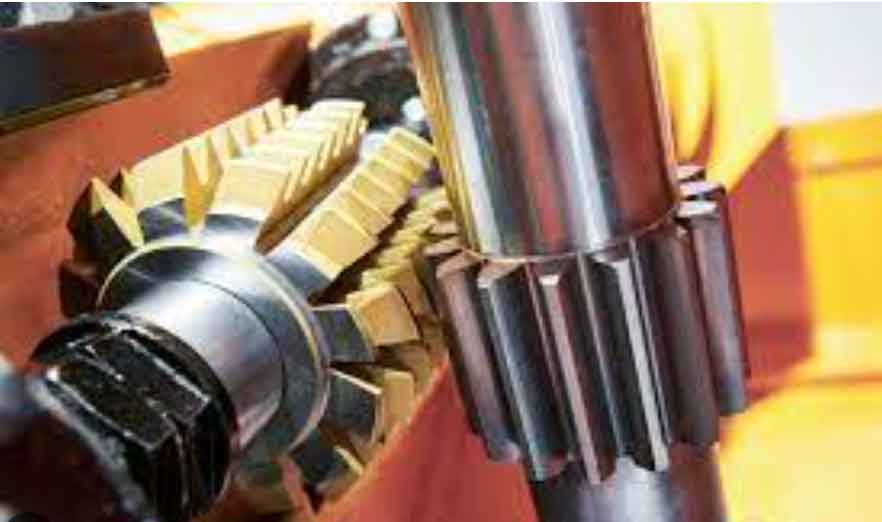
Gear hobbing machines are specialized equipment used for the precision machining of gears through the hobbing process. These machines come in various types and configurations to accommodate different gear manufacturing needs. Let’s explore the types of gear hobbing machines, their key features, and advancements in the field:
Types of Gear Hobbing Machines:
- Horizontal Gear Hobbing Machines: In horizontal gear hobbing machines, the gear blank is mounted horizontally on the machine’s work spindle, and the hob is mounted on a horizontal arbor. This type of machine is commonly used for hobbing external gears.
- Vertical Gear Hobbing Machines: In vertical gear hobbing machines, the gear blank is mounted vertically on the machine’s work spindle, and the hob is mounted on a vertical arbor. These machines are suitable for hobbing internal gears, such as ring gears and gear segments.
- Universal Gear Hobbing Machines: Universal gear hobbing machines have the flexibility to hob both external and internal gears. They can be configured for horizontal or vertical hobbing, making them versatile for various gear types.
Key Features of Gear Hobbing Machines:
- Hob Head: The hob head holds and drives the hob, allowing it to cut the gear teeth. It may have multiple axes of movement for adjusting the hob position and cutting parameters.
- Work Spindle: The work spindle holds and rotates the gear blank during the hobbing process. It provides the motion required for gear generation.
- Hob Arbor: The hob arbor holds and rotates the hob. It may have swiveling capabilities to set the hob at the correct helix angle for helical gears.
- Feed Mechanism: The feed mechanism controls the radial and axial feed of the hob to produce the desired gear tooth profile.
- Control System: Modern gear hobbing machines are equipped with advanced CNC (Computer Numerical Control) systems that offer precise control over cutting parameters, ensuring high accuracy and repeatability.
- Automation and Tool Changers: Some gear hobbing machines are equipped with automatic tool changers and workpiece loading systems, enabling continuous and efficient production.
Advancements in Gear Hobbing Machines:
- High-Speed Gear Hobbing: Advancements in machine design and cutting tool materials have enabled high-speed gear hobbing, leading to increased productivity and shorter cycle times.
- Multi-Axis CNC Control: Modern gear hobbing machines feature multi-axis CNC control, allowing for complex gear profiles and precise control over cutting movements.
- Hob Design and Optimization: Advancements in hob design, such as coated hobs and optimized tooth profiles, improve cutting efficiency and tool life.
- In-Process Metrology: Some gear hobbing machines incorporate in-process metrology systems to measure gear parameters during cutting, enabling real-time adjustments for higher accuracy.
- Energy Efficiency: Newer gear hobbing machines may incorporate energy-saving features to reduce power consumption during operation.
- Industry 4.0 Integration: Gear hobbing machines are being integrated into Industry 4.0 initiatives, enabling connectivity and data exchange for improved process monitoring, maintenance, and productivity.
Overall, advancements in gear hobbing machines focus on improving efficiency, accuracy, and versatility. These advancements allow gear manufacturers to produce high-quality gears with increased productivity and reduced manufacturing time, meeting the demands of various industries that rely on precision gears for their applications.