The main and driven gear materials in the gear temperature measuring test stand are constantan and 40Cr steel respectively.
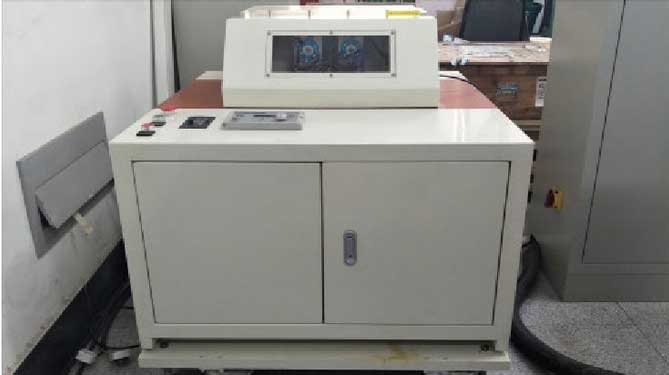
In order to accurately measure the tooth contact temperature under different operating conditions, the test bench shown in Figure 1 was developed.This test bench is a kind of test bench for measuring contact temperature of tooth surface of single-tooth meshing gear. Its active motor is three-phase asynchronous variable frequency motor, and its speed can be adjusted between 1080 and 2 400 r/min, with a wide range of regulation and control.Its driven gear has 3 missing teeth and 3 gears are installed side by side, which ensures that the driving gear and driven gear always engage with one tooth.The test bench is mainly composed of active motor, electric brake device, belt drive, speed sensor, torque sensor and temperature sensor.Figure 2 shows a physical drawing of two meshing gears.The temperature sensor embedded under the tooth surface of the gear can directly measure the temperature at the contact point during gear engagement.
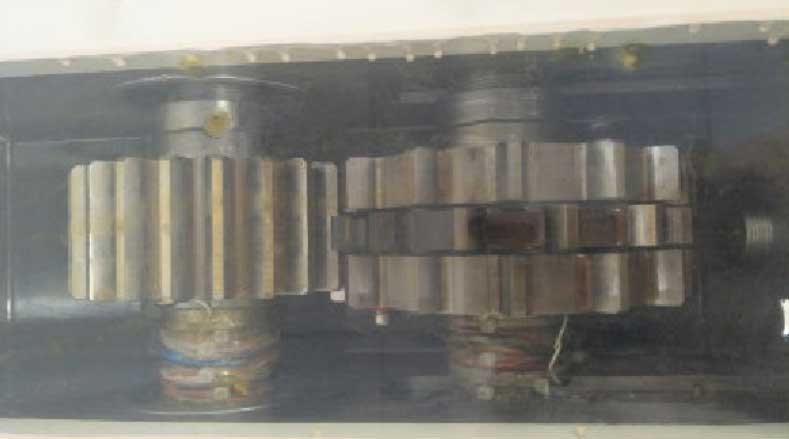
During the measurement, after running for about 0.5 h, the test data of a certain period of time are taken and the tooth contact temperature under the same parameters and operating conditions is calculated by numerical calculation method. The experimental results under different operating conditions are compared with the numerical calculation results, and the comparison results are shown in Figure 3.
It can be seen from Figure 3 that the measured tooth surface contact temperature differs from the numerical calculation results by a certain amount, but the trend is basically the same; however, the experimental values are higher than the numerical calculation values, mainly because the numerical calculation does not consider the influence of bearing heating on the temperature field of the gear body.It can be seen from the experimental curves that the contact temperature of the tooth surface fluctuates slightly near the joint position and then changes smoothly.The reason is that the normal contact pressure of the gear from the double-tooth engagement area to the single-tooth engagement area increases abruptly during the actual engagement process, while the contact stress of the tooth surface from the single-tooth engagement area to the double-tooth engagement area decreases abruptly, which is easy to form the impact of the tooth surface and cause the disturbance of the oil agitation, so that the lubricant can not attach well to the tooth surface, thus causing the fluctuation of the contact temperature on the tooth surface.It is unavoidable.
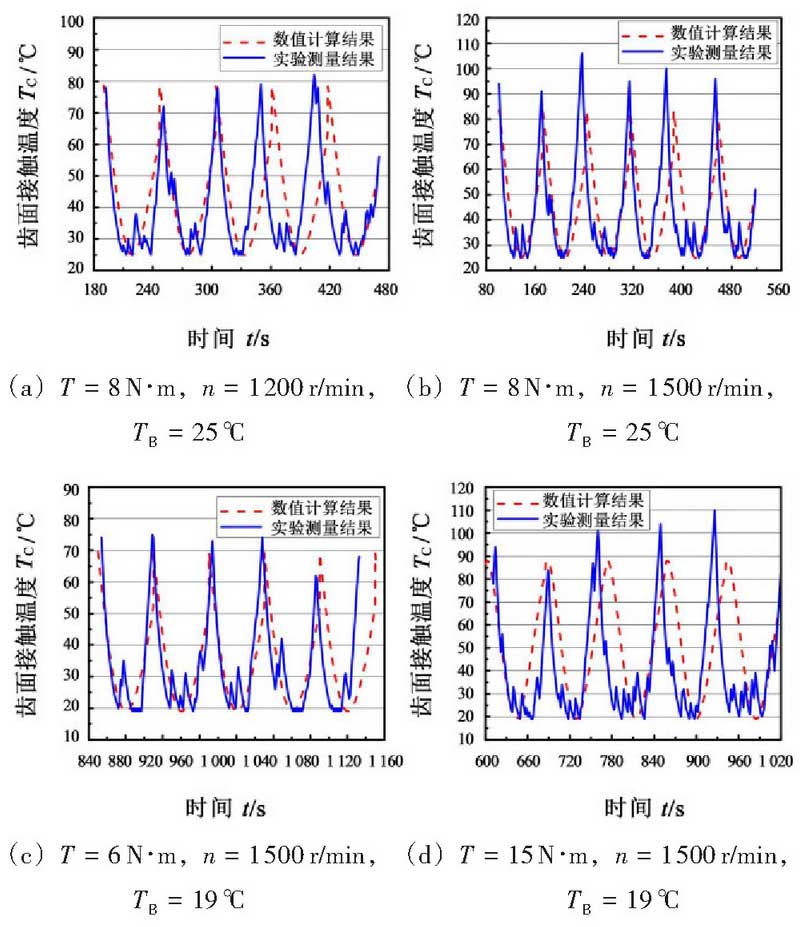
Figures 4(a) – 4(d) show the contact temperature of the tooth surface in one engagement cycle corresponding to Figure 3(a) – 3(d).From Figure 4, it can be seen that in one engagement cycle, the contact temperature of the driven wheel entering the engagement position and the tooth surface near the tooth crown is the highest and the lowest near the joint, approximately equal to the room temperature.The distribution rule of tooth contact temperature on the engagement line is that the contact temperature gradually decreases from the engagement position to the joint, and the tip circle gradually rises to the peak value from the joint to the driven gear.The contact temperature at the top of the driven gear teeth increases greatly when entering the engagement position, and the contact temperature at the top of the driven gear teeth is higher than that at the top of the driven gear teeth.
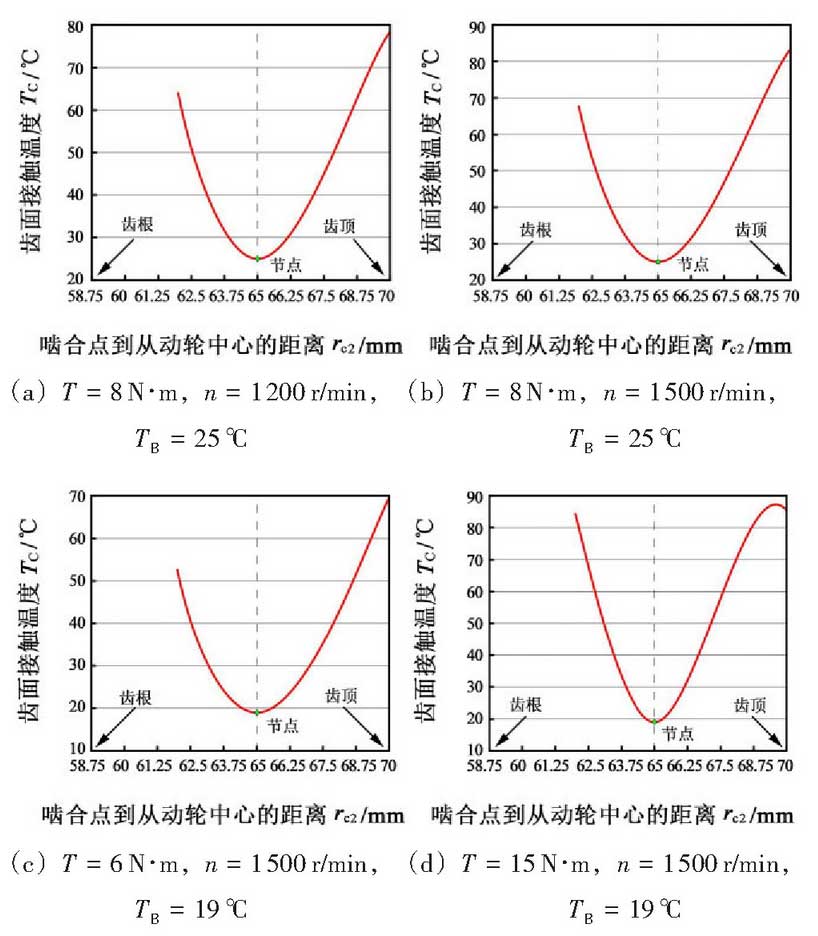
Comparing with Figure 4(a) and Figure 4(b), it can be seen that the tooth contact temperature generated during gear meshing is positively related to the speed. The higher the speed, the higher the tooth contact temperature.Comparing with Figure 4(c) and Figure 4(d), it can be seen that the contact temperature of tooth surface generated by friction increases with the increase of torque, which indicates that the contact temperature of tooth surface is positively correlated with the torque during meshing. The higher the torque, the higher the contact temperature of tooth surface.
The above calculation and experiment results show that the established calculation method of tooth contact temperature agrees well with the experiment results and the basic rule is correct when calculating the change of tooth contact temperature.This method is scientific and effective, and can reflect the temperature change during gear meshing and the influence of system parameters on the contact temperature of tooth surface to a certain extent.