In ADAMS, the meshing between gear and gear is simulated by contact pair and collision contact force. Therefore, ADAMS simulation software provides users with two collision contact force models, one is impact contact force model based on stiffness and damping coefficient, the other is restitution The contact force model is based on the coefficient of restitution. Because the impact model is more in line with the actual situation of gear meshing and the relevant parameters are easy to obtain, it is widely used in the simulation analysis of gear transmission. The impact contact force model is also used to define the gear pair in the system.
The function expression of the impact contact force model is as follows:
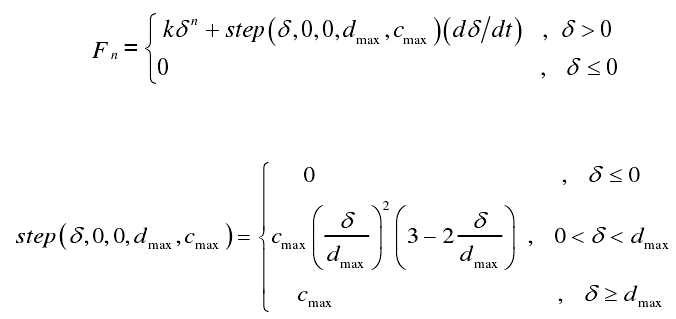
Where:
K — contact stiffness coefficient;
δ — penetration depth of two contact collisions;
N — rigidity force index not less than 1;
Cmax — maximum damping coefficient;
D δ / dt — the velocity of two objects;
Dmax — the distance required to reach the maximum damping coefficient.
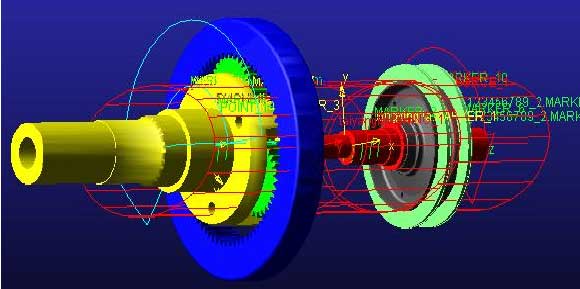
After completing the above steps, the virtual prototype simulation model of the sealed rotor system considering the gear meshing characteristics is established, as shown in the figure.