Gear failure analysis and prevention are critical aspects of maintaining the performance and reliability of straight bevel gear systems. Gear failures can lead to costly downtime, production delays, and equipment damage. Here are some common gear failure modes in straight bevel gears and strategies for prevention:
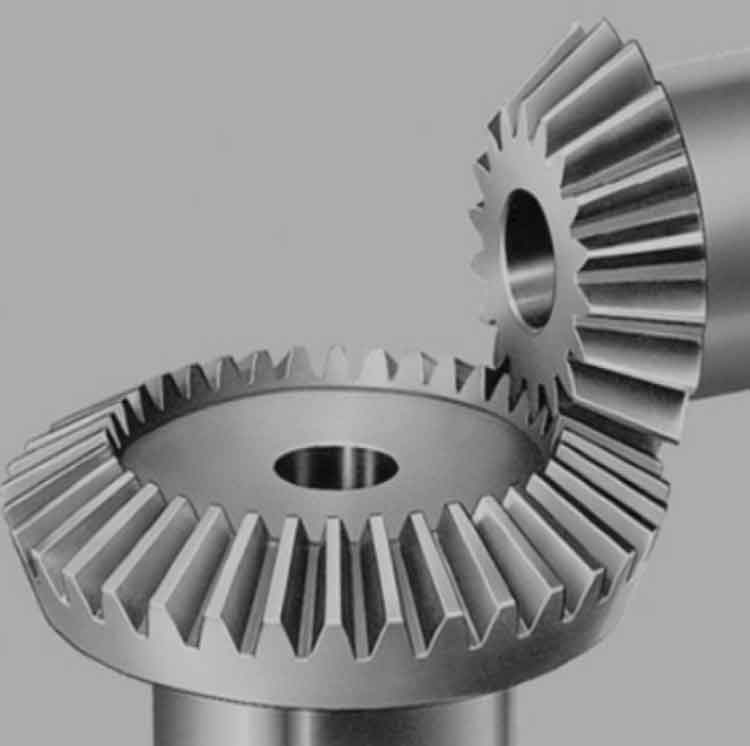
1. Wear and Pitting:
- Root Cause: Excessive load, misalignment, or inadequate lubrication can lead to wear and pitting on gear teeth surfaces.
- Prevention: Proper gear alignment, correct lubricant selection, and regular lubricant maintenance can help prevent wear and pitting. Additionally, avoiding overload situations and ensuring adequate gear material strength are essential.
2. Tooth Breakage:
- Root Cause: Tooth breakage can occur due to overloading, shock loads, or material fatigue.
- Prevention: Ensuring that the gear is appropriately sized and rated for the application’s load conditions can prevent tooth breakage. Proper material selection, heat treatment, and controlled manufacturing processes also contribute to gear strength and resilience.
3. Tooth Deformation and Bending:
- Root Cause: Excessive bending loads on the gear teeth can lead to permanent deformation.
- Prevention: Proper gear design, including tooth profile and thickness, can minimize the risk of bending and deformation. Adequate lubrication and load distribution across gear teeth are essential for preventing excessive bending stress.
4. Scuffing and Galling:
- Root Cause: Insufficient lubrication or high contact pressures can cause scuffing and galling, where metal surfaces weld or transfer material.
- Prevention: Selecting the right lubricant with appropriate additives for extreme pressure conditions can reduce the risk of scuffing and galling. Maintaining lubricant quality and cleanliness is crucial.
5. Fretting and Corrosion:
- Root Cause: Micro-motions between mating surfaces can lead to fretting wear and corrosion, particularly in lightly loaded gears or applications with vibrations.
- Prevention: Proper design to minimize micro-motions, using anti-fretting coatings or surface treatments, and maintaining a clean operating environment can prevent fretting and corrosion.
6. Tooth Chipping and Spalling:
- Root Cause: High shock loads, poor material quality, or inadequate heat treatment can cause tooth chipping and spalling.
- Prevention: Ensuring adequate gear material strength, using high-quality materials, and performing proper heat treatment can prevent chipping and spalling. Avoiding shock loads and overloading is also essential.
7. Misalignment:
- Root Cause: Misalignment between mating gears can cause uneven load distribution and accelerated wear.
- Prevention: Precise gear alignment and ensuring proper assembly and installation are crucial to prevent misalignment-related failures.
To prevent gear failures effectively, routine maintenance and inspections should be conducted to detect early signs of wear or damage. Implementing condition monitoring techniques, such as vibration analysis and oil analysis, can help identify potential issues before they escalate into failures.
Furthermore, using advanced design and simulation tools during the gear design phase can optimize gear geometry and materials for specific applications, enhancing overall performance and reliability.
Gear failure analysis and prevention in straight bevel gear systems require a comprehensive approach, encompassing proper gear design, selection of suitable materials, correct manufacturing processes, adequate lubrication, and regular maintenance practices. By proactively addressing potential failure modes, industries can ensure the longevity and reliability of their gear systems.