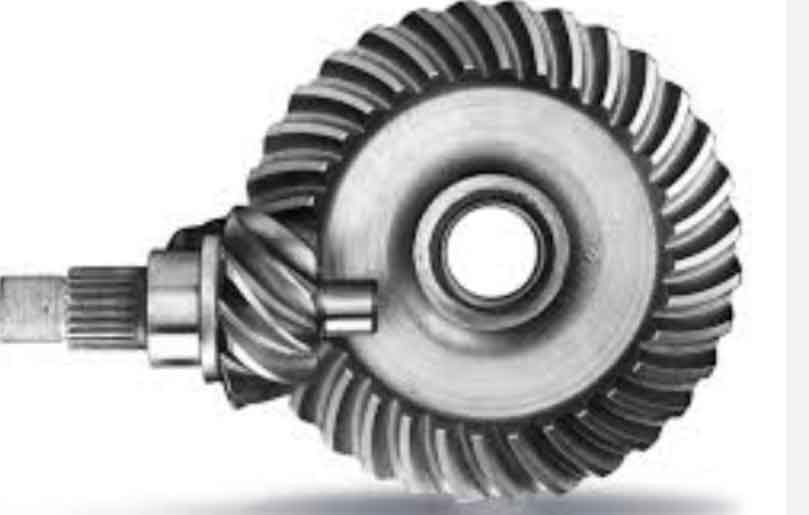
Hypoid gears represent a redefined gear geometry that showcases precision engineering at its finest. Their unique design and manufacturing intricacies make them a standout choice for demanding applications that require precise power transmission and high torque capacity. Let’s explore how hypoid gears redefine gear geometry through precision engineering:
1. Logarithmic Spiral Tooth Profile:
The tooth profile of hypoid gears is based on a logarithmic spiral, which is a key feature defining their geometry. This specialized tooth profile ensures smooth and continuous tooth engagement, reducing noise, vibration, and wear during meshing.
2. Non-Intersecting Axes:
The most distinctive aspect of hypoid gears is their offset axes. Unlike conventional bevel gears, where the axes intersect, hypoid gears have non-intersecting axes, enabling a more versatile and space-efficient gearbox design.
3. Optimal Contact Pattern:
The offset axes and logarithmic spiral tooth profile create an optimal contact pattern, distributing the load evenly across the tooth surface. This contact pattern enhances the gears’ torque capacity and load-carrying ability.
4. Advanced Manufacturing Techniques:
Precision engineering in hypoid gears involves advanced manufacturing techniques, such as computer numerical control (CNC) machining and gear grinding. These techniques ensure precise and consistent gear tooth profiles, leading to high-quality gears with minimal tooth deviations.
5. Gear Design Flexibility:
The offset design of hypoid gears allows for various gear configurations and the integration of additional features within the same assembly. This design flexibility enables engineers to tailor gearboxes to specific application requirements.
6. Finite Element Analysis (FEA):
Precision engineering often involves the use of FEA to analyze the structural integrity and performance of hypoid gears. FEA simulations help optimize gear design, material selection, and heat treatment processes to ensure reliable and efficient operation.
7. Gear Tooth Root Fillets:
The precision engineering of hypoid gears includes carefully designed root fillets, which minimize stress concentrations at the tooth root. This feature increases the gears’ fatigue strength and extends their service life.
8. Quality Control and Inspection:
Precision manufacturing of hypoid gears involves strict quality control and inspection procedures. Advanced metrology tools are used to measure gear tooth profiles, runout, and surface finish to ensure compliance with tight tolerance requirements.
9. Application-Specific Design:
Hypoid gears are often custom-designed for specific applications. Engineers consider factors such as load requirements, operating conditions, and gear ratio optimization to create tailored solutions that meet the desired performance criteria.
10. Lubrication and Surface Treatment:
Precision engineering extends to the choice of lubrication and surface treatments, ensuring smooth gear operation, wear resistance, and corrosion protection.
Hypoid gears exemplify precision engineering through their innovative gear geometry, non-intersecting axes, and advanced manufacturing techniques. The precise tooth profile, optimal contact pattern, and superior torque capacity make hypoid gears suitable for various high-performance applications, including automotive differentials, industrial machinery, and aerospace systems, where precision and reliability are paramount.