Fig. 1 shows the experimental vibration acceleration signals of healthy gear and pitting gear. It can be seen from the figure that the vibration plus signal of the healthy gear is relatively stable in the time domain as a whole, and the amplitude is also small; while the vibration acceleration signal of the pitting fault gear has a more obvious increase than that of the healthy gear, and there are many abnormal amplitudes of the vibration acceleration signal of the pitting fault gear in the time domain. The above phenomenon is basically consistent with the phenomenon of gear system simulation signal in time domain, which verifies the correctness of the simulation model in time domain, and reveals the influence of pitting fault on gearbox system.
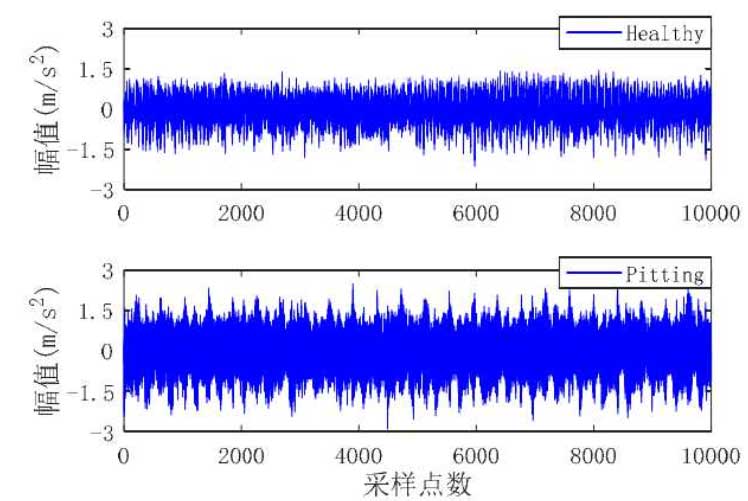
In order to quantify the fault characteristics of vibration acceleration signals of healthy gears and pitting failure gears in the experiment, the statistical indexes of vibration acceleration signals of healthy gears and pitting failure gears are given in Fig. 2. It can be seen from the bar graph that the RMS value and peak peak value of vibration acceleration signal of pitting fault gear are increased compared with that of healthy gear, which is consistent with the RMS value and peak peak performance characteristics of simulation signal, where RMS value is higher than that of normal gear The peak coefficient of pitting fault gear is smaller than that of healthy gear, which may be due to the interference of external noise during the experiment.
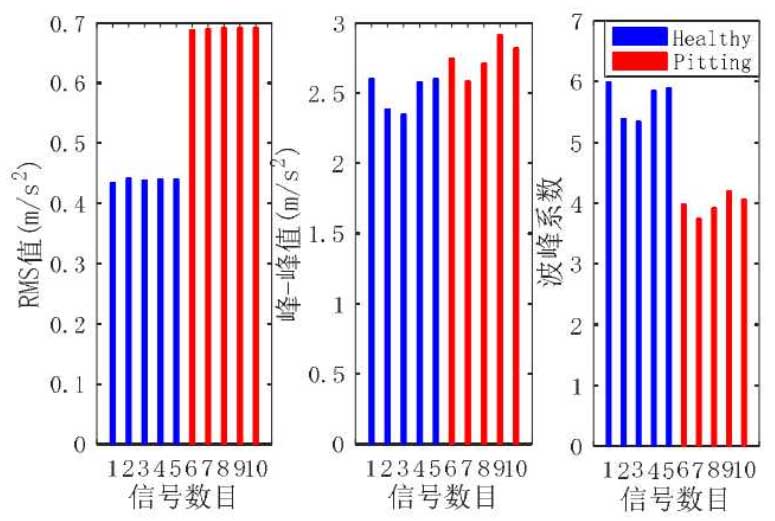
The experimental platform for measuring the dynamic strain of gear tooth root is built, and the dynamic strain of gear tooth root is measured and studied. At the same time, the semi analytical calculation method and Experimental Research on the medium degree pitting fault of gear are also carried out. For the healthy gear system and the gear system with moderate pitting failure, the vibration response of the gear system and the dynamic strain of the gear root are measured by vibration acceleration sensor and fiber Bragg grating sensor respectively. According to the potential energy principle and the theory of material mechanics, the relationship between the bending strain of tooth root and the meshing stiffness of gear is deduced. The meshing stiffness of healthy gear and gear with moderate pitting corrosion is obtained by calculating the dynamic strain of tooth root measured by fiber Bragg grating sensor. Then the dynamic response of gear system is analyzed and studied by using the dynamic model of gear system When the degree pitting fault occurs, the amplitude of vibration response signal will increase abnormally in time domain, and its statistical index value will also increase, such as RMS value, peak peak value, etc. Finally, the experimental vibration signal is analyzed and compared with the simulation results. The simulation results are basically consistent with the experimental results, which verifies the correctness of the simulation results.