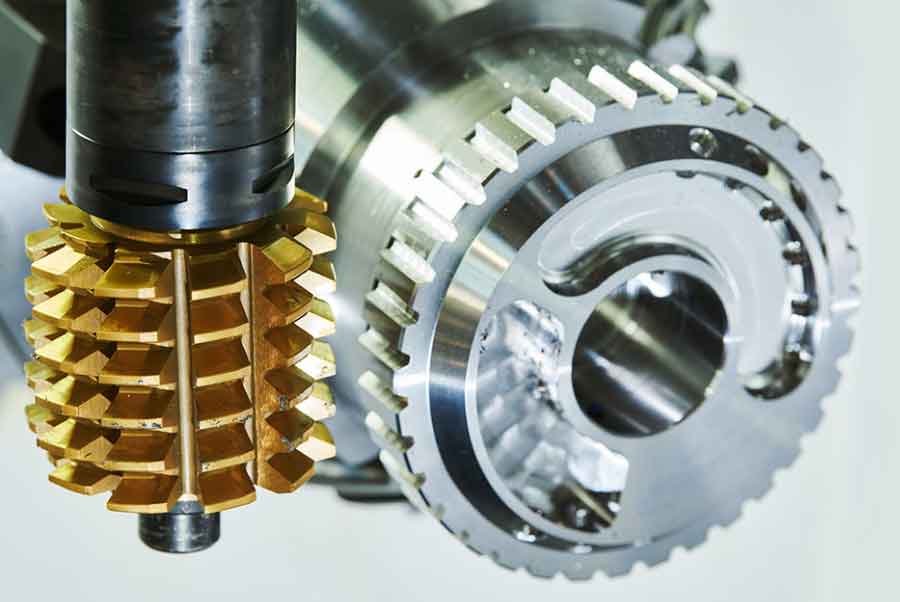
Gear hobbing technology has undergone significant advancements over the years, driven by the need for increased productivity, improved precision, and enhanced flexibility in gear manufacturing. This article explores some of the key advancements in gear hobbing technology that have revolutionized the industry.
I. CNC Gear Hobbing Machines:
Computer Numerical Control (CNC) gear hobbing machines have revolutionized the gear manufacturing process. These machines integrate advanced control systems, precision servo motors, and high-resolution feedback devices to achieve precise control over the cutting process. CNC gear hobbing machines offer programmable flexibility, allowing for the production of a wide range of gear types and profiles with high accuracy and repeatability.
II. Multi-Axis and Multi-Tasking Machines:
Multi-axis gear hobbing machines have expanded the capabilities of gear manufacturing. These machines feature multiple axes of motion, allowing for simultaneous cutting and indexing of complex gear profiles. The integration of additional machining operations, such as drilling, milling, and chamfering, within the same machine further enhances productivity and eliminates the need for multiple setups.
III. High-Speed Gear Hobbing:
Advancements in machine design, cutting tool materials, and cutting strategies have led to high-speed gear hobbing capabilities. High-speed gear hobbing machines can achieve significantly faster cutting speeds, reducing cycle times and increasing productivity. Additionally, high-speed cutting improves surface finish, reduces tool wear, and enables the production of gears with higher accuracy and quality.
IV. Dry Hobbing and Minimal Lubrication Systems:
Traditional gear hobbing often involves the use of cutting fluids or lubricants to facilitate the cutting process and dissipate heat. However, advancements in tool coatings and materials, along with the development of dry hobbing and minimal lubrication systems, have eliminated the need for excessive lubrication. Dry hobbing reduces environmental impact, simplifies cleaning processes, and eliminates the need for coolant management.
V. High-Performance Hob Cutters:
The development of high-performance hob cutters has significantly improved gear hobbing technology. Advanced coatings, such as TiAlN (Titanium Aluminum Nitride) and TiCN (Titanium Carbonitride), enhance tool life, reduce friction, and improve wear resistance. Additionally, optimized geometries and cutting edge designs enhance cutting efficiency, accuracy, and surface finish, resulting in high-quality gears.
VI. Simulation and Virtual Testing:
Advancements in simulation and virtual testing software have transformed gear hobbing technology. Engineers can simulate the gear hobbing process, analyze tool paths, optimize cutting parameters, and predict gear behavior before actual production. Virtual testing allows for rapid prototyping, reduces trial and error, and enhances the overall efficiency of gear manufacturing.
VII. Intelligent Monitoring and Control Systems:
Intelligent monitoring and control systems have become integral to gear hobbing technology. These systems utilize sensors, real-time data analysis, and machine learning algorithms to monitor and optimize the gear hobbing process. They can detect tool wear, monitor cutting forces, identify potential issues, and automatically adjust cutting parameters to ensure consistent quality and maximize productivity.
VIII. Industry 4.0 Integration:
Gear hobbing technology is being integrated into the broader concept of Industry 4.0, where data exchange, automation, and digital connectivity play a significant role. Integration with manufacturing execution systems (MES), cloud-based platforms, and IoT-enabled devices allows for real-time monitoring, remote diagnostics, and predictive maintenance, optimizing overall production efficiency.
Conclusion: Advancements in gear hobbing technology have transformed the gear manufacturing industry, enabling increased productivity, improved precision, and enhanced flexibility. CNC machines, multi-axis and multi-tasking capabilities, high-speed cutting, dry hobbing, high-performance hob cutters, simulation and virtual testing, intelligent monitoring systems, and Industry 4.0 integration have revolutionized the gear hobbing process. These advancements have not only improved the efficiency of gear manufacturing but also enabled the production of high-quality gears with tighter tolerances, complex profiles, and improved performance characteristics. As gear hobbing technology continues to evolve, gear manufacturers can expect further enhancements in productivity, precision, and process control, catering to the ever-growing demands of various industries.