Shot peening is a widely used method to improve the fatigue strength of gears, which can produce compression deformation on the surface of gears by mechanical means and produce deformation modified layer on the surface, so as to improve the surface strength. Shot peening causes a large amount of plastic deformation in the strengthening layer of the tooth surface, and the residual austenite on the surface of the tooth surface transforms to martensite. The martensite induced by the transformation has directionality, and is arranged in parallel bundles along the slip line. The dislocation density of the original martensite increases, and the structure is refined. Shot peening improves the microhardness of the gear surface and the residual compressive stress of the tooth surface under tens of microns, which can be greatly improved Improve the bending fatigue strength limit and service life of automobile gear [20]. Shot peening causes the following major changes in gear surface integrity, namely:
① The residual compressive stress field is introduced;
② The microstructure was refined by deformation;
③ Change of surface hardness;
④ Change of surface roughness;
Among them, ① ② ③ the first four kinds of surface changes can improve the fatigue life of gears, while the increase of surface roughness brought by shot peening may reduce the fatigue performance of materials, worsen the noise of gears, and is not conducive to the vibration and noise characteristics of automobiles. The influence of shot peening on the surface integrity of gear is improved by controlling the process parameters such as shot peening intensity and shot diameter and adopting compound shot peening. The key to control the surface integrity of gear peening is to control the distribution of residual stress and the surface roughness of gear surface, so as to avoid two kinds of improper peening, i.e. “under spraying” and “over spraying”.
1. Strong shot peening
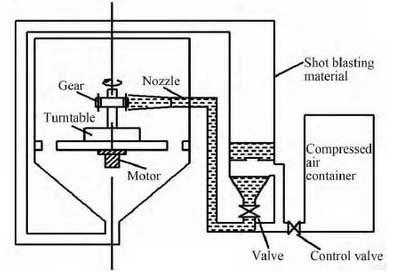
In China, many kinds of surface shot peening technology have been developed for the research of the surface strengthening technology of automobile gear’s bending fatigue strength. As shown in the figure, it is the schematic diagram of gear surface shot peening.
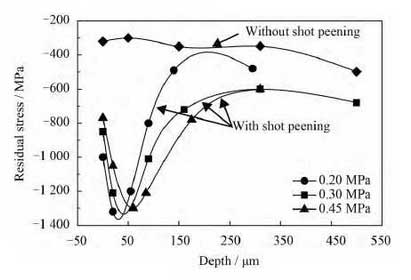
Mazda Automobile Company of Japan firstly researched and developed the surface strong shot peening technology of high pressure nozzle gear. Under the condition of room temperature, the high hardness cast steel shot (Φ 0.4mm ~ 0.6mm) collides with the gear surface at high speed under high pressure by using the nozzle peening machine with excellent controllability, which makes the gear surface strengthened at the moment of repeated heating and quenching, and the residual compressive stress near the gear surface is significantly increased, so as to restrain the development of fatigue crack. The figure shows the distribution of residual compressive stress near the surface of tooth surface after shot peening with Φ 0.6 mm steel shot under different pressure conditions, and the hardness of tooth surface also has some work hardening.
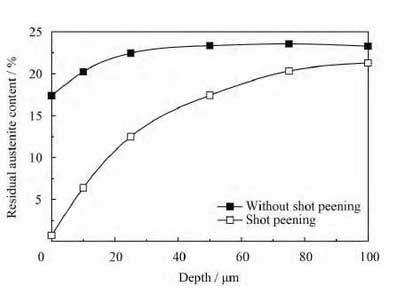
As shown in the figure, the change curve of residual austenite content with depth in the surface layer of low carbon alloy steel gear after strong shot peening and before shot peening is compared. Before shot peening, the austenite mass fraction in the surface layer is about 20% ~ 25%, and during shot peening, the austenite transforms into martensite. The austenite mass fraction in the surface layer of 0 ~ 50 μ m is 0.3% ~ 12%. Generally, under the same other conditions, the greater the shot peening strength is, the deeper the transformation depth of retained austenite into martensite is, and the more the transformation amount of retained austenite into martensite is; that is, the shot peening strength is directly proportional to the transformation depth and transformation amount of martensite.
2. Particle peening
Strong shot peening can greatly improve the residual compressive stress near the gear surface, promote the transformation of retained austenite into martensite, improve the bending fatigue strength of the gear, but also increase the surface roughness of the gear. The particle peening technology can not only improve the residual compressive stress near the gear surface, but also effectively reduce the impact of shot peening on the gear surface roughness, which meets the requirements of gear surface roughness.
3. Composite shot peening
A research and development center of automatic transmission in China has studied the surface modification and strengthening of transmission gears by high-pressure and powerful composite shot peening technology, which greatly improves the fatigue life of gears. That is to say, shot peening with high hardness and larger shot (Φ 0.6 ~ 1.0mm) under high pressure and high speed is adopted firstly, and then shot peening with small diameter and high hardness shot (Φ 0.1 ~ 0.2) is adopted Mm) shot peening, forming compound residual compressive stress on the surface of gear, reducing the surface work hardening, improving the surface roughness, improving the surface hardness, significantly improving the residual compressive stress near the tooth surface, thus inhibiting the development of gear fatigue crack. It not only ensures that there is a large residual compressive stress near the tooth root of the gear, but also does not change the surface roughness of the gear. For the specific strength of shot peening, the test piece is generally used to measure the shot peening strength.
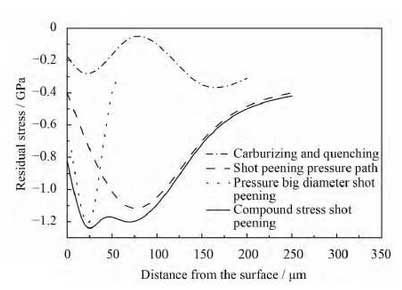
As shown in the figure, the distribution of residual compressive stress near the gear surface after different types of surface shot peening treatment, in which the effect of composite shot peening is more obvious than that of particle shot peening and strong shot peening, and the maximum residual compressive stress on the surface can reach 1300 MPa.
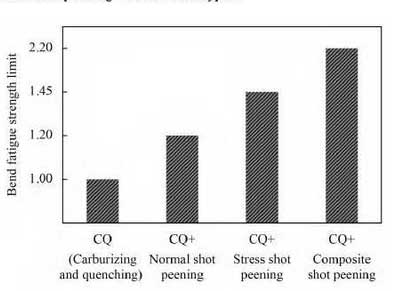
As shown in the figure, the bending fatigue strength limit of various shot peening methods is made by using the rotary bending fatigue test, and the bending fatigue limit of gear after shot peening treatment is greatly increased. After carburizing and quenching, the bending fatigue limit of gear can be increased more than twice by using surface compound shot peening.
4. Research on other new shot peening technologies
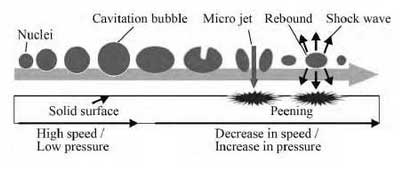
With the development of science and technology, as an important technology to introduce residual compressive stress, change the structure of surface materials, and enhance the fatigue life, new technologies are constantly developed and applied, such as cavitation water shot peening, laser hole shot peening, ultrasonic shot peening, etc. The figure shows the principle of cavitating water shot peening. The process uses the shock wave pressure and high-speed micro jet produced when the micro cavitating bubble collapses to strike the surface of the gear, so that the high-density dislocation accumulates in the surface layer of the gear to form the residual compressive stress layer, so as to achieve the purpose of strengthening the metal surface. Laser hole peening can peen in a narrow space through the shock wave generated by the collapse of the micro cavitation bubble at the laser focal point. The parameters can be precisely controlled, and the residual compressive stress is greater [26]. In ultrasonic peening, the projectile impacts the fixed material surface with super sound frequency from all directions. Because of the large energy introduced into the material, it can be used to realize the nano surface of the material and reduce the nitriding temperature.