In the field of mechanical engineering, the vibration and noise generated by gear transmission can have a significant impact on the normal operation of transmission equipment, and in severe cases, even cause equipment damage. To address this issue, researchers have been exploring various methods to reduce and isolate the vibration of gear systems. One such method is the use of squeeze film dampers (SFDs) and integral squeeze film dampers (ISFDs), which have shown promising results in vibration control.
This article focuses on the application of a novel G-type Integral Squeeze Film Damper (GISFD) in helical gear systems to reduce vibration. The background and significance of this research lie in the need to improve the performance and reliability of gear transmission systems by reducing vibration and noise. Gear systems are widely used in various industries, such as aerospace, automotive, and manufacturing, and excessive vibration can lead to reduced transmission accuracy, increased wear, and potential safety hazards. Therefore, developing effective vibration reduction methods is crucial for the optimal operation of these systems.
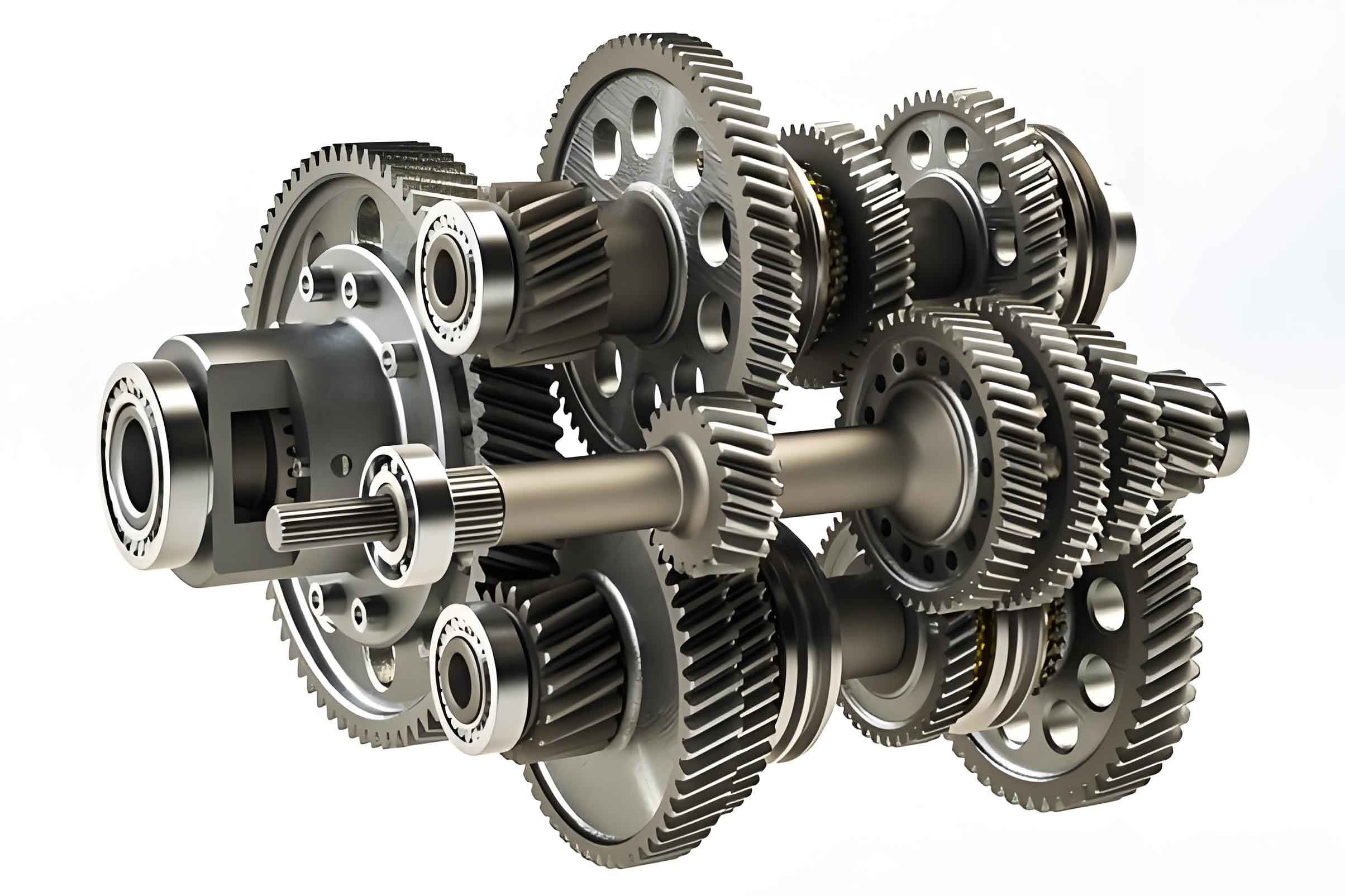
Previous studies in this area have investigated different types of dampers and their effects on gear vibration. For example, some researchers have studied the use of traditional SFDs in rotor systems and found that they can provide damping to reduce vibration, but they may also exhibit nonlinear behavior under certain conditions. ISFDs have been introduced to address some of the limitations of SFDs by using a segmented design to avoid circumferential flow of the oil film and provide more stable damping forces. However, the application of ISFDs in gear systems is still a relatively new area, and further research is needed to explore their effectiveness and potential benefits.
The main content of this research includes the introduction of the GISFD, the analysis of the vibration model of the helical gear system, and the experimental study on the vibration reduction effect of the GISFD on the helical gear shaft system.
- G-Type Integral Squeeze Film Damper (GISFD)
- Introduction: The GISFD is a novel type of damper that consists of an outer ring, a squeeze film area, G-type elastomers, and an inner ring. The inner and outer rings are connected by the G-type elastomers, which divide the squeeze film area into multiple local chambers. When the rotor vibrates, the vibration is transmitted to the inner ring of the GISFD through the bearing, and the inner ring whirls, causing the fluid in the gap of the squeeze film area to be squeezed, generating viscous damping force to dissipate part of the rotor vibration energy and reduce the rotor vibration.
- Structural Features and Advantages: Compared to the traditional ISFD, the GISFD uses a G-type elastomer structure, which occupies less area in the circumferential direction, resulting in a larger squeeze film area and better vibration reduction effect. The segmented design of the squeeze film area avoids the circumferential flow of the oil film, solving the problem of high nonlinearity of the SFD oil film force. The GISFD can provide both elastic support and damping to the rotor system, improving the stability of the system. Additionally, the GISFD is processed by electrical discharge machining, reducing the influence of manufacturing errors. The G-type elastomer structure has fewer structural parameters to consider during the design process, making it simpler to design.
Feature | Details |
---|---|
Components | Consists of an outer ring, a squeeze film area, G-type elastomers, and an inner ring. |
Connection | The inner and outer rings are connected by G-type elastomers. |
Squeeze Film Area | Divided into multiple local chambers by the G-type elastomers. |
Advantages | Larger squeeze film area, better vibration reduction effect, avoids oil film circumferential flow, provides stable damping force, and has a simpler design. |
- Vibration Model and Analysis
- Model Establishment: To analyze the vibration characteristics of the helical gear system, a simplified vibration model is established. The gear is considered as an excitation source, and the excitation is transmitted to the gear box through the bearing. The gear box is treated as a concentrated mass M, and the bearing and GISFD are simplified as a spring element with a certain stiffness K and a damping element with a certain damping C.
- Equation Derivation: Based on the model, the motion equation of the system is derived as Mx¨ + Cx˙ + Kx = F0ejωt, where F0 is the amplitude of the excitation force transmitted to the box, ω is the frequency of the excitation force, and x is the displacement response. The natural frequency of the system is ω0 = K/M, and the frequency ratio is z = ω/ω0. The vibration displacement response is x0 = |F0/K(1/(1 – z² + j2ζz))|, where ζ is the damping ratio of the system, ζ = C/(2KM).
- Vibration Transmission Coefficient: The vibration transmission coefficient Tf is derived as |P0/F0| = |1/K(jωC + K)/((1 – z² + j2ζz))| = √(1 + (2ζz)²)/√((1 – z²)² + (2ζz)²). When Tf < 1, the force transmitted to the base is less than the excitation force of the system. Reducing the stiffness coefficient K and increasing the damping C can reduce the transmission coefficient Tf.
- Analysis of Vibration Isolation Effect: The GISFD has a low stiffness and can provide damping to the gear transmission system, increasing the damping coefficient of the system. Therefore, it can effectively isolate the vibration transmitted to the gear box. However, for low-frequency vibrations, when Tf > 1, the vibration of the system may increase.
Model Aspect | Details | ||
---|---|---|---|
Assumptions | The gear is the excitation source, and the bearing and GISFD are simplified as a spring and damping element. | ||
Equation | Mx¨ + Cx˙ + Kx = F0ejωt | ||
Natural Frequency | ω0 = K/M | ||
Frequency Ratio | z = ω/ω0 | ||
Displacement Response | x0 = | F0/K(1/(1 – z² + j2ζz)) | |
Damping Ratio | ζ = C/(2KM) | ||
Transmission Coefficient | Tf = √(1 + (2ζz)²)/√((1 – z²)² + (2ζz)²) |
- Experiment and Results Analysis
- Test Bench Introduction: An open-type single-stage helical gear test bench is built based on the GISFD to study the influence of the GISFD on the vibration characteristics of the helical gear shaft system at different speeds. The test bench consists of a helical gear transmission system and a data acquisition system. The helical gear transmission system includes a motor, a helical gear pair, supports (GISFD support and rigid support), and the main and driven shafts.
- Experiment on Vibration Response with Different Support Structures: An experiment is conducted to compare the vibration characteristics of the helical gear shaft system under rigid support and GISFD support. The results show that the GISFD support can significantly reduce the vibration peak of the helical gear shaft system, with a maximum vibration reduction of 59.61%. The GISFD also has a good suppression effect on the characteristic frequencies of the helical gear shaft system, with a maximum vibration reduction of 85.71%.
- Experiment on Vibration Suppression of GISFD at Different Speeds: To explore the influence of the GISFD support on the vibration characteristics of the helical gear shaft system at different speeds, an experiment is carried out. The results show that the GISFD support has a good vibration suppression effect on the helical gear shaft system in a wide speed range, with a vibration reduction of up to 69.80%.
- Experiment on Vibration Suppression of GISFD for Worn Helical Gears: An experiment is conducted to study the effect of the GISFD support on the vibration characteristics of worn helical gears. The results show that the GISFD support can effectively suppress the vibration of the worn helical gear shaft system, with a vibration reduction of up to 83.99%.
Experiment Aspect | Details |
---|---|
Test Bench Components | Includes a helical gear transmission system and a data acquisition system. |
Support Structures | Rigid support and GISFD support. |
Vibration Measurement | Uses piezoelectric acceleration sensors to measure the acceleration in the horizontal and vertical directions of the bearing seats at the far end of the motor of the main and driven shafts. |
Results | GISFD support reduces vibration peak, suppresses characteristic frequency vibrations, and has a good effect on worn helical gears. |
The main conclusions of this research are as follows:
- The GISFD support can provide damping to the helical gear transmission system, effectively isolate the vibration transmitted to the bearing seat, and has a good vibration reduction effect in a wide speed range, with a vibration reduction of up to 69.80%.
- The GISFD support has a good vibration reduction effect on the vibration at the gear meshing frequency, with a maximum vibration reduction of 85.71%. It also has a good vibration reduction effect on non-meshing frequency vibrations and can improve the modulation phenomenon of the gear.
- The GISFD can effectively suppress the vibration of the helical gear with tooth surface wear and has a good vibration reduction effect in a wide speed range, with a vibration reduction of up to 83.99%.
However, this research also has some limitations. For example, the experiment only considers the vibration in the horizontal and vertical directions, and the influence of other factors such as temperature and lubrication conditions on the vibration reduction effect of the GISFD is not fully studied. Future research could focus on addressing these limitations and further exploring the application potential of the GISFD in gear vibration reduction.
In conclusion, this research provides a new approach for vibration reduction in helical gear transmission systems and has important implications for improving the performance and reliability of mechanical equipment. Further research in this area can lead to more effective vibration control methods and contribute to the development of advanced manufacturing technologies.