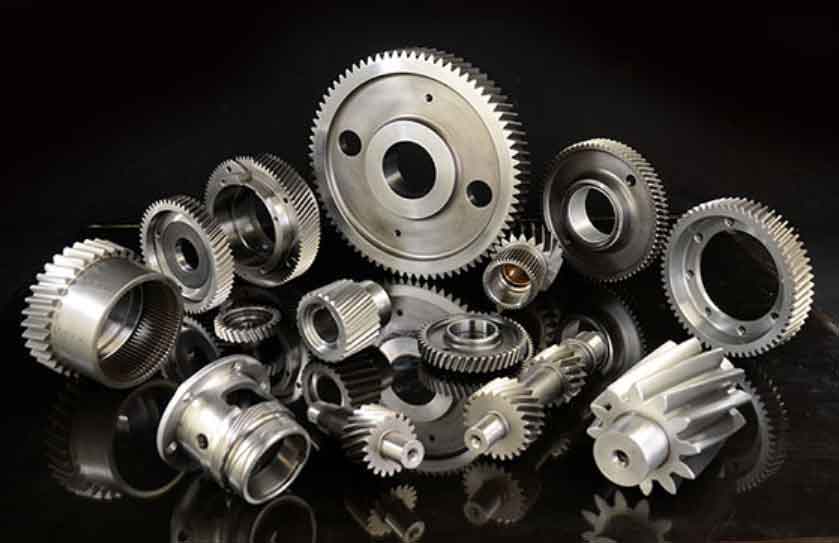
Optimizing gear meshing is crucial to achieving maximum efficiency and performance with helical gears. Proper gear meshing ensures smooth transmission of power, reduces noise and vibration, and minimizes wear and fatigue on gear teeth. Here are some tips for optimizing gear meshing with helical gears:
- Correct Gear Tooth Profile: Ensure that the helical gears have the correct tooth profile and helix angle. The tooth profile should match the gear’s module (pitch), pressure angle, and helix angle to ensure proper engagement and minimal sliding friction during meshing.
- Precision Manufacturing: Use high-quality manufacturing processes and equipment to produce precise gear teeth. Accurate gear manufacturing reduces variations in tooth profile and minimizes backlash, ensuring smooth and efficient meshing.
- Proper Tooth Contact Pattern: Check the tooth contact pattern during assembly. The ideal contact pattern is a line contact, ensuring even distribution of load across the gear teeth. Adjust the gear mesh position if necessary to achieve the desired contact pattern.
- Backlash Adjustment: Properly adjust the backlash (clearance) between the meshing helical gears. Adequate backlash is essential to accommodate thermal expansion and ensure smooth engagement without binding or excessive friction.
- Lubrication: Use the appropriate lubricant for the gear system. Proper lubrication reduces friction, wear, and noise during meshing. Choose a lubricant with good load-carrying capacity and temperature resistance to maintain gear efficiency.
- Alignment: Ensure accurate alignment of the shafts and gear components. Misalignment can lead to premature wear, noise, and reduced efficiency. Use precision alignment tools and techniques during gear assembly.
- Load Distribution: Optimize the gear system to evenly distribute loads among multiple gear pairs. Uniform load distribution prevents overloading of individual gear teeth and extends the overall system’s life.
- Quality Control: Implement strict quality control measures throughout the manufacturing process. Use non-destructive testing methods to identify defects and irregularities in the gears, ensuring only high-quality gears are used in the system.
- Material Selection: Choose appropriate materials for the helical gears based on the application’s requirements. Consider factors such as load, speed, and environmental conditions to select materials with the right strength, hardness, and wear resistance.
- Continuous Monitoring: Regularly monitor the gear system’s performance, including temperature, vibration, and noise levels. Early detection of any issues allows for timely maintenance and prevents catastrophic failures.
By following these tips, engineers and manufacturers can optimize gear meshing with helical gears, leading to efficient, reliable, and durable gear systems. Well-optimized gear meshing ensures smoother motion, reduced energy losses, and extended gear life, making helical gears an ideal choice for a wide range of mechanical applications.