Precision forging is a specialized manufacturing process that allows for the creation of complex metal shapes with high accuracy and efficiency. It involves using a combination of advanced techniques and equipment to shape metal into intricate geometries that are difficult or impossible to achieve with traditional forging methods.
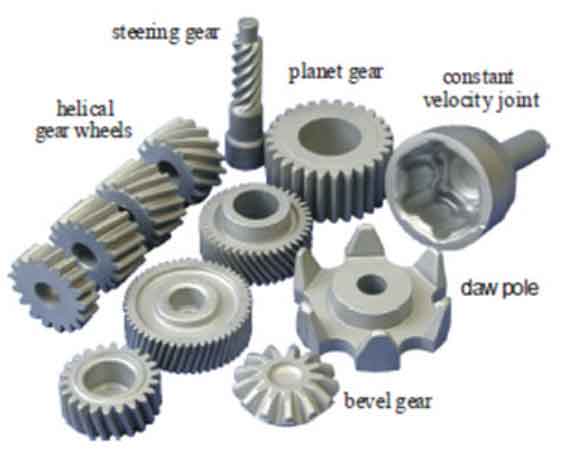
The process of precision forging involves several key steps:
- Die Design: A crucial aspect of precision forging is the design of the die, which determines the final shape and dimensions of the component. Computer-aided design (CAD) software is typically employed to create a detailed die design that matches the desired part geometry.
- Material Selection: The choice of material is important in precision forging. Metals with good forgeability, such as steel, aluminum, titanium, and their alloys, are commonly used. The material’s properties, including strength, ductility, and thermal characteristics, must be considered to ensure successful shaping.
- Heating: The workpiece, usually a metal billet, is heated to a specific temperature to increase its plasticity. This temperature varies depending on the material being forged and is carefully controlled to ensure optimal forging conditions.
- Precision Forging: Once heated, the billet is placed into the die and subjected to high pressure. The pressure is applied using hydraulic or mechanical presses, causing the metal to flow and fill the die cavities. The combination of pressure and temperature allows for precise shaping of the material according to the die design.
- Cooling and Finishing: After the desired shape is achieved, the forged component is cooled to room temperature. Depending on the specific requirements, additional steps such as heat treatment, machining, surface treatment, or inspection may be performed to achieve the desired final properties and surface finish.
Precision forging offers several advantages in the production of complex metal shapes:
- Design Complexity: Precision forging enables the creation of intricate shapes, including thin-walled sections, undercuts, and internal features. The ability to form complex geometries in a single operation eliminates the need for multiple manufacturing steps, reducing costs and lead times.
- Material Optimization: Precision forging minimizes material waste by closely matching the final shape to the desired part, resulting in near-net shape components. This reduces the amount of material that needs to be machined or removed, leading to cost savings and improved material utilization.
- Improved Mechanical Properties: The controlled deformation during precision forging enhances the mechanical properties of the forged components. The grain structure of the metal is refined, resulting in improved strength, toughness, and fatigue resistance compared to cast or machined parts.
- High Production Efficiency: Precision forging allows for the production of complex components at high volumes with consistent quality. The process is highly automated and repeatable, enabling efficient mass production and reducing labor costs.
- Cost Reduction: By reducing material waste, minimizing machining requirements, and streamlining the manufacturing process, precision forging offers cost savings over other manufacturing methods. It also eliminates or reduces the need for additional operations such as welding or assembly.
Precision forging finds applications in various industries, including automotive, aerospace, defense, energy, and medical. It is commonly used to manufacture components such as gears, shafts, valves, turbine blades, connecting rods, and structural parts where high strength, reliability, and dimensional accuracy are crucial.
In summary, precision forging unveils the secrets of complex metal shaping by combining advanced die design, material selection, and controlled forging processes. It enables the production of intricate and accurate metal components with improved mechanical properties and cost efficiency, revolutionizing the way complex shapes are manufactured in various industries.