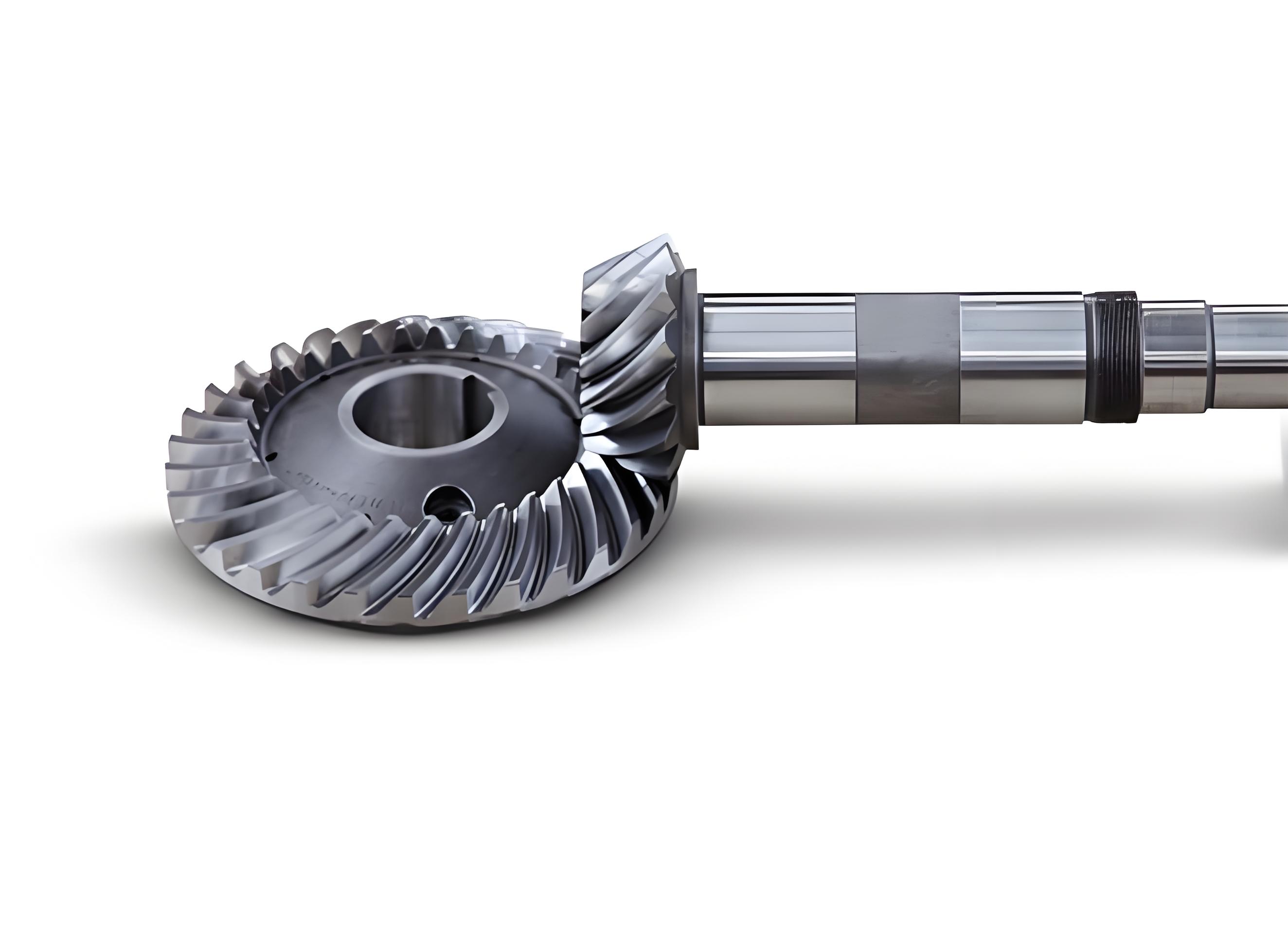
Abstract
Finite Element Analysis (FEA) is a powerful computational tool used to study stress distribution in spiral bevel gear under variable load conditions. This paper explores the methodology, implementation, and outcomes of using FEA to analyze and optimize the stress distribution in spiral bevel gear, enhancing their performance and durability in various applications.
Introduction
Spiral bevel gear is critical components in mechanical systems, transmitting power between intersecting shafts with high efficiency. Understanding the stress distribution within these spiral bevel gear under variable load conditions is essential for improving their design, performance, and longevity. FEA provides a detailed insight into the stress patterns, enabling engineers to optimize spiral bevel gear geometry and material properties.
Methodology
- Gear Modeling
- Geometric Modeling: Creating a precise 3D model of the spiral bevel gear using CAD software.
- Material Properties: Defining the material properties, including Young’s modulus, Poisson’s ratio, and yield strength.
- Finite Element Meshing
- Mesh Generation: Discretizing the 3D model into finite elements, ensuring a fine mesh in regions of high stress concentration.
- Mesh Refinement: Applying mesh refinement techniques to enhance accuracy in critical areas.
- Boundary Conditions and Load Application
- Boundary Conditions: Setting appropriate boundary conditions to simulate the spiral bevel gear’s operational environment.
- Load Conditions: Applying variable load conditions to represent realistic operating scenarios, including static, dynamic, and impact loads.
- Simulation and Analysis
- Solver Configuration: Selecting appropriate solvers and configuring simulation parameters.
- Stress Analysis: Running simulations to analyze the stress distribution across the spiral bevel gear teeth and identifying areas of high stress concentration.
Results and Discussion
- Stress Distribution Patterns
- Static Load Conditions: Under static loads, stress concentrations are typically found at the root and flank of spiral bevel gear teeth.
- Dynamic Load Conditions: Dynamic loads introduce additional stress variations due to spiral bevel gear’s rotational motion and load fluctuations.
- Impact Loads: Sudden impact loads can cause significant localized stress spikes, potentially leading to spiral bevel gear failure.
- Effect of Gear Geometry
- Tooth Profile Optimization: Modifying the tooth profile to achieve a more uniform stress distribution, reducing peak stresses.
- Root Fillet Design: Enhancing the root fillet design to minimize stress concentration at the tooth root.
- Material Considerations
- Material Selection: Analyzing different materials and their impact on stress distribution, with a focus on high-strength alloys and composites.
- Heat Treatment Effects: Evaluating the effects of heat treatment processes, such as carburizing and nitriding, on stress distribution and spiral bevel gear performance.
- Load Distribution Analysis
- Load Sharing: Investigating the load-sharing characteristics of spiral bevel gear teeth under variable load conditions.
- Contact Stress: Analyzing contact stress between mating spiral bevel gear teeth and optimizing contact patterns for enhanced performance.
Case Studies
- Automotive Applications
- Gearbox Gears: FEA results for gearbox gear under variable speed and torque conditions, highlighting areas for design improvement.
- Differential Gears: Analysis of differential spiral bevel gear subjected to varying loads during cornering and acceleration.
- Aerospace Applications
- Helicopter Transmission Gears: Stress analysis of helicopter transmission spiral bevel gear under fluctuating flight loads, emphasizing the importance of material selection and heat treatment.
- Jet Engine Gears: Evaluating the stress distribution in jet engine spiral bevel gear operating under extreme temperatures and loads.
- Industrial Machinery
- Heavy-Duty Machinery Gears: FEA of spiral bevel gear in heavy-duty machinery exposed to intermittent and high-impact loads, focusing on durability and wear resistance.
- Robotic Actuator Gears: Stress analysis of spiral bevel gear used in robotic actuators, considering precision and load-carrying capacity.
Conclusion
FEA is an invaluable tool for analyzing stress distribution in spiral bevel gear under variable load conditions. The insights gained from FEA can guide the optimization of spiral bevel gear design, material selection, and manufacturing processes, leading to enhanced performance and reliability. Ongoing advancements in computational techniques and material science promise further improvements in spiral bevel gear analysis and optimization.
References
- International Journal of Mechanical Sciences: Articles on the application of FEA in spiral bevel gear analysis.
- Journal of Materials Processing Technology: Research on material properties and their impact on spiral bevel gear performance.
- Tribology International: Studies on the effects of variable load conditions on spiral bevel gear wear and stress distribution.
- Finite Elements in Analysis and Design: Papers on advanced FEA techniques and their application in mechanical engineering.
This paper provides a comprehensive overview of using FEA to analyze stress distribution in spiral bevel gear, serving as a valuable resource for researchers, engineers, and industry professionals involved in spiral bevel gear design and optimization.