Gear forging is a versatile manufacturing process that unleashes the potential of customized gear manufacturing. It offers several advantages for creating gears tailored to specific requirements. Here’s how gear forging enables the realization of customized gears:
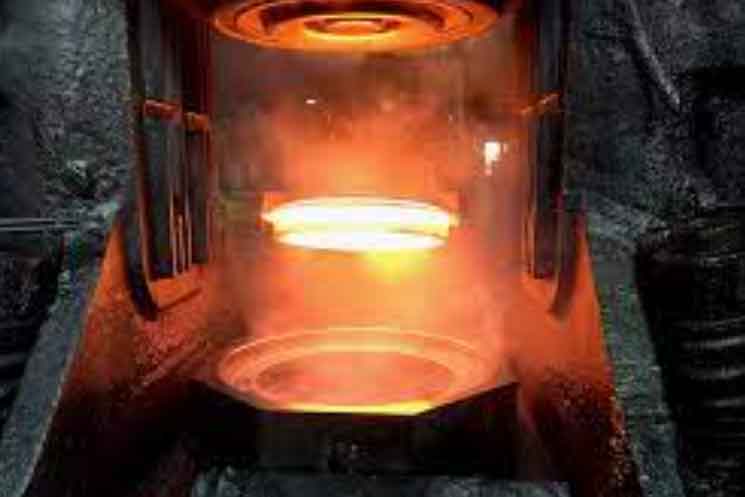
- Flexibility in Gear Design: Gear forging provides design flexibility, allowing the creation of gears with customized features and specifications. The forging process allows for the production of complex gear geometries, including internal gears, helical gears, spur gears, and bevel gears, among others. Customized gear designs can be developed to optimize performance, load capacity, efficiency, and other application-specific factors.
- Material Selection: Gear forging enables the use of a wide range of materials to suit specific application requirements. Different materials, such as carbon steels, alloy steels, stainless steels, and non-ferrous alloys, can be forged into gears with varying properties. The material selection can be tailored to achieve desired characteristics like strength, wear resistance, corrosion resistance, and heat resistance, ensuring the gear’s suitability for the intended application.
- Tailored Gear Properties: Gear forging allows for the customization of material properties to meet specific performance demands. Through heat treatment processes, such as quenching and tempering, the mechanical properties of the forged gears can be precisely controlled. Customized heat treatment parameters, such as temperature, duration, and cooling rate, enable the optimization of hardness, toughness, and other material properties required for the intended application.
- Enhanced Gear Strength: Gear forging results in gears with superior strength and durability. The controlled deformation and grain flow alignment during forging create a forged gear with a refined microstructure and improved mechanical properties. The customized gear can be designed and forged to withstand high loads, shock, and fatigue, ensuring reliable performance and long service life.
- Cost-Effective Production: Gear forging offers cost advantages in customized gear manufacturing. The process allows for efficient material utilization, minimizing waste and reducing material costs. Additionally, the high strength and reliability of forged gears often result in lower maintenance and replacement costs over the gear’s operational lifespan.
- Consistency and Reproducibility: Gear forging ensures consistency and reproducibility in the manufacturing process. Once the forging parameters and die designs are established for a particular gear, the process can be repeated to produce multiple identical gears with consistent quality and performance. This reliability is crucial when manufacturing gears for machinery that requires standardized or interchangeable components.
- Shorter Lead Times: With gear forging, customized gears can be produced within shorter lead times compared to other manufacturing methods. The streamlined and efficient forging process allows for rapid production once the forging die is prepared. This is especially advantageous for time-sensitive projects or industries with quick turnaround requirements.
- Integration with Additional Processes: Gear forging can be integrated with other processes to further customize gears. After forging, the gears can undergo additional machining, grinding, or surface treatment operations to achieve specific dimensional tolerances, surface finishes, or other desired features. This integration allows for a comprehensive approach to gear customization, meeting precise specifications and performance criteria.
Gear forging, with its customization capabilities, plays a significant role in meeting the diverse gear requirements of industries such as automotive, aerospace, energy, and heavy machinery. By leveraging the potential of gear forging, manufacturers can unleash the full potential of customized gear manufacturing, delivering gears that are precisely tailored to meet the unique demands of each application.