The worm gear transforms the rotary motion of the steering wheel into the linear motion required to turn the wheels. Their self-locking feature ensures that the wheels can’t force the steering wheel to turn, offering safety and control.
Material Handling Equipment
In material handling equipment such as lifts, conveyors, and hoists, the self-locking property of worm gears is invaluable, preventing the load from dropping or moving unexpectedly. In addition, their high torque transmission capability makes them well-suited for lifting or moving heavy loads.
Manufacturing and Industrial Machinery
In manufacturing plants and other industrial settings, worm gears are commonly found in machines used for grinding, cutting, or milling. The high gear reduction allows these machines to have high torque for cutting hard materials, while their compact size keeps the overall size of the machine manageable.
Renewable Energy Systems
Worm gears have found a niche in renewable energy systems, particularly in wind turbines. They are used to orient the blades and the entire turbine assembly to optimize the capture of wind energy. Their self-locking feature prevents the turbine from spinning out of control in high winds.
Future Prospects
With advancements in material science and manufacturing technologies, the efficiency and load-bearing capacity of worm gears have improved significantly. Modern materials like advanced plastics and alloys are being used to make lighter, stronger, and more durable worm gears.
Furthermore, as we continue to progress towards a more automated and mechanized world, the demand for compact, high-torque transmission systems is likely to grow. As such, worm gears will continue to play a vital role in the machines of the future, underlining their status as a true engineering marvel.
In conclusion, the worm gear’s ability to transform high-speed, low-torque input into low-speed, high-torque output in a compact, self-locking design makes it a critical component of modern machinery. Its contribution to making our machines more efficient, reliable, and safe is a testament to the wonders of engineering.