Gear forgings play a crucial role in driving efficiency and reliability in gear manufacturing processes. Here are several ways in which gear forgings contribute to these important aspects:
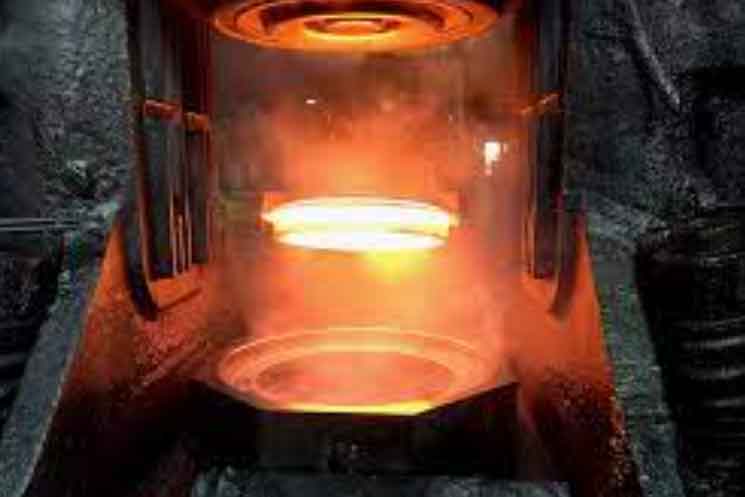
- Increased Strength and Durability: Gear forgings are known for their superior strength and durability compared to other manufacturing methods like casting or machining. The forging process aligns the grain structure of the metal, resulting in a stronger and more resilient gear. This enables gears to withstand high loads, shocks, and vibrations without deformation or failure, ensuring long-lasting performance and reliability.
- Enhanced Fatigue Resistance: Gears are often subjected to repetitive loading cycles, leading to fatigue failure over time. Gear forgings, with their refined grain structure and absence of defects, exhibit improved fatigue resistance. They can endure millions of load cycles without experiencing significant wear or performance degradation, enhancing overall gear reliability.
- Optimal Material Utilization: Gear forgings offer excellent material utilization due to their near-net shape production capabilities. By forging gears close to their final shape, the amount of material wasted during subsequent machining operations is minimized. This leads to cost savings in material procurement and reduced machining time, resulting in improved manufacturing efficiency.
- Tighter Tolerances and Dimensional Accuracy: The precision achieved in gear forgings contributes to tighter tolerances and dimensional accuracy. By utilizing advanced tooling and die designs, gear manufacturers can produce gears with precise tooth profiles, pitch diameters, and other critical dimensions. This ensures accurate gear meshing, smooth operation, and improved overall gear performance.
- Consistent Material Properties: The forging process provides uniform and consistent material properties throughout the gear, ensuring predictable and reliable performance. The controlled heating and deformation during forging eliminate internal defects, such as voids, porosity, or inclusions, which can compromise the integrity of the gear. Gear forgings exhibit consistent hardness, strength, and toughness across the entire component, enhancing reliability and reducing the risk of premature failures.
- Design Flexibility: Gear forgings offer design flexibility, allowing for the production of complex gear geometries that meet specific application requirements. The forging process can accommodate a wide range of gear shapes, sizes, and tooth profiles. This flexibility enables gear manufacturers to tailor gears to their intended use, optimizing performance, efficiency, and reliability for various demanding applications.
- Streamlined Production Process: Gear forgings streamline the production process by reducing the number of manufacturing steps required. Near-net shape forgings minimize the need for extensive machining, resulting in shorter lead times and improved overall production efficiency. The simplified process also reduces the potential for errors, rework, and material waste, contributing to increased productivity and cost-effectiveness.
- Quality Assurance: Gear forgings undergo stringent quality control measures, ensuring that only components meeting the required specifications are utilized. Non-destructive testing techniques, dimensional inspections, and material analysis are employed to verify the integrity and quality of the gears. This rigorous quality assurance process enhances the reliability and performance of the gears in demanding applications.
Gear forgings provide a reliable and efficient solution for manufacturing high-performance gears in various industries. By leveraging the inherent advantages of gear forgings, manufacturers can achieve optimized gear designs, improved material utilization, enhanced durability, and consistent quality, ultimately driving efficiency and reliability in gear manufacturing processes.