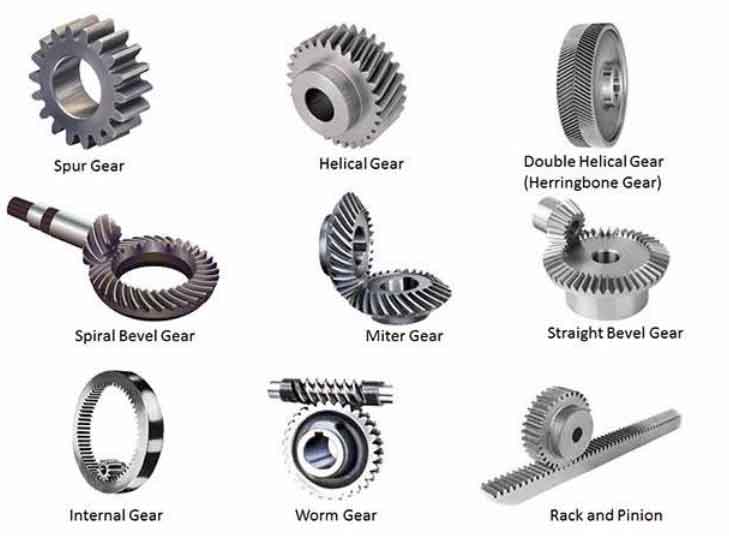
Gears are fundamental components in mechanical systems, providing the means to transmit torque and rotational motion between shafts. Among the various types of gears, helical and spur gear is commonly used in high-performance applications due to their specific advantages. This article provides a detailed comparative analysis of helical and spur gear, focusing on their design, performance, and suitability for different high-performance applications.
Introduction
Gears are essential for the efficient transmission of power in many mechanical systems. While spur gear has been widely used for their simplicity and efficiency, helical gear ais often preferred in high-performance applications due to their smoother operation and higher load-carrying capacity.
Design and Geometry
Spur Gear:
- Shape: Teeth are straight and parallel to the axis of the spur gear.
- Contact: Teeth engage and disengage instantly along the whole face width, causing a sudden application of load.
- Manufacturing: Easier and less expensive to manufacture.
Helical Gear:
- Shape: Teeth are cut at an angle to the face of helical gear, creating a helical shape.
- Contact: Teeth engage gradually, spreading the load over multiple teeth and providing smoother operation.
- Manufacturing: More complex and costly due to the angled teeth.
Parameter | Spur Gear | Helical Gear |
---|---|---|
Teeth Profile | Straight | Angled (Helical) |
Load Distribution | Instantaneous, single point | Gradual, multiple teeth |
Noise Level | Higher | Lower |
Manufacturing | Simpler and cheaper | More complex and expensive |
Performance Characteristics
Efficiency:
- Spur Gear: Generally have higher efficiency due to lower frictional losses.
- Helical Gear: Slightly lower efficiency because of increased friction due to the sliding contact of helical teeth.
Load Capacity:
- Spur Gear: Suitable for moderate load applications.
- Helical Gear: Can handle higher loads due to better load distribution.
Noise and Vibration:
- Spur Gear: Produce more noise and vibration because of the sudden engagement of teeth.
- Helical Gear: Quieter and produce less vibration due to gradual engagement.
Parameter | Spur Gear | Helical Gear |
---|---|---|
Efficiency | Higher | Slightly lower |
Load Capacity | Moderate | High |
Noise and Vibration | Higher | Lower |
Suitability for High-Performance Applications
Spur Gears:
- Best suited for applications where simplicity, cost-effectiveness, and high efficiency are prioritized.
- Common in machinery where noise and vibration are less critical.
Helical Gears:
- Ideal for high-performance applications requiring high load capacity, smooth operation, and reduced noise.
- Widely used in automotive transmissions, high-speed machinery, and industrial gearboxes.
Case Study: Automotive Transmission
In automotive transmissions, the choice between spur and helical gear is critical for performance and user experience. Helical gear is preferred due to their ability to handle higher loads, operate quietly, and ensure smooth power delivery. This is crucial in high-performance vehicles where noise, vibration, and harshness (NVH) are significant considerations.
Conclusion
Both helical and spur gear has their unique advantages and are suited for different applications. While spur gear offer simplicity and higher efficiency, helical gear excel in high-load and high-performance environments with smoother operation and reduced noise. The choice between the two should be based on the specific requirements of the application, considering factors such as load capacity, noise levels, and manufacturing costs.