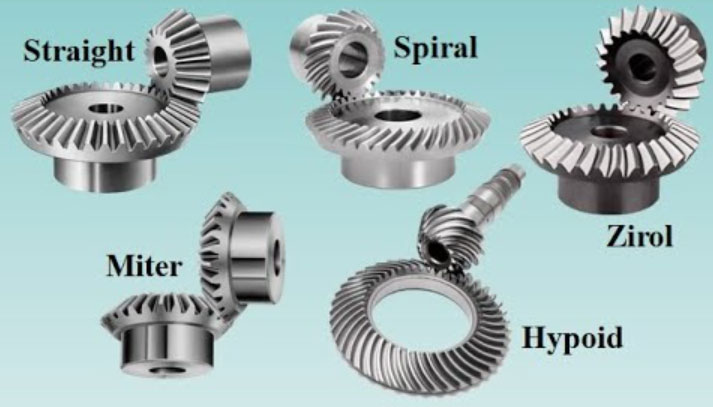
Bevel gears are a type of gears used to transmit motion and power between non-parallel shafts. They feature cone-shaped gear teeth that are cut on the surface of a cone. Bevel gears are categorized into different types based on their tooth geometry and orientation, such as straight bevel gears, spiral bevel gears, and hypoid bevel gears. Let’s explore the mechanics of bevel gears in detail:
1. Tooth Geometry:
Bevel gears have teeth cut along the surface of a cone. The tooth profile varies depending on the specific type of bevel gear. Straight bevel gears have straight teeth cut along the cone surface, while spiral bevel gears have curved teeth that spiral around the cone. The tooth profile of bevel gears enables smooth and efficient power transmission.
2. Shaft Orientation:
Bevel gears are designed to transmit motion and power between intersecting or non-parallel shafts. The shafts on which the bevel gears are mounted intersect at a common point for intersecting shafts or form an angle for non-parallel shafts. The angle between the shafts determines the type of bevel gear required and affects the gear’s performance.
3. Force Transmission:
Bevel gears transmit rotational motion and torque between the shafts. The angled teeth of bevel gears allow for efficient power transmission and force distribution. When the gears rotate, the teeth engage and transfer the rotational force from the driving gear to the driven gear. The force transmission in bevel gears is perpendicular to the gear axis, resulting in changes in direction and speed of rotation.
4. Gear Ratios: The gear ratio of bevel gears is determined by the number of teeth on each gear and their relative sizes. The gear ratio affects the speed and torque relationship between the input and output shafts. Different gear arrangements, such as 1:1, speed-increasing, or speed-reducing ratios, can be achieved with bevel gears by selecting gears with the appropriate tooth counts.
5. Spiral Bevel Gears:
Spiral bevel gears are a common type of bevel gears used in various applications. They have curved teeth that are cut in a spiral pattern around the cone surface. The spiral tooth profile allows for smooth tooth engagement and gradual load transfer, reducing noise and vibration. Spiral bevel gears provide high load-carrying capacity and are widely used in automotive differentials, heavy machinery, and power transmission systems.
6. Hypoid Bevel Gears:
Hypoid bevel gears are a specialized type of bevel gears that have non-intersecting and non-parallel shafts. They are typically used in applications where the input and output shafts must be offset or crossed. Hypoid bevel gears feature a hypoid shape, which is a combination of spiral bevel and offset gear geometry. They offer high torque transmission capabilities, compact design, and smooth operation.
7. Applications of Bevel Gears:
Bevel gears find applications in a wide range of industries and systems. They are commonly used in automotive differentials, marine propulsion systems, heavy machinery, power tools, and aerospace applications. Bevel gears are particularly advantageous in systems where non-parallel or intersecting shafts require efficient power transmission and changes in rotational direction.
Bevel gears are versatile mechanical components that enable efficient power transmission between non-parallel or intersecting shafts. Their tooth geometry, shaft orientation, and various types offer flexibility in design and application. Understanding the mechanics of bevel gears is essential for selecting the appropriate gear type and arrangement to achieve the desired motion and force transmission requirements in different systems.