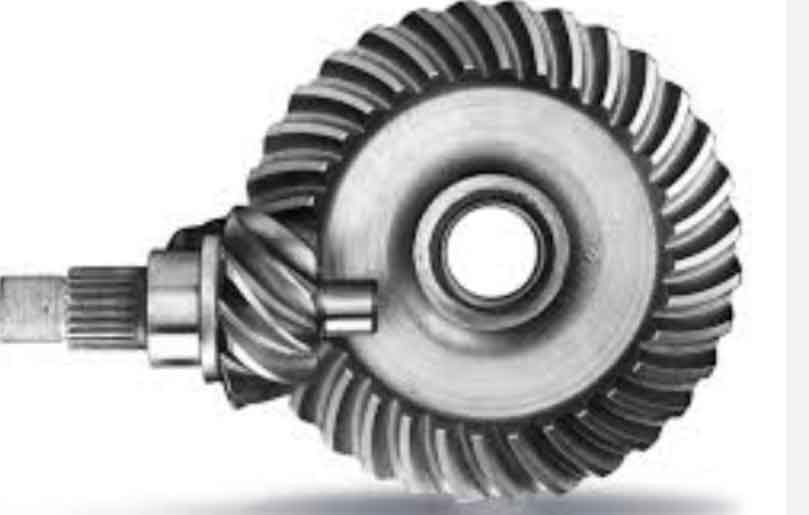
Gear engineering excellence is crucial when leveraging the potential of hypoid gears. Here are some key considerations to ensure optimal performance and maximize the benefits of hypoid gears:
- Gear Design Optimization:
- Collaborate with experienced gear designers who have a deep understanding of hypoid gear geometry and design principles.
- Optimize the gear tooth profile, tooth contact pattern, and gear ratio to meet the specific requirements of the application.
- Utilize advanced gear design software and simulation tools to analyze and optimize gear performance.
- Material Selection:
- Choose high-quality materials with excellent strength, durability, and wear resistance to ensure long-lasting performance.
- Consider factors such as load capacity, operating conditions, and temperature requirements when selecting gear materials.
- Consult with material experts or gear manufacturers to determine the most suitable material for the specific application.
- Manufacturing Precision:
- Collaborate with skilled gear manufacturers equipped with advanced machining capabilities and quality control processes.
- Ensure precise gear cutting, heat treatment, and finishing processes to achieve the required gear tooth accuracy and surface finish.
- Implement rigorous quality control measures throughout the manufacturing process to maintain consistent gear quality.
- Lubrication and Maintenance:
- Proper lubrication is essential for optimal gear performance and longevity. Select lubricants suitable for hypoid gears, considering factors such as viscosity, temperature range, and additive packages.
- Follow recommended lubrication intervals and maintenance procedures to minimize wear, reduce friction, and prevent gear failures.
- Regularly monitor gear performance, inspect for any signs of wear or damage, and address maintenance issues promptly.
- Noise and Vibration Control:
- Implement effective noise and vibration control measures to minimize the inherent characteristics of hypoid gears.
- Consider using noise reduction techniques such as gear tooth modifications, gear housing design optimization, or adding noise-damping materials.
- Conduct thorough testing and analysis to identify and address any potential noise and vibration issues during the design and development stages.
- Application-Specific Optimization:
- Collaborate closely with gear engineers and manufacturers to optimize hypoid gears for the specific application requirements.
- Consider factors such as torque, speed, operating conditions, environmental factors, and load distribution to achieve the best performance and reliability.
- Conduct thorough testing and validation to ensure the hypoid gears meet or exceed the desired performance targets.
By leveraging gear engineering excellence, including design optimization, material selection, precision manufacturing, proper lubrication, noise control, and application-specific optimization, the potential of hypoid gears can be fully realized. Collaborating with knowledgeable gear engineers and manufacturers is crucial to ensure the successful implementation and performance of hypoid gears in your machinery or system.