Gear shaping is a precise and efficient process that plays a critical role in enhancing precision and efficiency in gear manufacturing. Here are several ways in which gear shaping contributes to achieving high precision and efficiency:
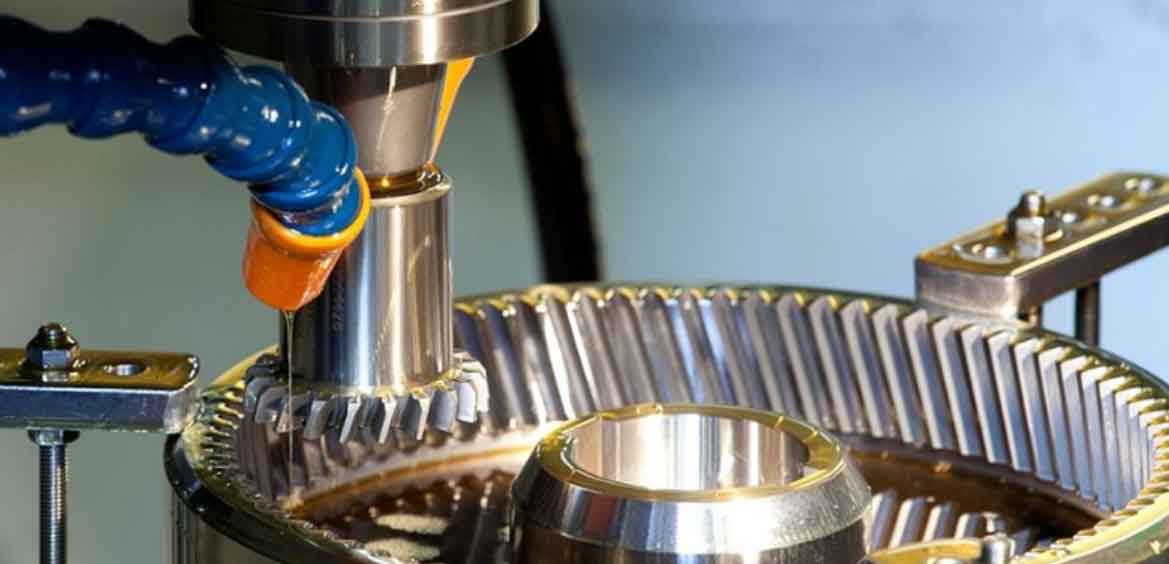
- Accurate Tooth Profile Generation: Gear shaping enables the generation of precise gear tooth profiles. By using a shaper cutter with carefully designed tooth geometry and controlling the cutter’s movement, gear shaping ensures the accurate formation of gear teeth. This results in gears with correct involute profiles, tooth thickness, and tooth spacing, leading to smooth and efficient gear operation.
- Consistent Tooth Spacing: Gear shaping machines allow for precise control of the cutter’s feed and reciprocating stroke, ensuring consistent tooth spacing throughout the gear. This uniformity is crucial for smooth gear meshing and efficient power transmission. By maintaining precise tooth spacing, gear shaping eliminates potential issues such as backlash and uneven load distribution.
- High Production Efficiency: Gear shaping is known for its high production efficiency compared to other gear manufacturing methods. Once the machine setup is optimized, gear shaping can produce multiple gear teeth simultaneously, leading to faster gear production rates. The continuous reciprocating motion of the shaper cutter allows for efficient material removal, reducing cycle times and improving overall manufacturing productivity.
- Suitability for Mass Production: Gear shaping is well-suited for mass production due to its efficiency and repeatability. Once the cutting parameters are established, gear shaping machines can consistently produce gears with high precision and minimal variation from part to part. This makes gear shaping an ideal choice for industries that require large quantities of gears with consistent quality, such as automotive and industrial equipment manufacturing.
- Versatility in Gear Types: Gear shaping can be applied to various gear types, including spur gears, helical gears, internal gears, and more. The versatility of gear shaping machines allows manufacturers to produce a wide range of gear sizes, tooth profiles, and configurations. This flexibility enables gear manufacturers to meet diverse customer requirements and cater to different applications.
- Automation and Integration: Gear shaping machines can be integrated into automated production lines, further enhancing efficiency and precision. Automation reduces manual intervention, increases process reliability, and enables seamless integration with other manufacturing operations, such as gear inspection and post-processing. Automated gear shaping systems can significantly improve overall production efficiency and reduce human error.
- High-Quality Surface Finish: Gear shaping produces gears with excellent surface finish quality. The continuous cutting action of the shaper cutter results in smooth tooth surfaces, reducing friction, wear, and noise during gear operation. The superior surface finish achieved through gear shaping contributes to the overall efficiency and durability of the gear system.
By leveraging the precision and efficiency of gear shaping, manufacturers can achieve high-quality gears that meet strict performance requirements. Whether it’s for automotive, aerospace, or industrial applications, gear shaping plays a vital role in ensuring the reliable and efficient operation of gear systems.