The mesh quantity and quality of the finite element model directly affect the speed and accuracy of the calculation results. In order to improve the calculation speed and ensure that there are 2 ~ 3 complete meshing periods, the 6-tooth finite element mesh model of gear pair is obtained by using HyperMesh preprocessing division. As shown in the figure, c3d8r element is used to improve the calculation accuracy. Based on ABAQUS finite element quasi-static analysis method and implicit static analysis method, the contact analysis model is established. As shown in FIG. 10, the meshing simulation of four groups of gear pairs established in Section 3.1 is carried out. In the finite element model analysis, there are four analysis steps: initial step, which constrains all degrees of freedom;
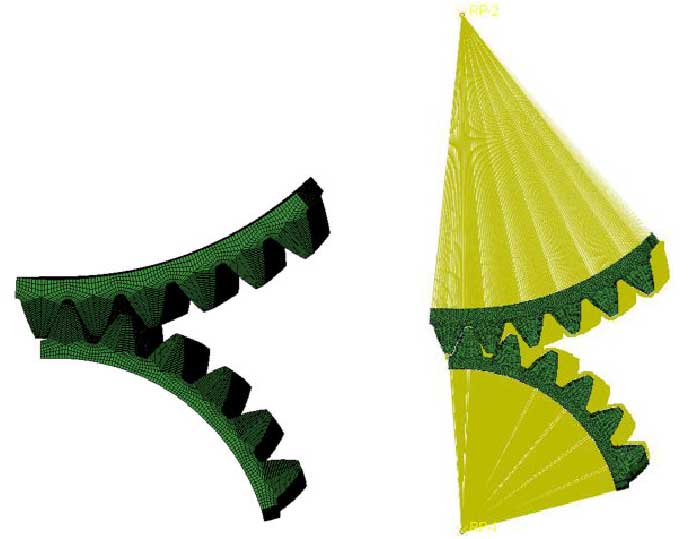
In the first step, the driving wheel (small wheel) keeps the constraint unchanged, and the driven wheel (big wheel) rotates around the axis at a small angle to avoid no contact between the tooth surfaces;
In the second step, the driving wheel keeps the constraint unchanged, and the driven wheel releases the degree of freedom around the axis, and applies small torque to ensure the convergence of load torque analysis in step 3;
In the third step, the driving wheel keeps the constraint unchanged, and the driven wheel releases the degree of freedom around the axis and increases the torque to the rated value;
In step 4, the driving wheel rotates about the axis by 6 teeth corresponding to the angle, and the driven wheel is the same as the third step.
Thus, the working condition of the driving wheel and the driven wheel resisting the load torque through meshing is simulated.