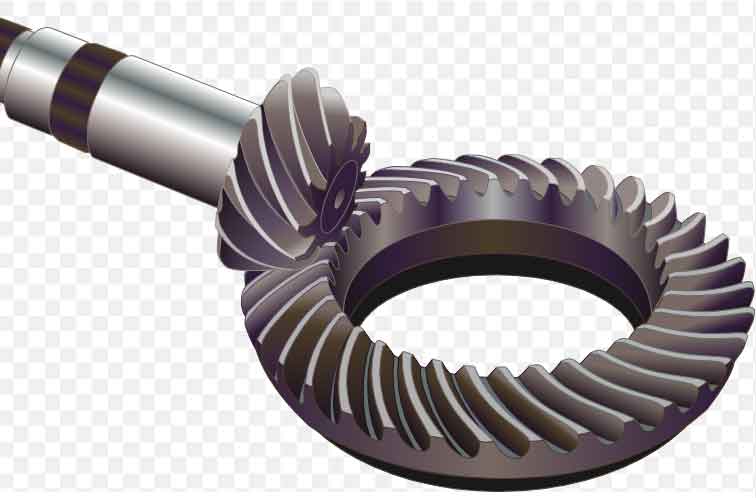
Optimizing gear meshing is crucial for achieving maximum efficiency with spiral bevel gears. Here are some tips to enhance gear meshing and improve overall performance:
1. Precise Gear Design:
Ensure that the spiral bevel gears are designed with accurate tooth profiles, pitch, and helix angles. Use advanced computer-aided design (CAD) software and simulation tools to analyze the gear geometry and tooth contact patterns.
2. Proper Gear Pairing:
Select gears with matching specifications and gear ratios to ensure smooth meshing and minimize unnecessary load on the gear teeth. Proper gear pairing helps distribute the load evenly across the gear teeth.
3. Quality Manufacturing:
Choose a reputable manufacturer with expertise in producing high-quality spiral bevel gears. Precise machining and heat treatment processes are essential for ensuring accurate gear geometry and surface finish.
4. Lubrication:
Use a suitable lubricant that provides sufficient film thickness and reduces friction between the gear teeth during operation. Proper lubrication is critical for minimizing wear and extending the gear’s lifespan.
5. Backlash Control:
Minimize backlash by maintaining precise gear tooth contact. Proper alignment and adjusting the gear mesh clearance can help reduce backlash and ensure accurate motion transmission.
6. Tooth Contact Analysis:
Perform tooth contact analysis to identify potential contact abnormalities and make necessary adjustments to improve gear meshing. Analyzing tooth contact patterns helps optimize gear performance and minimize noise and vibration.
7. Noise Reduction Techniques:
Employ noise reduction techniques, such as crown modifications and lead crowning, to improve gear meshing and reduce noise generated during operation.
8. Gear Inspection and Maintenance:
Regularly inspect the gears for signs of wear or damage and perform maintenance as needed. Timely maintenance can prevent premature failures and maintain optimal gear performance.
9. Proper Mounting and Alignment:
Ensure proper mounting and alignment of the gears to maintain correct gear meshing. Misalignment can lead to uneven loading and premature gear failure.
10. Material Selection:
Choose materials with suitable properties for the specific application to ensure durability and performance. Factors such as load capacity, wear resistance, and temperature tolerance should be considered.
11. Avoid Overloading:
Avoid exceeding the gear’s maximum torque capacity to prevent premature failure. Operating gears within their specified limits ensures optimal performance and longevity.
12. Reduce Friction and Wear:
Implement measures to minimize friction and wear between gear teeth, such as using surface treatments or coatings, to improve overall efficiency and extend gear life.
By following these tips, engineers can optimize gear meshing for maximum efficiency with spiral bevel gears. Proper design, manufacturing, lubrication, and maintenance practices are essential for ensuring smooth and reliable gear operation in various applications.