The automobile gear is in the state of continuous load operation. There are rolling and sliding between the meshing surfaces of the gear. At the same time, the root of the gear is also affected by pulse and alternating bending stress. There are usually four different failure modes of gears:
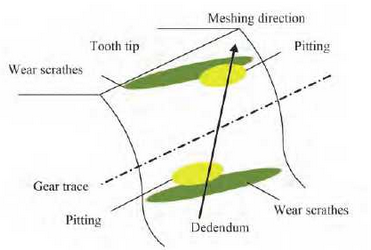
① Broken teeth;
② Macro pitting and micro pitting;
③ Wear;
④ The tooth surface is glued.
Most of the failures of the gears mentioned above come from the surface of the tooth surface or root, so it can be seen that the surface of the gears is very important. The surface integrity of the gears refers to the surface state after no damage or strengthening and the performance determined by it [3]. The surface integrity of the gears includes the surface residual stress, microhardness, surface roughness, microstructure, etc., and the thickness and Bond strength and other factors. No matter the surface chemical heat treatment or shot peening deformation strengthening treatment, the surface roughness, morphology, structure, hardness and residual stress of the gear surface integrity are all affected, and the surface integrity of the gear is closely related to its bending fatigue resistance and contact fatigue resistance.
1. Research on the mechanism and material of gear bending fatigue damage
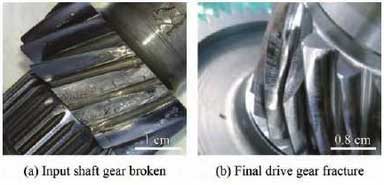
The strength of gear is mainly the bending fatigue strength of gear and the contact fatigue strength of gear surface. The figure shows the bending fracture of the gear. The main reason is that the root of the gear is subject to repeated concentrated stress to produce cracks and gradually expand to cause failure. The bending fatigue cracks are generated from the grain boundary oxide layer on the surface of the gear, and propagate along the austenite grain boundary under the surface to the depth of the hardened layer, which causes the crystal boundary damage.
The grain boundary oxide layer on the surface of the material is mainly composed of Si, Mn, Cr and other alloy elements which can improve the quenching performance. The edge of the grain boundary is easy to produce partial incomplete quenching field, forming the abnormal layer of incomplete carburization composed of Troostite and bainite. The figure shows the grain boundary oxidation structure of 20CrMoH sample after carburizing and quenching, and the black whisker like components extending from the surface to the interior are the oxides of Si, Mn and Cr.
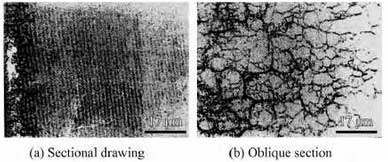
In order to improve the bending fatigue strength of gears, the R angle of gear root is usually increased, and the high pressure angle is designed. For example, the method to improve the abnormal layer of incomplete carburization can generally be used to increase the quenching speed, but attention should be paid to avoid large tooth surface deformation; or the alloy elements such as Ni, Mo, etc. which are conducive to improving the quenching performance can be used to reduce the content of Si, Mn, Cr and other elements at the same time.
2. Tooth contact fatigue mechanism and material
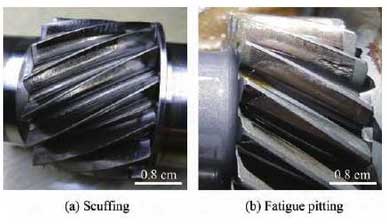
The fatigue damage of tooth surface is caused by the repeated action of the tooth surface contact stress and the tensile stress caused by the different relative sliding speed of the tooth surface mesh. The damage forms are mainly surface damage pitting and peeling, and Figure 4 is an example of gear pitting damage. The fatigue pitting life of the gear surface is directly proportional to the surface temperature, the roughness of the gear surface and the friction coefficient when the gear is meshed, and inversely proportional to the dynamic viscosity of the lubricating oil. Generally, increasing the hardness of material at high temperature and tempering softening resistance can effectively increase the fatigue life of gear tooth surface. The test shows that increasing the carbon content of tooth surface from 0.8% ~ 1.0% to 2.0% ~ 3.0% can inhibit the high temperature softening of material surface, but the carburizing time and diffusion time need to be strictly controlled due to the large amount of micro carbide precipitation in high concentration carburizing. The figure shows the relationship between the hardness of high concentration carburizing and common carburizing, surface distance and surface temperature.
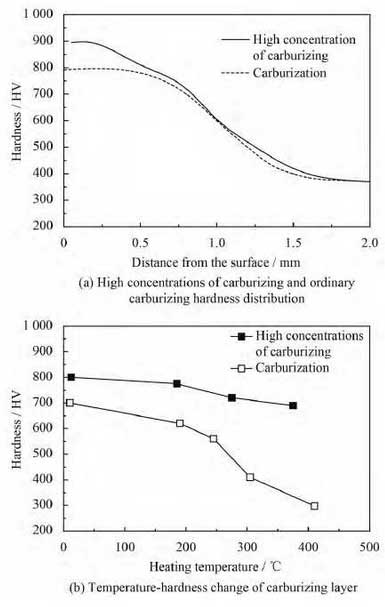
Another method is to properly increase the content of Si, Cr and other alloy elements in the material and to implement the carbonitriding heat treatment method can greatly improve the contact fatigue life of the tooth surface, as shown in Figure 6 is the comparison of pitting fatigue test results of gear steel with different alloy composition on the dynamic cycle test bench (CQT: carburizing, cnqt: carbonitriding).
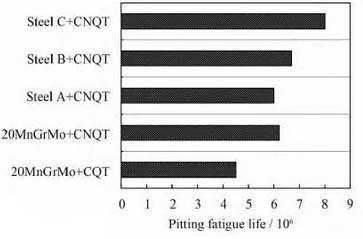